man — Википедия
Материал из Википедии — свободной энциклопедии
У этого термина существуют и другие значения, см. man (значения).man (от англ. manual — руководство) — команда Unix, предназначенная для форматирования и вывода справочных страниц. Поставляется почти со всеми UNIX-подобными дистрибутивами. Каждая страница справки является самостоятельным документом и пишется разработчиками соответствующего программного обеспечения.
Чтобы вывести справочное руководство по какой-либо команде (или программе, предусматривающей возможность запуска из терминала), можно в консоли ввести:
Например, чтобы посмотреть справку по команде ls, нужно ввести man ls.
Для навигации в справочной системе man можно использовать клавиши ↑ и ↓ для построчного перехода, PgUp и PgDn для постраничного перехода вверх и вниз соответственно.
При просмотре больших страниц удобно воспользоваться поиском, для чего следует нажать
Для получения краткой справки по командам и горячим клавишам справочной системы нужно нажать H (Help — помощь).
Для выхода из справочной системы используется клавиша Q (Quit — выход).
Для получения детальной инструкции по использованию команды используется конструкция
Справочные страницы поделены на 8 стандартных разделов [1] и один дополнительный[2]. Каждый из разделов соответствует той или иной тематике в рамках установленной операционной системы.
Раздел | Краткое описание[1] |
---|---|
1 | Прикладные программы и команды оболочки |
2 | Системные вызовы ядра (функции языка Си) |
3 | Библиотечные вызовы (функции различных библиотек, установленных в систему) |
4 | Специальные файлы (находящиеся обычно в каталоге /dev) |
5 | Форматы файлов и соглашения |
6 | Игры |
7 | Различные описания, соглашения и прочее |
8 | Команды администрирования системы, которые обычно запускаются от имени суперпользователя |
9 | Ядро операционной системы (нестандартный раздел)[2] |
Номер раздела в команде man указывается вторым аргументом, перед названием справочной страницы. Если номер раздела опущен, то поиск справочной страницы ведётся по всем разделам по порядку.
man passwd #раздел 1 man 1 passwd #раздел 1 man 5 passwd #раздел 5
- Переводы man-страниц на русский язык
![]() Команды Unix | |
---|---|
как собирают грузовики MAN в России
Так повелось, история Петербурга неразрывно связана с европейскими государствами. Отчего за градом прочно закрепился имидж европейской столицы России. Новая Голландия, Немецкая Слобода… Немало и других названий подчеркивают родство с Западной Европой. А с недавних пор и индустриальный пригород начал обзаводиться такими достопримечательностями. Порукой тому завод по сборке грузовиков MAN в Шушарах
Визит на завод откладывался несколько раз. Тому было много причин. Сначала еще нечего было показывать, потом было просто недосуг. Затем и вовсе грянул кризис. Однако, следуя мудрому совету о том, что именно в кризис и закладывается основа для будущего, руководство российского офиса MAN все же решилось приоткрыть завесу над своим сборочным производством в Санкт-Петербурге. Не скрою, был приятно удивлен, когда у входа в офисное здание меня встретил местный «гид» и предложил сразу, без лишних экивоков, пройти в производственный корпус. На мой резонный вопрос, что, может, стоит еще кого подождать ради приличия, был получен короткий ответ, что больше никого и не будет. В общем, полный эксклюзив.
Итак, к реализации проекта компания MAN приступила в 2011 году. Территория и сооружения находятся в долгосрочной аренде. В середине 2013 года сборочное производство вступило в строй действующих. Этому предшествовало получение лицензии на опасный производственный объект, которая, собственно, и позволяла начать сборку грузовиков. У завода один-единственный покупатель — ООО «МАН Трак энд Бас РУС».
ООО «МАН Трак энд Бас Продакшн РУС» является 100-процентной дочерней организацией MAN Truck & Bus AG. Предприятие достаточно сильно интегрировано в производственную систему головного предприятия. Дело доходит до того, что все компьютеры «думают», что их операторы находятся непосредственно в Германии. На заводе действует единая для всех предприятий компании система МРS, и все производственные процессы выполняются по тем же стандартам, что и, скажем, в Мюнхене (логистика, производство и т. п.).
Производственный корпус, расположенный под единой крышей, условно разделен на несколько зон. Зона логистики, где хранятся компоненты будущих грузовиков. Основная доля компонентов приходит из Европы. Зона «распаковки» или, если угодно, комплектации. Производственная линия. Цех окраски. Приемка. Модификационный центр по доводке специальных исполнений.
Общая площадь завода составляет около 30 тыс. м2. При этом на долю непосредственно производства приходится 19,5 тыс. м2. Офисная часть, расположенная над зоной логистики, занимает 1,2 тыс. м2. Персонал завода на момент посещения составлял порядка 90 человек. 47 из них — производственные рабочие. Завод рассчитан на выпуск 6000 грузовиков в год при двухсменной работе. Это приблизительно 15 грузовиков в смену при такте в 27 минут (ограничение по цеху окраски). На момент посещения завода такт сборки грузовика составлял 1 час 45 минут, что приблизительно соответствует сборке трех грузовиков в смену или 600 грузовиков в год. Это не ахти что, но такова ситуация на рынке. Ничего не попишешь.
Отдельная площадка отведена для кабин, поступающих из Австрии
Комплектующие для сборки грузовиков поступают с четырех основных производств MAN. CKD-боксы поступают из Зальцгиттера, из Нюрнберга приходят двигатели, из Мюнхена — мосты, кабины — из Австрии (MAN Steyr). Лонжероны и поперечины рам приходят от глобального поставщика MAN из Германии. Но самое интересное то, что коробки передач поставляются из Набережных Челнов — от СП «ZF-Кама». Нельзя сказать, что это те же самые КП, что и для КАМАЗа. Во всяком случае, то, что приходит на завод в Питер, полностью удовлетворяет немецкую сторону. Отсюда и достаточно высокий уровень локализации производства. В зависимости от модели процент колеблется от 20 с небольшим до 30. Именно это обстоятельство и позволило предприятию получить сертификат локального производителя с целью возможного участия в госзакупках.
Поставляемый из Зальцгиттера CKD-бокс включает в себя 5 ящиков, в которых размещается в среднем до 15 машинокомплектов. Под хранение кабин отведена специальная площадка. В целом на логистический комплекс приходится половина всех производственных площадей. Он напрямую связан с доками, к которым ежедневно приходят под разгрузку трейлеры с комплектующими. Несмотря на отлаженный механизм, идет постоянный процесс оптимизации комплектов, упаковки и всего того, что связано с поставкой комплектующих.
После того как все распаковано и разложено по местам, начинается непосредственно сборка грузовика. Лонжероны рамы устанавливаются на тележки, и начинается таинство сборки. Для того чтобы не запутаться во всем многообразии собираемых грузовиков, мелом на раме рисуют подсказки. На данном этапе технология сборочного процесса полностью идентична заводу в Мюнхене. Сборка рамы, точнее шасси, разбита на 5 постов. После собранное шасси проходит через ворота качества.
Как только рама приобретает законченные черты, внутризаводской номер уступает место VIN-коду, который набивается специальным устройством. Нумерация сквозная, поэтому каждый собранный грузовик легко отследить.
На логистический комплекс приходится половина всех производственных площадей
При сборке рамы в основном используется заклепочное соединение и специальный гидравлический инструмент с усилием в 30 тонн. Болтовые соединения не отвергаются. Технологическая особенность такова, что в одни и те же отверстия могут ставиться как заклепки, так и болты. Однако в места, отведенные специально под заклепки болт уже не поставить. Точность затяжки обычного соединения — с допуском 15 %, ответственного, влияющего на безопасность грузовика, — 5.
На каждом посту, или станции (по немецкой терминологии), масса инструкций как по сборке, так и по периодической поверке инструмента. Качеству сборки уделяется самое пристальное внимание.
Затем на подсобранную в перевернутом виде раму устанавливают мосты. После чего специальным устройством ей придают привычное положение для дальнейшей сборки. Далее происходит установка гидроусилителя руля и различных мелких деталей. Завершается процесс сборки шасси воротами качества. Здесь проверяются моменты затяжки всех соединений.
Сборка рамы начинается с подсказок
Несмотря на то, что большая часть комплектующих поступает на сборку уже в окрашенном виде, шасси проходит финальную окраску в соответствии со стандартами, принятыми на MAN. На участке подготовки к покраске часть деталей и узлов маскируется, часть подготавливается к окраске, тут же устраняются дефекты. Окраска осуществляется двумя малярами вручную, пневматическими краскораспылителями. Кстати, используются краски на водорастворимой основе, что не так часто встречается в производстве грузовиков. Сушится шасси в два этапа, затем оно остывает и только после этого поступает на сборочный конвейер.
Заключительная стадия сборки грузовика разбита на 6 этапов. На первых трех устанавливаются пневматические и электрические линии. Работа весьма ответственная, поскольку при сборке необходимо соблюсти массу требований, определяемых стандартами фирмы MAN.
Поскольку работа на сборке кропотливая и достаточно утомительная, помимо обеденного перерыва имеются еще два «перекура» по 15 минут.
На четвертой станции устанавливается радиатор и подсобранный двигатель. Производится подключение гидравлических линий и стыковка с коробкой передач. Ну и далее «свадьба» — подсобранная кабина устанавливается на шасси.
На последней станции устанавливаются колеса, аккумулятор. Машина практически полностью готова к тестированию и программированию.
А вот и российский VIN-код
Далее начинаются станции тестирования, но перед началом регламентных работ машина вывешивается, и из-под нее выводятся конвейерные тележки, которые направляются за новым шасси. Системы грузовика заполняются всеми необходимыми техническими жидкостями (антифриз, хладагент и т. п.), производится заправка топливом.
На первом этапе тестируется пневматика. Затем в работу включаются компьютерщики по программированию систем грузовика, для чего они связываются со специальным сервером в Мюнхене. Если выявляется какая-либо ошибка, то в работу вступает «вторая линия обороны» — MAN CADS. С ее помощью идентифицируется ошибка и способы ее устранения. Если же все нормально, производится первый запуск двигателя.
Далее грузовик, уже своим ходом, направляется на линию окончательных тестов. Перед въездом на тормозной стенд машина преодолевает «полосу препятствий» их неровностей. Таким образом, ее встряхивают, дабы все лишнее отделилось от грузовика. Попутно проводится осмотр на предмет добросовестности крепления деталей и узлов.
Пост установки силового агрегата в сборе и радиатора
На электронном тормозном стенде поочередно тестируются тормоза, ось за осью, а также блокировки дифференциалов (межколесного, межосевого). Затем грузовик заезжает на осмотровую яму, где производится общий осмотр, контроль подвески, установка развала/схождения передних колес.
На завершающем этапе автомобиль проходит через ворота качества. Здесь еще раз тестируется вся электрика и масса других нюансов, отражающих специфику конкретного грузовика. Далее следует дорожный тест протяженностью в 20 км по дорогам общей сети. Специально проработанный маршрут позволяет опробовать машину в различных режимах движения. Если все нормально, грузовик отправляется на весы. Производится контрольное взвешивание, и полученные данные заносятся в ПТС. На предприятии имеется водительский состав в количестве 10 человек, и в зависимости от необходимости они задействованы полностью или частично.
Подсобранное шасси перемещается на специальных тележках с приводом, расположенным под полом
Но на этом контроль качества не заканчивается. Есть так называемая система внутреннего аудита. Раз в три дня один грузовик проходит довольно сложную процедуру. Три дня его досконально осматривают, проверяют все системы, после чего автомобиль отправляется на более длительный дорожный тест (порядка 100 км) с более сложным характером движения.
По завершении аудита выставляется так называемый рейтинг, где «1» — это отлично, чем больше это значение, тем хуже показатель.
Чем интересна система. Сначала набираются баллы. Ноль баллов — отличный продукт. До пяти баллов — это то, что клиент никогда не увидит. До 15 баллов — это то, на что клиент обязательно обратит внимание. До 50 баллов — это серьезный дефект, который может повлечь за собой отказ какого-либо из агрегатов. До 100 баллов — возможный отказ одной из важных систем, такой грузовик никогда не покинет пределы завода. Далее набранные баллы пересчитываются по сложной формуле (происходит учет сложности конструкции конкретного грузовика).
В принципе, на заводе могут собирать все типы грузовиков MAN — TGL, TGM, TGS и TGX. Главное условие — устойчивый спрос.
Все грузовики проходят испытание на тормозном стенде с выводом показаний на электронное табло
Помимо основного производства на заводе имеется специальная выделенная зона — модификационный центр. На этой площадке проводится доработка машин под конкретные пожелания клиента. В частности, на одном из постов происходит переоборудование стандартного шасси MAN TGM под установку пожарного оборудования. Работа сложная, вплоть до изменения длины рамы. На другом посту идет дооснащение грузовиков TGS для работы с КДУ. Данные машины будут задействованы на обслуживании питерской КАД.
Компания «МАН Трак энд Бас Продакшн РУС» является весьма ответственным работодателем. Стандарты, принятые на производстве, превышают даже те, что действуют на территории РФ. Предприятие посетили ряд контролирующих государственных органов, особых замечаний к производству предъявлено не было. Предприятие предоставляет своим работникам достаточно привлекательный социальный пакет. Настолько привлекательный, что на данное производство желали бы попасть многие из ищущих работу в сфере автоиндустрии. Взять хотя бы такой факт: во время работы в цехе играет ненавязчивая музыка. Кстати, по просьбе самих работников.
Финальный осмотр грузовика. а далее дорожный тест
При выборе площадки изначально рассматривался вопрос о наличии достаточного количества квалифицированных кадров, в том числе и с опытом работы в автопроме. К тому времени за Петербургом уже закрепился имидж русского Детройта, поэтому с кадрами проблем не возникло. Большая часть работающих на заводе имеют автомобильное образование или опыт работы в автоиндустрии. Часть работников, на сборке и других ответственных направлениях, прошли стажировку от двух до трех месяцев на предприятиях компании в Западной Европе.
МИМОХОДОМ
При посещении завода не преминул воспользоваться случаем и задать пару-тройку вопросов руководителю предприятия — Станиславу Ковалеву.
— Понятно, что завод не влияет на сбыт продукции. Как решаются вопросы эффективности производства, в особенности в условиях кризиса в экономике?
— MAN имеет единые международные стандарты качества и эффективности, по которым работают производства во всем мире. Завод в Санкт-Петербурге не исключение. Мы не просто придерживаемся стандартов, но также стремимся совершенствовать производственные процессы и улучшать показатели. Результатом этой работы стали первые места по качеству, полученные нами в мае и июне 2015 года на внутреннем конкурсе среди заводов MAN.
— Вопрос локализации — один из главных для производства. Завод принимает в этом какое-либо участие или все «спускается сверху»?
— Как уже было отмечено выше, стандарты качества и эффективности едины для всех предприятий MAN. Тем не менее, решения по поставщикам принимаются с участием специалистов, работающих на заводе в Санкт-Петербурге. Локальные инженеры и служба закупок осуществляют аудит качества поставщиков и непосредственно участвуют в принятии решений.
— Кризисы приходят и уходят. Но именно в это время закладываются основы старта на перспективу. Что у вас в «загашнике» для лучших времен?
— MAN — глобальная компания. Наша сила в том, что мы неразрывно связаны с материнским брендом и входим в собственную сеть производственных предприятий концерна. Если по существу — выпуск в середине лета 1000-го грузовика. Другие наши начинания мы озвучим чуть позже.
ЕСТЬ 1000-Й!
В июле в Санкт-Петербурге сошел с конвейера первый грузовик MAN с четырехзначным порядковым номером, им стал седельный тягач белого цвета MAN TGS 19.400 4х2 BLS-WW.
Мероприятие по празднованию прошло в стенах завода и собрало работников предприятия и руководителей российского подразделения концерна MAN Truck & Bus. В мероприятии принял участие и вице-президент по качеству дивизиона Production truck концерна MAN Truck & Bus г-н Хольгер фон дер Хайде.
Генеральный директор ООО «МАН Трак энд Бас Продакшн РУС» Станислав Ковалев провел для гостей экскурсию по экспозиции грузовиков MAN, выпущенных в Санкт-Петербурге, а в производственном цеху подробно рассказал обо всех этапах сборки грузовых автомобилей и особенностях этого процесса. Г-н фон дер Хайде отметил, что команда работников завода обладает всеми необходимыми профессиональными компетенциями для выпуска продукции в соответствии с самыми высокими стандартами MAN, и грузовики, произведенные в Санкт-Петербурге, идентичны по качеству своим аналогам из Европы.
5 декабря состоялась официальная номинация поставщика штампованных деталей для завода Renault в Москве. По результатам тендера им стала компания «Альфа Автоматив Техноложиз», совместное предприятие АМО ЗИЛ и японской компании IHI Corporation. Поставки деталей от номинированного поставщика на завод «Автофрамос» начнутся в 2009 году, когда мощности завода увеличатся вдвое и достигнут 160 000 автомобилей в год.
«Альфа Автоматив Техноложиз» (AAT), cовместное предприятие АМО ЗИЛ и IHI Corporation, будет поставлять на Автофрамос более 70 наименований внешних кузовных и структурных деталей для всей гаммы Renault Logan. Прессовое производство AAT будет раcполагаться на производственных мощностях ЗИЛ.
Близость расположения завода «Автофрамос» и производства AAT будет способствовать эффективности сотрудничества между Renault и поставщиком, особенно в области качества и логистики.
Со стороны IHI Corporation, компании мирового уровня, специализирующейся на тяжелом машиностроении, организация производства будет осуществляться при поддержке мировых лидеров в производстве прессовой оснастки и штампованных деталей, японских компаний Ogihara и Fuji Technica.
ОАО Автофрамос инвестирует более 20 млн. евро в штамповую оснастку, за изготовление которой будет отвечать ААТ. Выбор поставщика металлопроката будет осуществляться партнерами совместно.
Локализация поставок штампованных деталей – очередной важный шаг в достижении цели 50%-ной локализации комплектующих для производства Renault в России в 2009 году. На сегодняшний день это партнерство представляет собой один из крупнейших контрактов на поставки между иностранным автопроизводителем и локальным поставщиком в России.
Сегодня Renault в России работает с 25 локальными партнерами-поставщиками, среди которых российские и совместные предприятия, а также филиалы иностранных компаний в России.
Хочу получать самые интересные статьи
Российский завод по сборке грузовиков MAN
Практически все основные мировые производители легковых и грузовых автомобилей имеют в России собственные сборочные мощности. С недавнего времени вокруг Санкт-Петербурга появился целый автомобильный кластер. Сегодня поговорим о заводе МАН в Шушарах, который появился в 2013 году.
Хотя сам завод начали строить еще в 2010 году, первые машины вышли с конвейера только через 3 года. В проект было инвестировано более 25 миллионов евро.
Сборку немецких грузовиков, которые получают российский VIN-код на своей раме, производят по технологии CKD. Это крупноузловая сборка. На завод приходят машинокомплекты с разных заводов МАН. Например кабины привозят из Австрии, а двигатели и мосты из разных городов Германии. Нельзя сказать, что российские поставщики не вносят свой вклад в сборку готового грузовика. Это не так. Ведь из Набережных Челнов приходят коробки передач марки ZF. Трансмиссия для грузовиков MAN производится на совместном предприятии “КАМАЗа” и европейского производителя коробок передач.
Правда пока процент локализации производства не превышает 30%. Показатель постоянно увеличивается за счет поиска новых российских поставщиков комплектующих. Как утверждают технологи отечественного завода немецких грузовиков российская сборка по качеству мало чем уступает тому же процессу на основном заводе в Мюнхене. Работники проводят те же операции и используют тот же инструменты. Кроме того проводится строгий контроль качества готовых грузовиков.
Технический центр грузовых автомобилей и прицепов “Собер-Авто” предлагает манипулятор МАН с различными техническими характеристиками. Под нужды любого заказчика можно подобрать идеальный вариант спецтранспорта. Машины на базе шасси TGS с разной колесной формулой, хорошим выбором силовых агрегатов порадуют надежностью и выносливостью.
Кроме сборки обычных тягачей и самосвалов на заводе МАН в России занимаются установкой дополнительного оборудования и выпуска специализированной техники. Например конкретному заказчику могут предложить пожарную машину или мусоровоз на базе шасси немецкого грузовика. За все время существования завода было собрано более 1000 грузовых машин, которые сегодня успешно эксплуатируются по российским дорогам. Современные мощные машины серии TGL, TGM, TGS и TGX выходят с конвейера завода ежедневно.
В результате кризиса, завод на некоторое время замораживал сборку автомобилей. Это в первую очередь было связано с резким падением рубля. Однако сегодня ситуация в экономике улучшается и требуются новые грузовые машины. Поэтому предприятие смотрит в будущее с оптимизмом.
Завод MAN в Санкт-Петербурге
За последние годы Россия стала крупным сборщиком автомобилей ведущих мировых марок. В нашей стране собирали и собирают машины Ford, General Motors, Hyundai, Toyota – список, как говорится, можно продолжать. И на рынке производителей коммерческой техники не наблюдалось затишья. Самым активным игроком среди сборщиков грузовиков стала компания Volvo Trucks, в июне 2007 г. Volvo и руководство области заключили инвестиционное соглашение о строительстве завода на площади 55 га «Калуга-Юг». Инвестиции в проект составили свыше 100 млн евро. На фоне шведов MAN выглядит гораздо скромнее – без малого 30 тыс. м2. И то, что сейчас называют заводом, до недавнего времени было складским комплексом, относящимся к расположенному неподалеку автогиганту GM. Вкладывать средства в сооружение путем его приобретения немцы не стали, взяв в аренду. Срок аренды, увы, не разглашается, и надеемся, что подающее надежды предприятие не постигнет судьба предыдущего эксплуататора недвижимого имущества. Питерский завод дополнил и без того немалую империю MAN, которая в 2014 г. насчитывала около 38 500 сотрудников по всему миру. В Германии работают четыре производственных площадки в городах Мюнхен, Нюрнберг, Зальцгиттер и Плауэн. Кроме них заводы компании есть в городах Штайр (Австрия), Познань, Стараховице и Кракове (Польша). Помимо Европы производства MAN функционируют в Анкаре, Питампуре (Индия) и в городах ЮАР – Олифантсфонтейне и Пайнтауне. Совокупные продажи в сегменте коммерческого транспорта составили 11 млрд евро и 120 000 грузовых автомобилей, автобусов и автобусных шасси MAN, Volkswagen и Neoplan. MAN Truck & Bus со штаб-квартирой в Мюнхене занял 16,4% и второе место на европейском рынке грузовиков полной массой от 6 тонн. В сегменте автобусов 10,8% всех новых регистраций в Европе пришлось на автомобили MAN и Neoplan. Этот результат ставит MAN Truck & Bus на третье место среди крупнейших европейских производителей автобусов массой от 8 тонн. Дочерняя компания MAN Latin America с головным офисом в Сан-Паулу, занимающая 27% рынка, сохраняет лидирующие позиции на рынке грузовиков от 5 т уже одиннадцатый год подряд.
Впервые о планах немецкого концерна MAN построить в Петербурге свой завод заговорили в 2011 году. К следующему году в Шушарах присмотрели производственную площадку и завод MAN начал работать в тестовом режиме. В Санкт-Петербурге завод MAN входит в сеть производственных предприятий концерна. Техническое оснащение соответствует единым стандартам. Между производственными линиями завода в Мюнхене и Санкт-Петербурге нет существенной разницы. Сейчас объем производства таков, что на его площадях в разобранном виде хранится до 45 грузовиков. Эти машинокомплекты приходят в ящиках, по большей части из Германии и Австрии. Там, в Зальцгиттере, готовят к отправке кронштейны, в Нюрнберге двигатели, в Штайре кабины и др. Подобный способ выпуска машин на территории России используют много иностранных производителей. Единственный крупный агрегат, поступающий на завод MAN и локализованный у нас, это коробка передач ZF. Напомним, совместное предприятие ОАО «КАМАЗ» и Zahnrad Fabrik было создано в январе 2005 года. Производит оно 9- и 16-ступенчатые механические коробки передач Ecomid (9S1310 TO) и Ecosplit (16S1820 TO). В 2016 году планируется освоить производство автоматизированных КП Ecomid Add-on. На сегодня основным потребителем продукции СП является ОАО «КАМАЗ» (более 95%), в 2012 стартовало производство трансмиссий для ОАО «АЗ УРАЛ» (9S1310 TO) и MAN в России (16S2520). В 2016 году запланировано производство коробок передач для ОАО «МАЗ» (16S1820 TO и 9S1310 TO).
Внутри корпусов
Фактически по оборудованию завод может собрать всю линейку MAN, для этого могло бы потребоваться лишь незначительное дооснащение. Но пока присутствует лишь пара моделей (TGS и TGM), и доминирует TGS в различных вариациях (2-х, 3-х, 4-осные) – как седельные тягачи, так и шасси. Согласно внутреннему распорядку детали, приходящие на завод, уже приписаны к конкретному грузовику – это создает некоторые проблемы, если какая-то запчасть оказывается поврежденной. Взять новую с полки не получится, а придется заказывать и ждать с очередной поставкой, иногда до месяца. Подобная ситуация и с крепежной мелочевкой (тоже поставляется из Германии) – она, конечно, не привязана к определенному ТС, но поставляется с крошечным запасом 5%. Такое управление производственными процессами, или MAN Production System, не что иное, как слегка измененная Toyota Production System. Там для минимизации запасов готовых изделий производственная система большей частью ориентирована на производство, основанное на заказах. Именно поэтому используется система «вытягивания», при которой последующие процессы обращаются к предыдущим, чтобы взять необходимые изделия.
Производственный план, в котором обозначены необходимые модели автомобилей, их количество и срок изготовления, отправляется на конечную сборочную линию. Затем метод передачи материалов разворачивается на 180 градусов. Чтобы получить узлы для окончательной сборки, конечная сборочная линия обращается к сборочной линии узлов с указанием строго необходимого наименования и количества узлов и сроков их поставки. Так производственный процесс движется от стадии готовой продукции к отделу заготовки сырья. Каждое звено цепочки процесса, организованного по принципу «точно вовремя», соединено и синхронизировано с другими.
По этому принципу собирают грузовики на двух линиях – изготовления рамы и окончательной сборки, которые состоят из пяти и шести станций (мест сборки) соответственно, что почти в пять раз короче, чем, например, на заводе в Германии. Длина линии и, соответственно, количество станций прямо пропорционально влияет на производительность. Ресурс по выпуску завода в Шушарах – всего 6000 грузовиков в год в две смены. В переводе на возможные суточные достижения это 15-16 грузовиков, а реально сейчас завод выпускает четыре грузовых автомобиля в день.
На линии сборки рамы на нее наносят российский vin-номер, последние четыре цифры которого имеют сквозную нумерацию – и всего месяц назад из ворот предприятия вышел тысячный экземпляр. Для удобства установки кронштейнов и другого оборудования сборка рамы осуществляется осями вверх. Раму с поперечинами соединяют клепки с усилием склепки не менее 30 тонн. Болтовое соединение проще при монтаже, но дороже при применении. Совсем от болтов с гайками не отказываются – их используют, когда обнаруживают бракованную заклепку. Затягивают гайки (и не только на раме) – тарированными ударными гайковертами с погрешностью недозатягивания 15%. После них соединение дополнительно проверяют динамометрическими ключами предельного типа. Хотя для особо ответственных деталей (стремянок рессор и крепления рулевого механизма) применяют гайковерты с точностью до 2%, после их затяжки дополнительной протяжки не требуется. Поступающие на завод узлы и агрегаты могут быть окрашены либо не иметь защитного покрытия. Несмотря на это, собранные шасси (без кабин, колес и проводки) дополнительно покрывают слоем краски на водной основе. По стандартам MAN cлой покрытия не может быть меньше 90 мкм. Именно покрасочная камера, если так можно выразиться, тормозит линии, «такт тайм» которых составляет 27 минут – быстрее окрасить поступившее шасси не получается.
Нанесенное покрытие сохнет при температуре 80 градусов Цельсия в специальных камерах сушки. По технологии MAN разные требования к внешнему виду предъявляются к разным частям шасси. Тем, что на виду (к примеру, противоподкатному брусу) наводится блеск и лоск, которым позавидуют кузова легковых автомобилей на выдаче клиенту.
После окраски, на протяжении трех станций, собирают пневматические и электрические «косы», где сборщики проявляют свои творческие способности, ведь существуют чертежи, но четкой трассировки их прокладки нет. Сотрудники руководствуются стандартами по длине, изгибам, расстоянию между хомутами и т. д.
Свои TGS в различных вариациях MAN оснащает двигателями стандарта Eвро-5 с применением AdBlue. Установка более экологичных версий в планах завода пока не значится. Дизельные двигатели «женят» с коробками ZF челнинского производства. Но в случае заказа автоматической трансмиссии ее привезут из Германии. Из Австрии в практически собранном виде на завод поступают кабины – на них лишь устанавливают аэропакеты, бачки омывателей и другую мелочевку. В финале сборки человек с компьютером, подключенным к машине, связывается с головным заводом в Германии, чтобы получить разрешение и программы для заливки в блоки управления электронных систем грузовика.
MAN в Санкт-Петербурге: смотрите и запоминайте
Приглашение посмотреть расположенный недалеко от Санкт-Петербурга сборочный завод компании MAN, как оказалось, следовало воспринимать буквально: внутри его производственных помещений смотреть действительно можно было на все, что угодно, а вот фотографировать оказалось запрещено категорически. Так что читателю в данном конкретном случае, как говорится, придется верить мне на слово.
Под завод, где сегодня собирают грузовики MAN, перестроили расположенный на территории промзоны «Шушары» бывший складской комплекс – вдоль всего его фасада и по сию пору тянется ряд из двух десятков «причалов» для подаваемых под погрузку фур. Сперва это здание в производственных целях арендовал General Motors, а затем, в 2011 году, после подписания с правительством Санкт-Петербурга соглашения о намерении разместить локальное производство, его сменило OOO «МАН Трак энд Бас Продакшн РУС». В 2012-м производственные мощности модернизировали и в конце того же года запустили в работу.
По сути завод – это один гигантский цех, где в пределах прямой видимости расположены и сборочная линия, и склад автокомпонентов, и площадка уже готовых к передаче заказчикам автомобилей. Среди последних на день моего визита оказались двухосные и трехосные седельные тягачи MAN TGS, меж стройных рядов которых обнаружились лишь два самосвала той же модели с кузовами Wielton – как объяснил наш сопровождающий, это последние экземпляры из уже отгруженной заказчику партии.
Судя по информации на вывешенных рядом со входом информационных стендах (Можно сфотографировать чтобы не переписывать? Ни в коем случае!), на сегодняшний день весь персонал завода насчитывает 76 человек, из которых 40 – рабочие. Общая площадь территории предприятия – порядка 33,5 тыс. кв. м, а непосредственно под производственные линии отведено около 19,5 тыс. кв. м.
Хотя привычного для более крупных автозаводов намертво встроенного в фундамент конвейера здесь нет (не те объемы производства), но суть технологии от этого не меняется: собираемые автомобили перемещают от поста к посту, но делается это с помощью нескольких движимых мускульной силой поставленных на небольшие колеса тележек, следующих вдоль одного-единственного проложенного по полу направляющего желоба, который издалека и не разглядишь. Сначала рабочие собирают раму, затем на нее ставят подвеску, оси, двигатель и КПП. В стороне от сборочной линии – окрасочная камера, где используются наиболее безопасные с точки зрения экологии красители на водной основе. Причем рамы питерской сборки красят только в черный цвет, тогда как в Европе – в семь различных цветов по выбору заказчика. Завершающий этап – монтаж кабины, а самая последняя операция – программирование бортового компьютера, который для этого по сети подключают к серверу, распложенному в Германии. На выходе – полностью готовый MAN TGS с российским WIN-номером. Производственные и складские помещения выглядят по-немецки опрятно, воздух в цеху свеж, температура комфортная, да и работа идет весело: на многих постах из принесенных, судя по всему, самими сборщиками динамиков льется музыка, причем у каждого – свой репертуар.
Интересно, что, в отличие от европейского завода, где изготавливают такие же грузовики, российские рабочие выполняют большее число операций, потому что у них больше времени на каждую единицу техники – темп производства не велик, всего четыре грузовика в смену, а смена одна. Понятно, что в подобном темпе за год не сделать и тысячи машин, хотя оборудование при односменной работе позволяет изготовить в три, а при двухсменной – в шесть раз больше. Зная подобный расклад не удивляешься, что производство остается чисто сборочным. Большинство комплектующих доставляют на завод в контейнерах: каждая партия, так называемый лот, обеспечивает изготовление 15 автомобилей. Плюс некоторые узлы, включая кабины в сборе, поступают отдельно. Участвуют ли в этих поставках отечественные предприятия? Фактически нет: судя по картинке на одном из уже упоминавшихся стендов, в питерских автомобилях MAN из российских компонентов – только аптечка, огнетушитель и технические жидкости. Плюс ко всему на той же картинке оказалась изображена коробка передач ZF – из тех, что в Набережных Челнах производит СП «ЦФ-КАМА». Я намеренно вынес упоминание о ней за рамки и без того скудного локализационного перечня, потому что складированные недалеко от сборочной линии коробки передач судя по закрепленным на них идентификационным табличкам оказались исключительно made in Germany. Впрочем не стоит отметать вариант, что челнинские ZF ставят на какие-то другие модификации MAN TGS.
Откровенно узкий перечень автокомпонентов местного производства для действующих в России заводов зарубежных производителей – вещь обычная, и никакие кризисы здесь ни при чем, как ни при чем состояние экономики в целом. Даже у сторожила нашего рынка, работающего в Миассе еще с середины 1990-х СП «Ивеко-АМТ», насыщенность российской компонентной базой выпускаемых автомобилей, точнее, их шасси, по сию пору остается на столь же невысоком уровне. И это за двадцать лет! Почему? Главным образом потому, что российские производители комплектующих за редчайшим исключением как были, так и остаются неспособными обеспечить требуемое качество при вменяемой цене. Тот же «Ивеко-АМТ» если что-то и локализует, то исключительно самостоятельно, будь то производство кабин, самосвальных кузовов или сортиментовозных платформ.
Впрочем, вернемся к питерскому заводу MAN. Исходя из личного впечатления, выстроенная на предприятии производственная схема для нынешней рыночной ситуации оказалась вполне жизнеспособна: несмотря ни на что грузовики здесь продолжают собирать, пусть и не в изначально планируемых объемах. Так, буквально перед моим приездом в тестовый 20-километровый марш-бросок, обязательный для всех выходящих из заводских ворот автомобилей, отправился тысячный питерский MAN, а тем временем рабочие уже комплектовали агрегатами машину с номером 1030. Так что дело идет, а мне со своей стороны остается пожелать заводу, чтобы на вторую тысячу автомобилей у него ушло времени как минимум не больше, чем на первую.
Константин Закурдаев
Интересное от редакции:
10.07.2015 в 15:35
22.05.2015 в 08:36
28.04.2015 в 08:29
14.04.2015 в 16:34
03.03.2015 в 07:30
15.01.2015 в 11:34
23.12.2014 в 14:22
06.12.2014 в 14:51

05.12.2014 в 16:15

28.11.2014 в 09:06
Читайте также:
20.12.2017 в 05:00
05.07.2018 в 05:30
17.11.2016 в 12:00
27.10.2014 в 17:54
26.04.2016 в 07:34
05.09.2017 в 08:00
14.09.2015 в 08:03
14.01.2016 в 07:23

20.03.2015 в 07:53
06.07.2016 в 12:30
«МАН»: страна-производитель и основные характеристики
Страна-производитель «МАН» (Maschinenfabrik Augsburg Nürnberg) – Германия. Концерн специализируется на выпуске грузовиков различного типа, автобусов, дизельных турбин и моторов. Фирма образована в 1958 году, штаб-квартира находится в Мюнхене. Свой 50-летний юбилей компания отметила в 2008-м, штат сотрудников насчитывает свыше 50 тысяч человек, годовой объем от продаж в 120 странах составляет порядка 15 миллиардов евро в год. Рассмотрим особенности создания фирмы, а также краткое описание самых популярных машин этой марки.
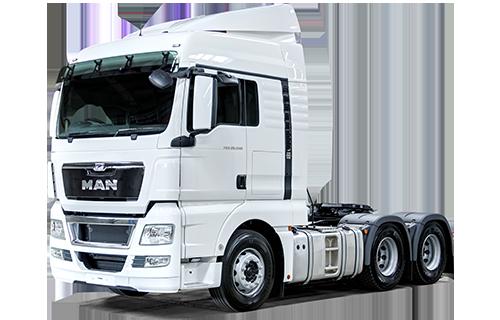
Исторические факты
Продолжая изучать страну-производителя «МАН», следует отметить, что исторически происхождение предприятия началось еще в 1758 году. В то время, в Оберхаузене начал свою работу металлургический комбинат «Санкт-Антоний». В 1808 году завод объединился еще с двумя компаниями, в результате чего был основан концерн Jacobi Iron And Steel Works Union And Trading Company (металлургическое производство от Якоб Айрон, Стил Воркс и «Трейдинг компани»).
Первое предприятие в Южной Германии, известное как «МАН», создал в 1840 году инженер Людвиг Сандер. В свое время наименование менялось на Maschinenfabrik, а позже – на MAN-Werk Gustavsburg. В 1908-м фирма получила свое нынешнее название, однако приоритетным направлением была добыча руды и производство чугуна. Хотя и машиностроительное направление не было оставлено без внимания.

Годы войны
Мало, кто не знает страну-производителя «МАН», поскольку эти грузовики распространены по всему миру. Стоит отметить, что в военный период экономическое положение корпорации существенно ухудшилось. Во многом на это повлияла репатриации после Первой мировой, оккупация Рурского региона, а также всеобщий финансовый кризис.
Всего за пару лет число сотрудников сократилось вдвое. Наблюдался развал гражданской промышленности, а военная сфера развивалась стремительно в рамках национал-социалистической идеи. На «МАН» производили дизельные моторы для танков и субмарин, цилиндры для снарядов и пистолетные детали. После окончания ВОВ союзники разделили предприятие по частям. Основным направлением стало изготовление коммерческих автомобилей и печатных машинок.
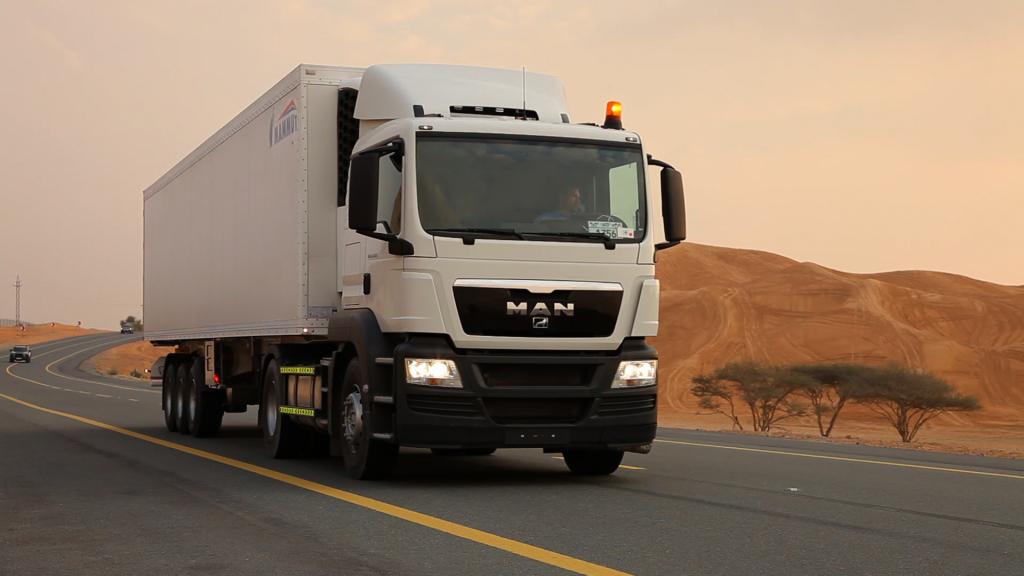
Очередной кризис
В 1982-83 годах страна-производитель «МАН» испытала очередной кризис, связанный с плохой финансовой ситуацией и нефтяным мировым коллапсом. Само предприятие ожидал глубокий корпоративный упадок. Преимущественно проблема отразилась на снижении продаж коммерческих транспортных средств. Дополнительным фактором спада производства стала устаревшая структура фирмы со значительным перекрестным субсидированием между филиалами. Обновление компании произошло в 1986 году, головной офис перенесли в Мюнхен, официальное наименование корпорации стало MAN AG.
Двухтысячные
В стране-производителе автомобиля «МАН» многое изменилось в 2006-м году (касательно указанного предприятия). Руководство концерна заключило договор с компанией из Индии Force Motors. Соглашение предполагало создание совместного комбината в равных долях для выпуска грузовых машин и автобусов, эксплуатируемых на внутреннем и внешнем рынке. Производственные мощности открыли в Питампуре, Мадъях-Прадеши. Первый грузовик индийского происхождения сошел с конвейера в 2007-м. Через четыре года немецкий концерн выкупил часть своего восточного партнера, после чего в Индии стало функционировать дочернее представительство.
Осенью 2006-го была предпринята попытка поглощения шведской «Скании», которую поддержала Европейская комиссия. Однако уже через пару месяцев предложение было отозвано в связи с отказом влиятельных акционеров. Свой 250-летний юбилей компания «МАН» отметила с размахом (2008 год). В программе представлены выставки в различных музеях, а также тур старинных моделей под лозунгом «МАН снова в дороге».
В 2009-м фирма перерегистрировалась под европейским брендом MAN SE. Летом этого же года филиалы MAN Turbo и MAN Diesel объединили в один проект под названием Power Engineering. Кроме того, корпорация подписала стратегический договор с китайскими партнерами, выпускающими грузовой автомобиль марки Sinotruk. В этот период часть мелких дочерних подразделений была распродана.
В стране-производителе грузовиков «МАН» не обошлось без скандалов. В 2009-м прокуроры Мюнхена разоблачили коррупционную схему, которая практиковалась руководством фирмы в плане подкупа деловых партнеров и членов правительств в нескольких десятках стран. Чтобы получить контракт на период с 2001 по 2007 год по выпуску автобусов и грузовиков, часть «верхушки» компании во главе с Гендиректором Самуэльсоном вынуждена были уйти в отставку.
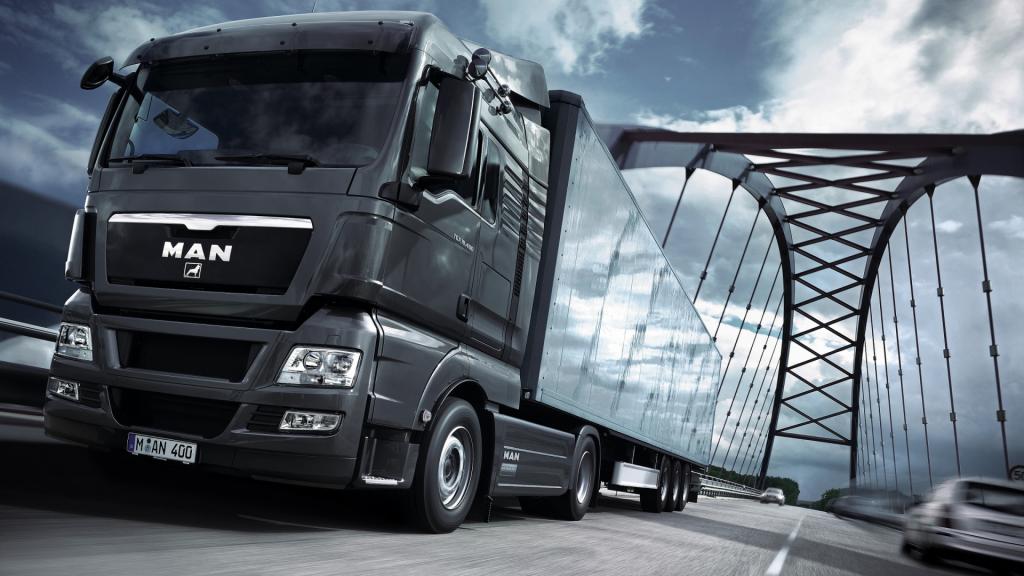
Ситуация с «Фольксвагеном»
История создания «МАН» продолжилась летом 2011 года. Тогда группа Volkswagen AG купила свыше 55 процентов акций голосов и половину капитала в MAN SE. Планировалось объединение со «Сканией», что позволило бы обновленной марке стать крупнейшим изготовителем европейских грузовиков. Подобная схема позволила бы сэкономить порядка полумиллиарда евро за счет объединения закупок расходных материалов и запчастей. Нормативная часть указанного соглашения завершилась в ноябре 2011-го.
Для справки:
- весной 2012 года компания «Фольксваген» увеличила акции голосов до 73 процентов;
- в июне того же года цифра выросла до 75 %;
- полученные результаты позволяют открыть соглашение о доминировании.
«МАН» — чья марка?
Страна-производитель рассматриваемого автомобиля – Германия. В современном модельном ряде представлено несколько разновидностей машин, краткие параметры которых рассмотрим далее. Начнем с серии ТГХ.
Указанные транспортные средства оптимально подходят для длительных перевозок, между собой отличаются габаритными размерами. Кабина машины характеризуется хорошей обзорностью, верхний люк открывается при помощи спойлера. Самое большое водительское место представлено в серии XLL. Внутри практически не слышно шума, а отделка и приборы выполнены на высшем уровне.
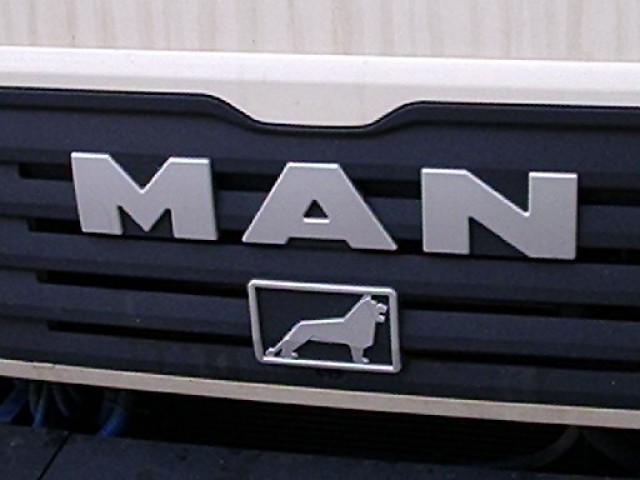
Модели ТГА и ТГС
Какая страна-производитель «МАН», рассмотрено выше. Далее вкратце изучим особенности грузового тягача линейки ТГА. Кабина и платформа этих машин ориентирована на перевозку строительных материалов и оборудования, при общей массе в 50 тонн. Автомобиль оснащается шестицилиндровым двигателем объемом 10,5 литров, мощностью до 440 «лошадей». Высота кабины составляет 2,2 метра при ширине в 0,79 м.
Грузовики линейки ТГС комплектуются одним из типов кабин:
Ширина первой «компактной» вариации составляет 0,75 м. Все указанные версии довольно высокие, оснащены необходимым оборудованием для оптимальной работы. Показатель мощности грузовика данной серии – 330-430 лошадиных сил при объеме в 10,5 литров. Надежность сборки и качественные параметры проверены временем.
Модификации ТГМ и ТГЛ
Автомобили «МАН ТГМ» весят 26 тонн, оснащаются восемью типами колесных баз (от 3,52 до 6,17 метров). Такие машины предназначены для транспортировки строительного сырья или мусора без выезда за пределы населенного пункта. Длина кузова варьируется от 3,9 до 8,1 метра. Автомобиль оборудуется дизельным мотором с шестью цилиндрами, мощностью 240, 280, 326 сил лошадиных. Стандарт соответствия экологическим стандартам «Евро-3».
Версия ТГЛ рассчитана на чрезмерные нагрузки, комплектуется специальным фильтром, который служит для очистки воздуха во время вентиляции или обогрева. Кабина машины оборудуется парой водительских кресел с подвеской. В качестве силового агрегата выступает «движок» с четырьмя цилиндрами, объемом шесть литров и мощностными показателями от 150 до 206 лошадиных сил.
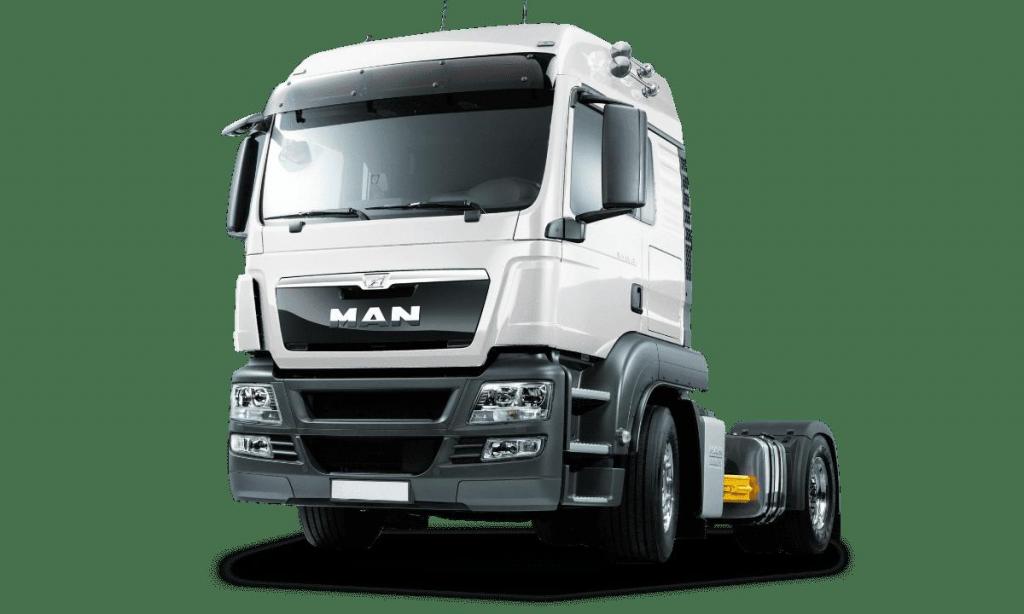
Интересная информация
Отвечая на вопрос, кто производит «МАН», страной-производителем упоминается Германия. Стоит отметить, что существенный вклад в развитие бренда внес Рудольф Дизель. Инженер в 1893 году получил патент на разработку четырехтактного мотора. Уже через четыре года был создан полноценный двигатель, работающий по принципу воспламенения от сжатия.
В 1925-м выпустили машины типа «МАН S1H6», имеющие грузовой объем до 5 тонн и «движок» с шестью цилиндрами. В 1955-м компания получила комбинат в Мюнхене, ранее разрабатывающий силовые агрегаты для различных серий «БМВ». С того периода выпуск грузовых машин начал активно разрастаться, а вместо V-образных моторов стали ставить шестицилиндровые версии. В 1978-м бренд «МАН» получил звание «Грузовик года», после чего сделали специальную производственную линию MAN Nutzfahrzeug AG. В этом направлении работал коллектив, численностью свыше 20 тысяч сотрудников. В 2007-м один из автомобилей «МАН» получил первое место на ралли Париж-Даккар.
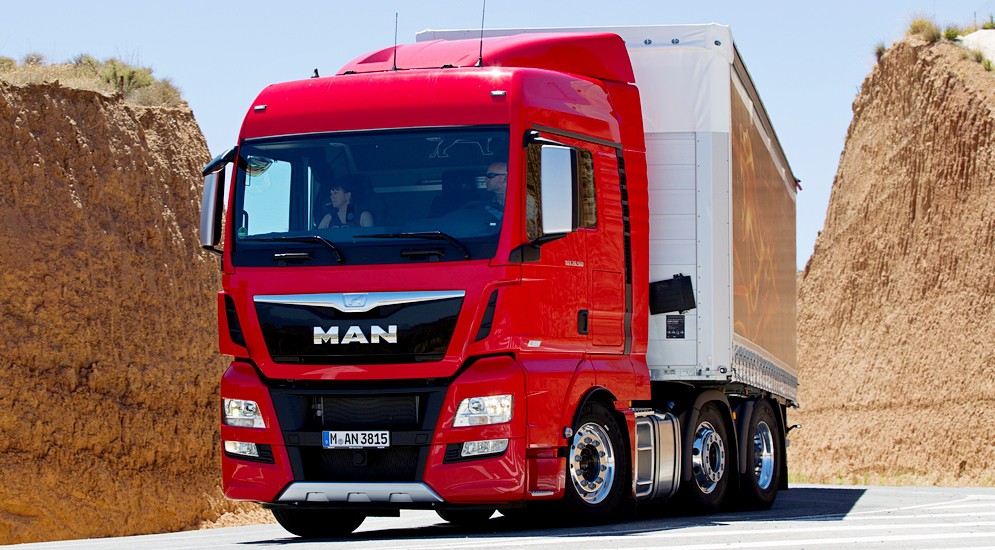
Итог
Грузовые машины рассматриваемой марки ориентированы на транспортировку грузов на длительные дистанции. Они активно используются для городских и межрегиональных перевозок. В линейке грузовиков разработаны версии, оборудованные для тех или иных целей. Все автомобили отличаются хорошим показателем грузоподъемности, надежностью и максимально комфортным оформлением рабочего места.
Как делают грузовики МАН: репортаж с завода
30 Мая 2019автор статьи и фотографий: Евгений Захаренко
В марте мы побывали на итоговой пресс-конференции МАН в Кракове и одним из самых интересных событий этой замечательной поездки было посещение автосборочного завода MAN в городе Неполомице. Об этом и расскажем.
Читайте также:
Интервью с Питером Андерсоном («МАН Трак энд Бас РУС»)
Пресс-конференция МАН 2019 (пролог)
МАН: итоги 2018 года. Это был один из самых лучших годов в истории МАН
Знаете, что больше половины MAN TGS и MAN TGX, которые совершают поездки по
дорогам России как раз и были там собраны? Это крупнейшая производственная площадка
MAN в Европе: автоматические конвейерные линии для сборки различных модификаций грузовиков, высокая экономичность процессов, система предупреждения ошибок на производстве и много чего интересного мы увидели сами.
Больше фотографий с завода в нашем фотоархиве «Пресс-конференция МАН -2019»
Мы уже писали о том, что в этом году завод получил престижное первое место в категории «Превосходное серийное производство». Руководитель завода Хайко Кайзер (Heiko Kayser), который нам и устроил экскурсию по заводу от лица почти 750 сотрудников завода принял награду
История завода МАН в Польше
История завода началась в 2005 году, как и принято, с проекта, а уже 4 октября 2007 года с конвейера сошел первый грузовик, в польском, красно-белом цвете, в котором мы также не преминули побывать см. фото.
TGA 19.400 – первый польский грузовик МАН собранный в Неполомице
Завод занимает 240 тыс. м2 огороженной территории и 1160 тыс общей площади.
Численность сотрудников – 752 человека из которых 643 человека технические специалисты, а 109 человек офисный персонал.
Общий вид завода МАН
Завод в Кракове проводит сборку всего модельного ряда крупнотоннажных грузовиков TG. Сейчас спектр продукции охватывает двух, трех и четерехосные грузовики серии TGS (спецтехника), TGX (внутренние и международные перевозки) и TGS WW (большегрузные перевозки за пределами Европы) различных конфигураций с полной массой более 16 тонн. Знаете, сколько грузовиков в день сходит с конвейера? Почти 100 штук! И это не предел. Работа организована в две смены, в каждой работают по 288 человек технического персонала. Первая смена выходит на работу в 14-05 , а вторая заступает на смену в 20-22.
Ближайшие планы завода выпускать 150 штук грузовиков в день. Прошли тестовые рабочие смены, когда выпускали 65 и даже 70 грузовиков за смену, а это 140 в сутки! При этом с конвейера сходят машины различных модификаций и назначений. Как такое возможно?
Завод в Неполомице отличает то, что сборка грузовиков построена по типу модульного производства перенятый у производителей легковых автомобилей, т.е грузовики собираются отдельными блоками: рама, кабина, моторный отсек, доставляются уже собранными с других заводов МАН, а уже на краковском заводе идет окончательная сборка машин, это позволило значительно повысить эргономику производства и снизить нагрузку на персонал.
Машины с завода в Неполомице работают по всей Европе, СНГ, Африке и АЗИИ, даже есть вариант для Англии, где как известно машины «праворукие», несколько таких машин мы увидели на конвейере, но почти четверть машин с краковского завода остаются в Польше.
На заводе отлажена логистика, каждый день идет разгрузка почти 100 грузовиков с запчастями. Запчасти приходят от почти 300 поставщиков, а общая сумма поставок в месяц превышает — 50 миллионов евро.
Для разгрузки траки заезжают прямо на сборочный пункт
Можно увидеть, как у каждого пункта сборки разгружаются поставщики оборудования, логистика построена таким образом, чтобы все комплектующие были максимально близко к сборочному цеху, например в пункте сборки двигателей, разгружаются поставщики запчастей для двигателей, если поставляют рамы, то их также разгружают в соответствующем месте, очень удобно и эффективно с точки зрения производственного процесса. Поставка и сборка оборудования находится практически в одном месте.
При этом ради оптимизации на заводе нет больших складов, набор комплектующих максимум на 2 дня работы. Поэтому если вдруг поставки прекратятся, завод полностью встанет через 1-2 дня, но произойдет ли это? Судя по немецкому принципу работы, только в случае природного форс-мажора.
Сотрудники завода, как правило, живут рядом, в ближайших городах и селах, зарплата порядка 700 — 1000 евро, небольшая, чем и обусловлен выбор размещения завода в Польше, в Германии сотрудники получают как минимум в 4 раза больше. На заводе есть тренажерный зал для сотрудников компании, где можно сбросить напряжение от монотонной работы на беговой дорожке или силовых тренажерах. Есть на заводе и собственный учебно-производственный центр по повышению квалификации работников.
Спортзал для сотрудников МАН
Также, МАН, независимо от должности, которую занимает сотрудник, спонсирует занятия спортом в любом профильном заведении Кракова, это касается и медицинского обслуживания. Ну, а чтобы, дополнительно мотивировать сотрудников не болеть, ввели премию для «неболеющих». Поэтому вести здоровый образ жизни выгодно.
Интересна также внутренняя система соревнований между производственными подразделениями МАН, буквально через две недели после нашего приезда наш экскурсовод поедет участвовать во внутренней премии, где будет презентовать систему контроля и мониторинга, которую они создали на заводе в Неполомице, если ситема окажется удачной, она будет внедрена на других заводах МАН, а сотрудники получат премию.
Экран системы мониторинга
Итак, как же собирают грузовики МАН?
Начнем с общего плана (см.фото). На заводе две сборочных линии на каждой из них есть несколько постов для сборки: 13 постов на первой линии и 40 постов на второй.
На фото Руководитель завода Хайко Кайзер (Heiko Kayser) показывает линии сборки завода
Процесс сборки начинается с рамы, она приходит на завод уже в сборе, остается только покрасить. Кстати, покраска возможна в любой цвет по желанию клиента.
Рама после покраски отправляется на конвейер
Дальше рама устанавливается на электрическую тележку конвейера и отправляется на сборку.
Рама на конвейере
Сама тележка, тоже интересное изобретение. Максимальный груз, который она может перевезти – 10 тонн, при скорости движения 30 метров в минуту. Каждая тележка имеет аккумуляторную батарею, которая заряжается индукционным способом
Автоматическая тележка на конвейере МАН
Чтобы сотрудники не заходили на траекторию движения тележек, она отмечена сигнальной разметкой.
Видео: самоходные тележки
Первый этап, это нанесение VIN-номера на раму, в коде которого зашифрованы сведения о производителе: код завода и характеристики будущего грузовика, такие как количество осей, год выпуска и др. VIN Краковского завода, как и немецких грузовиков, начинается с букв WMA, а последняя буква в номере — P (Польша).
Нанесение VIN-номера на раму будущего грузовика МАН
Здесь же прикладывается и протокол монтажа, который будет заполнен сотрудниками завода, по мере комплектации. Благодаря этому документу можно узнать важную информацию, какие компоненты, кем и когда были установлены. Каждый завершенный этап подписывается ответственным сотрудником. Это стандартная процедура для всех заводов МАН.
Движемся дальше и прокладываем электропроводку, пневматику, монтируем навесное оборудование.
Следующий этап монтаж рессор, стыковка осей, которых может быть от 2 до 4-х. Для этого есть два пункта сборки: для передних и задних. Как выглядит процесс? По конвейеру, на самоходных тележках подъезжает шасси, в этот момент сверху опускается рама. Два модуля стыкуются, а на следующем посте все фиксируется болтами. Как нас убедили, на сегодняшний день ни на одном заводе нет такого современного монтажа этих элементов.
Видео: процесс движения шасси по конвейеру
Монтируем передаточный вал, который получаем напрямую из Мюнхена. Дальше рама отправляется на монтаж двигателя, а мы заходим в центр обучения сотрудников.
Дальше рама отправляется на монтаж двигателя
Центр расположен на втором этаже, откуда можно сделать обзорные снимки всего производства.
Общий вид производства
Первая линия конвейера
Отдел логистики и запасных частей МАН
Отдел логистики и запасных частей расположен по центру, почти все эти запчасти будут установлены на машины в этот же день
Вторая линия конвейера
Учебный центр МАН
В учебном центре обучают новых сотрудников работать на всех этапах производства. Важно, чтобы работники могли в любой момент перейти на другой участок и помочь коллегам, если на каком-то из этапов сборки возникли сложности или не хватает работников. Здесь учат работать с инструментом, как правильно брать детали и монтировать. Все сотрудники должны выучить свои обязанности на том или ином участке производства.
Тренажеры
Интересен комплекс упражнений перед началом работы. Все сотрудники, занятые на производстве, как спортсмены перед игрой, должны «разогреться», провести разминку рук и туловища, это помогает избежать травм и улучшить концентрацию.
IT подразделение МАН
Продолжаем нашу экскурсию и проходим мимо участка шиномонтажа, сами колеса установим на грузовики немного позже, после монтажа силовых агрегатов.
Чистота на заводе впечатляет!
Переходим на участок, где подготавливают двигатель к сборке. На место сборки, двигатель поступает непосредственно от поставщиков из Нюрнберга и прямо из машины разгружается на производственную линию.
Сердце грузовика МАН
Подготовили? Установили коробку передач? Отправляем на самоходной тележке к месту сборки.
Двигатель МАН отправляется на сборку
Это уже вторая линия, на которой расположено 40 пунктов сборки, из которых 36 производственных и 4 буферных, также, на этой линии есть три пункта проверки качества.
Всего на заводе пять «ворот» проверки качества, на первой линии перед лакопокрасочным цехом и «финальная» перед «зеленой линией», но об этом позже.
Движение по конвейеру занимает в среднем 56 часов для тяжелого грузовика и около 36 часов для легкого. И вот здесь самый сложный момент, представляете как сложно уравновесить производственные процессы, когда по конвейеру одновременно двигаются грузовики разных моделей и модификаций?
Посмотрим, как устанавливают двигатель на раму?
Это можно сделать не торопясь, т.к. это единственное место, где будущий грузовик стоит на месте, на остальных участках, идет непрерывное движение грузовика от одного участка к другому.
С помощью кран-балки опускаем двигатель на раму
Протягиваем все соединения
И не удивительно, что здесь нужна остановка, монтаж двигателя дело серьезное, тут нет места для спешки. Все инструменты под рукой, в основном это пневматические гайковерты с автоматической настройкой крутящего момента. Причем система управления оборудованием проверяет какой модификации автомобиль стоит на участке и автоматически устанавливает параметры для закручивания, показывает количество необходимых соединений, а после монтажа, проводит проверку соединений, что дает 100% гарантию, того что все сделано правильно. Удивительно!
На монтаж, в зависимости от поста, уходит от 6 до 20 минут рабочего времени и в ближайшее время, это время будет уменьшено еще на три минуты. Во время нашего посещения завода здесь как раз работали специалисты по оптимизации рабочего процесса.
Пришло время установить радиатор…
Устанавливаем радиатор
Сотрудники весьма оригинальные личности, обратите внимание, на заводе можно работать в шортах, без головного убора, в общем, весьма комфортные условия.
Сотрудники завода МАН оригинальные личности
Мы спросили, не противоречит ли это технике безопасности, на что получили следующий ответ:
— В последнее время в Польше лето очень жаркое и мы разрешили сотрудникам возможность выбирать одежду, они могут носить как короткие брюки, так и длинные. Это их выбор. У нас есть внешняя служба сервиса одежды, которые нам ее доставляют, забирают, стирают, в том числе и обувь. Как правило, фирменная одежда сотрудников серого цвета, а мастера участка вы можете узнать по оранжевой футболке, ну, а если увидели желтую футболку, то это заместитель начальника цеха.
Вот такая цветовая градация.
Как нам рассказал сотрудник проводивший экскурсию, недавно на предприятие вызывали специалиста-медика, который изучил все этапы работы на каждом участке конвейера, провел анализ нагрузок и выдал список рекомендаций о том, как лучше держать инструменты и проводить монтаж оборудования, чтобы снизить уровень нагрузок и усталости. И это сработало! Хороший пример для других производителей.
Монтируем кабину?
Кабины, как мы говорили, поступают из Мюнхена, полностью готовые к монтажу. Опускаем кабину на раму, закрепляем, проводим электрику.
Монтаж кабины МАН
Также, на этом участке заливаем технологические жидкости: в пневматику для поднимания кабины, систему для управления шасси, проще говоря, гидропривод и заливаем 10% топлива в бак, уже пора.
Заливаем 10% топлива в бак
Сама емкость с баком находится за территорией завода, к посту подходит только трубопровод.
Электрика кабины и шасси, скоро все провода займут свое место
Кабина на месте, в баке бензин, пора ставить колеса!
Дальше идут одни из «ворот качеств» — QUALITY GATE, их можно узнать по синему цвету. Все проверяем согласно стандартам компании, но почти всю работу делает автоматика.
Ворота качества — QUALITY GATE
Спрашиваем, могут ли сотрудники слушать музыку или радио на рабочем месте.
– Да, это возможно, только оборудование (радиоприемник) обязательно должно быть проверено, на то, может ли оно находится на этом месте. Если все нормально, то такой прибор получает разрешительную этикетку, которая наносится на корпус, чтобы в будущем не было проблем со страховкой.
Также нам рассказали, что на предприятии очень следят за эргономикой производства и прислушиваются к мнению рабочих, так несколько лет назад, после общения с сотрудниками участка по монтажу электрооборудования, на заводе соорудили вот такие помосты, для удобства работы т.к. без них, было сложно дотянутся до некоторых узлов автомобиля.
Помост сделан по предложению сотрудников
Важно общаться с персоналом считают на заводе МАН, это помогает вводить интересные новшества, а сами работники чувствуют ответственность за рабочий процесс.
Каждый раз если на производстве случается какая-то нештатная ситуация угрожающая жизни работника, в течение 24 часов должен быть сделан анализ произошедшего: что произошло, почему, спросить у всех отделов на заводе, есть ли у них такая опасность и ввести меры предосторожности, чтобы такая ситуация больше не повторилась.
Монтаж электрооборудования теперь проходит легче
Ну что, пора заводить и тестировать? В этой зоне грузовики уже начинают самостоятельное движение, поэтому нам приходится быть очень осторожными. Итак, выходим на финишную прямую, последние два этапа. Первый для двух-трех осевых машин, второй для четырехосных.
Дополнительная проверка шасси осуществляется из смотровой ямы, проходит корректировка покраски, проверяется соединение кабины и рамы, и здесь же собирается техническая информация для калибровки тахографа.
Стенд для тестирования ходовой части грузовиков МАН, на такой ленте можно разогнать автомобиль до 140 км/ч.
На специальных стендах идет разгон машины. Дальше проверяем давление в системах, сход-развал, тормозную систему и АБС, токсичность выхлопов, дымность и т.д.
Вся проверка проходит согласно стандартам Фольксвагена, не забываем, что это главный акционер МАН. Это стандартная проверка для всех заводов МАН, Скания, Фиат, Фольсваген и Шкода. Это абсолютно независимая проверка приглашенных аудиторов, на которую никто не может оказать влияния или как у нас принято «договорится». Это самостоятельная юридическая единица. Дополнительно, есть практика перекрестных проверок, например, когда специалисты из Скании, расположенных в Германии или Австрии, проводят проверку здесь, а сотрудники завода МАН в Неполомице проверяют там.
— Мы должны быть уверены, что у нас одинаковые стандарты выпуска машин, ведь система проверки и оценки у всех одинаковая. Поэтому особого смысла выбора грузовика МАН немецкой, польской или российской сборки смысла нет,- убеждает нас гид.
Финальная проверка грузовиков МАН
При этом завод МАН в Неполомице может похвастаться опытом своих специалистов, которые уже несколько лет обучают сотрудников других заводов, регулярно проводят мастер-классы, даже летают в Бразилию, где также проводят обучение на одном из заводов МАН.
Итак, финальная проверка!
Проверяем все системы и подписываем тот самый «протокол монтажа», который составили в самом начале конвейера, когда вместо грузовика была только рама даже без vin-номера. Пока автомобиль двигался по конвейеру каждый работник вносил в него свою подпись по окончанию своего этапа работ. Сотрудники несут полную юридическую ответственность за качество своей работы. Даже если через 10 лет будет обнаружен дефект, будет точно известно, кто монтировал данный агрегат и кто несет ответственность. Кстати, все инструменты на заводе тоже проходят еженедельную проверку.
Благодаря многоступенчатой системе проверок качества сборки, 70% автомобилей проходят финальную проверку с первого раза, остальные требуют незначительных доработок. Правило МАН — в день не более 10 ошибок на 100 машин! Каждая ошибка анализируется и сводится к минимуму при последующих сборках.
Финальный протокол подписан, статус автомобиля меняем с «В процессе сборки» на «Собран» и перед тем как покинуть ворота, и пересечь символическую финальную «зеленую линию» конвейера, о которой мы говорили ранее, взвешиваем нашего «грудничка».
Финиш!
Символическая зеленая линия в конце конвейера означает, что автомобиль который пересекает эту линию полностью готов к работе и может быть отдан клиенту.
К работе готов!
Автомобиль отправляется на паркинг, а ключи и документация в отдел продаж. Благодаря нашей системе мониторинга, рассказывает нам экскурсовод, — мы точно знаем, где находится автомобиль: в процессе производства, в ожидании работ или готов к выдаче и знаем его точное место на паркинге.
Клиенты могут забрать автомобиль с завода самостоятельно или заказать услугу доставки у специализированных фирм. В момент передачи машины клиенту, еще одна проверка, еще один контроль… Проверим лакокрасочное покрытие и элементы защиты для транспортировки. Убеждаемся, что автомобиль передан клиенту в наилучшем виде и рабочем состоянии.
Место, где готовые грузовики МАН ждут своих клиентов
Завод МАН в Неполомице , как живой организм, постоянно эволюционирует и совершенствуется. Никакой пустой суеты, которой славятся некоторые китайские заводы, все спокойно, эффективно и по времени. Потрясающий завод!
Вот так и делают грузовики МАН! Всегда в первоклассном качестве, исключая малейшие варианты поломки.
Грузовики МАН они ведь не только для работы, но и для удовольствия!
Редакция журнала «Bus-club.ru» выражает благодарность компании «МАН Трак энд Бас РУС» за приглашение на пресс-конференцию, экскурсию по заводу и прекрасную организацию мероприятия.
Больше фотографий с завода в нашем фотоархиве «Пресс-конференция МАН -2019″
Источник: Bus-club.ru
Тема: Выставки и мероприятия