МарКон — Завод тормозных колодок
09.06.2017Политика производственного импортозамещения продолжается который год, однако основные успехи пока достигаются лишь на пищевом рынке. А вот производственная сфера развивается медленно, компонентная — еще и неохотно. Представители западных компаний, хотя и постепенно внедряются в производство, регулярно жалуются на отсутствие то условий, то нужного отечественного сырья. Могло бы показаться, что так у нас везде, однако компания «МарКон», например, с 1991 года занимается производством тормозных колодок в России. О том, почему отечественному производителю ничего не мешает, рассказал генеральный директор ООО «Завод Маркон» Сергей Чумаков (на фото вверху).

— В 1989 году ко мне подошел товарищ, показал колодку с наклепанным куском резины от старой транспортерной ленты и спросил: «Как ты думаешь, будет тормозить? Вот, купил на свой мерседес…» С этого все и началось. Отечественным производителям дисковых тормозных колодок в «свободные 90-е» нечего было предложить владельцам подержанных иномарок. И эта ниша запчастей на рынке с каждым годом только увеличивалась. Я рассудил так: колодка — конструкция примитивная, и независимо от того, для жигулей или для мерседеса она сделана, материалы на нее идут в принципе одни и те же. И рискнул начать производство тормозных колодок практически с нуля. На тот момент у меня уже был опыт инженера, производственника, управленца. А еще было давнее желание создать свой бизнес.
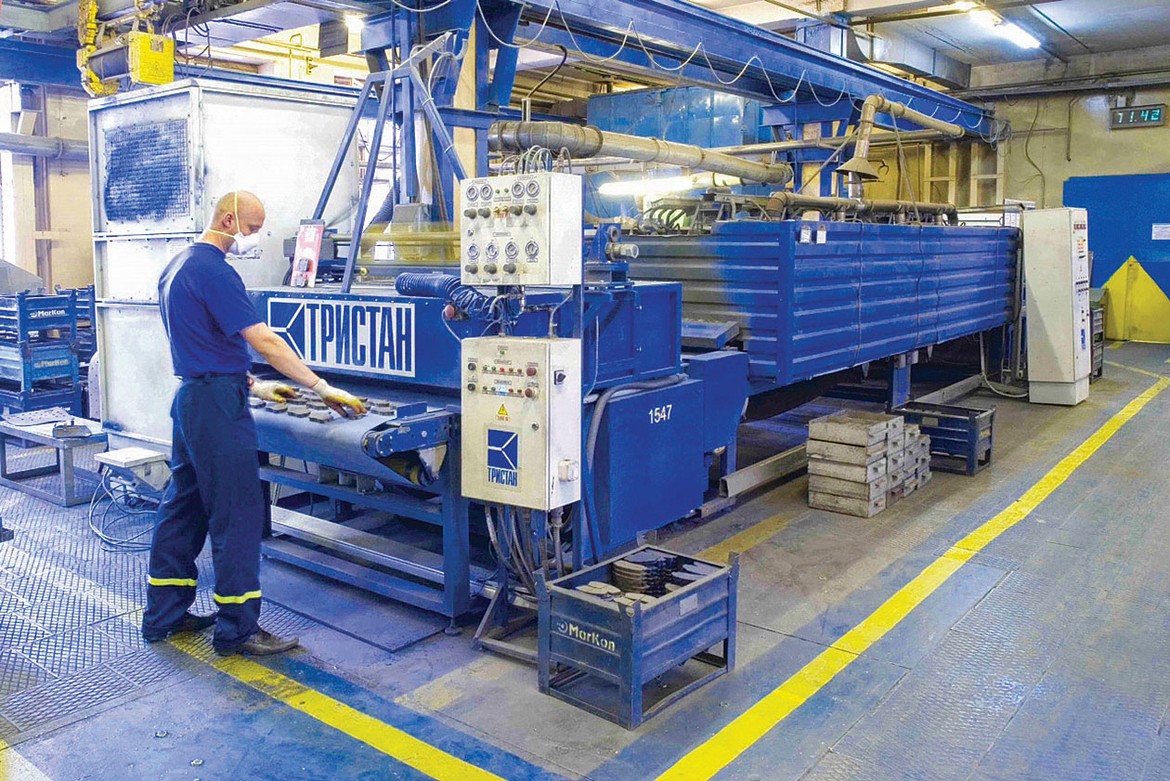
Покрасочная линия
— Вы сразу отдали приоритет иномаркам или работа с отечественными машинами тоже ведется?
— На момент вступления в рынок в стране было пять заводов, которые умели выпускать всего шесть видов дисковых колодок, зато в больших количествах. Это было напрямую связано с неизменной конструкцией тормозных узлов на российских автомобилях. Ни одно предприятие не было в состоянии оперативно отреагировать на потребность рынка и начать выпускать огромный ассортимент иномарочных колодок малыми партиями. На это и была сделана ставка. «МарКон» в первые три года наладил выпуск колодок на самые популярные тогда иномарки: Toyota Corolla, Volkswagen Passat, Mercedes W124, Audi 80, Opel Astra и другие. За первые 10 лет мы увеличили ассортимент до 110 наименований, а за 25 лет освоили уже более 400 типов колодок. Колодки на отечественные авто мы начали выпускать гораздо позже, когда задались целью поставлять продукцию на автосборочные конвейеры.
— Вы работаете только для вторичного сегмента или есть договора с кем-то из производителей в России?
— Изначально мы делали колодки для вторичного рынка. Но перед нами всегда стояла цель: выпускать продукцию в качестве ОЕ — Original equipment. Наши колодки успешно прошли ходовые и стендовые испытания на всех автосборочных конвейерах, и с 2001 по 2013 год мы были поставщиками конвейеров АвтоВАЗа, УАЗа, ЗИЛа, «ИжАвто» и «Русской механики». В настоящее время являемся поставщиками таких производителей, как АМО ЗИЛ, «Русская механика» и «Коммерческие автомобили — Группа ГАЗ».
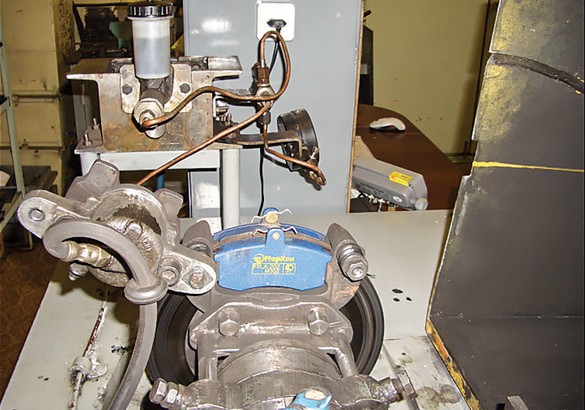
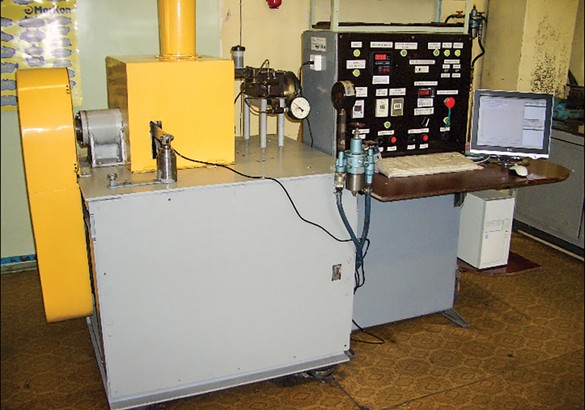
Безынерционные испытательные стенды БИНС-1 (слева) и БИНС-2
— Насколько сложно было работать на начальном этапе? Какие трудности были с отладкой производства, со сбытом, с конкурентами, с браком?
— Начальный этап был безумно сложным. Предприятие строилось и развивалось практически на энтузиазме и профессионализме его первых сотрудников. Была только идея, к которой нужно было приложить и производственные площади, и оборудование, и персонал, и рынок сбыта. Но главное — деньги. Чтобы открыть счет в банке, мне пришлось заложить в ломбарде некоторые личные вещи. Кредиты брали у частных лиц под 180%. Оборудование арендовали на действующих заводах Ярославля, сборка и упаковка производилась в гараже. Брака не было.
Готовые колодки я по выходным сам отвозил в Москву, развозил там по рынкам и ларькам, собирал отзывы, изучал спрос, попутно сам же и испытывал их на трассе, проделывая 25 торможений каждые 45 секунд со скорости 100 км/ч. За качество своей продукции буквально отвечал головой. Конкурентами «МарКона» на рынке в то время были ведущие мировые производители с многолетней безупречной репутацией: Lucas, Ferodo и ATE. Но у нас были свои преимущества: наличие на складе, скорость доставки и, конечно, цена.
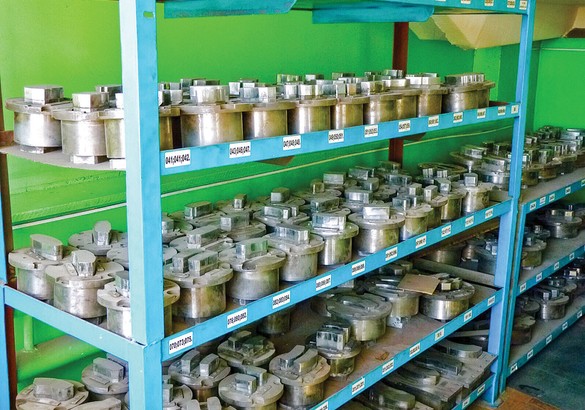
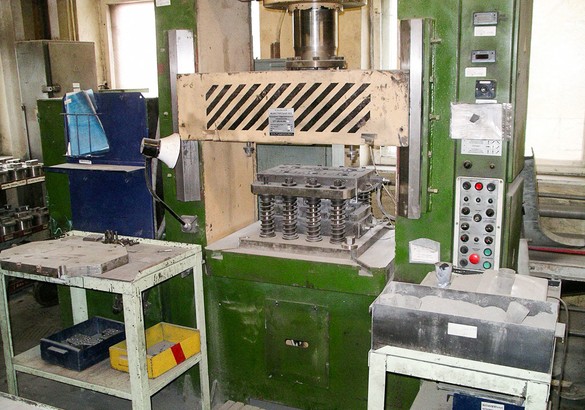
Прессформы и пресс
— Производственное оборудование и сырье — это все импортное или есть что-то отечественное? Какова приблизительная доля локализации вашей продукции?
— В начале 90-х свой первый цех на арендованной площади мы оснащали, как могли: смесь делали в бетономешалке, для вулканизации купили хлебопекарную печь. Прессы для формования искали по всей стране: из трех списанных собирали один действующий. Сырье закупалось только отечественное.
Сейчас ситуация другая: смесители — немецкие, печи — итальянские, станки — канадские. Но прессы и еще довольно много различного оборудования разработано и изготовлено для нас под заказ на предприятиях России. Оснастка — вообще вся отечественная. Из сырья за границей приходится закупать сурьму и арамидное волокно. Долю локализации импорта мы оцениваем в 30%.
— Какие годы были для вас самыми успешными и с чем вы это связываете?
— Самыми интересными в плане реализации идей, инженерных знаний, накопления опыта, налаживания торговой сети, конечно, были первые годы становления производства. В начале 2000-х автомобильный рынок показывал рост 10% в год. Мы же тогда росли на 25-30% ежегодно! Самым удивительным годом стал кризисный 2008-й. Наши дилеры, спасая свои деньги, выкупили у нас все складские запасы. А мы благодаря этому за год погасили пятилетний кредит на приобретение основного производственного корпуса.
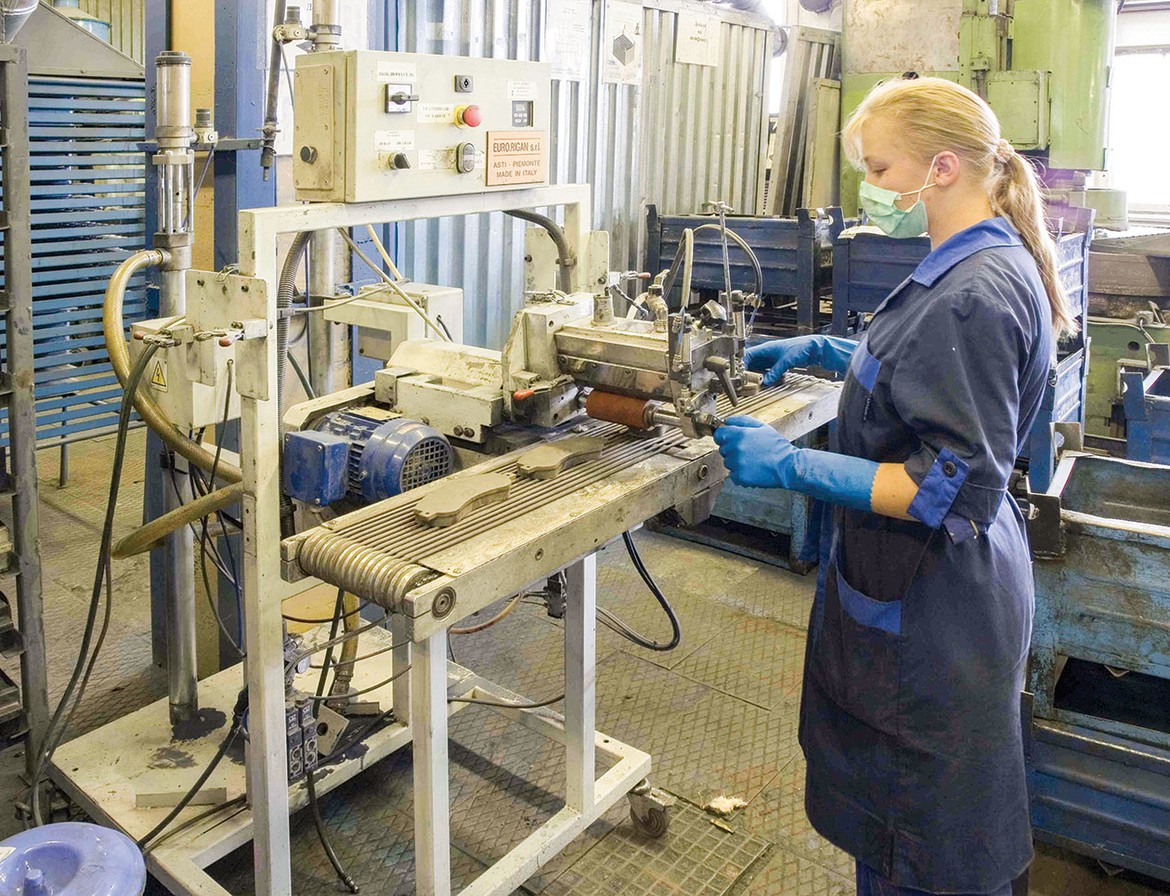
— Сейчас идет третий год кризиса. Насколько сильно он сказался на вашей деятельности? Какие меры вы приняли, чтобы минимизировать его последствия?
— Наше предприятие вообще выросло не «благодаря», а «вопреки», поэтому для «МарКона» этот кризис не опаснее других. Изменение экономической ситуации в стране отразилось прежде всего на тех предприятиях, которые работали на заемные средства, — вот им действительно тяжело пришлось. А «МарКон» использует собственные средства и рассчитывает всегда только на свои силы и ресурсы, поэтому от каких-то внешних факторов особо не зависит.
— Есть ли в ваших планах выход на производство других товарных групп?
— Производство дисковых тормозных колодок весьма специфично: и по сырью, и по оснастке, и по оборудованию, и по испытаниям. Готовая продукция требует обязательной сертификации. Встроить в существующее производство какое-то другое изделие, даже, например, барабанные тормозные колодки, практически невозможно. Правильнее делать то, что умеешь делать хорошо, и стремиться это делать лучше других.
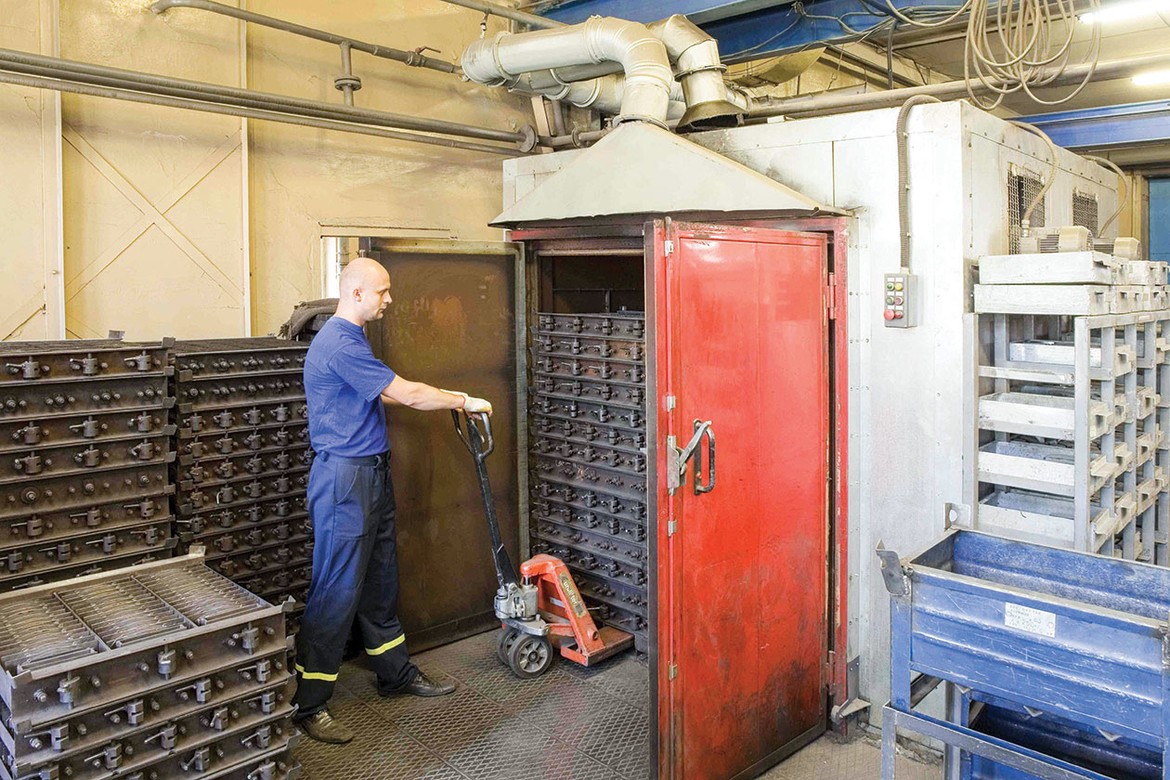
Печь для вулканизации
— Насколько сильна конкуренция сегодня? Чем вы переманиваете покупателей у именитых западных компаний?
— Конкуренция на рынке тормозных колодок и сильна, и велика. По-прежнему представлены самые авторитетные производители — Brembo, ATE, Ferodo, и есть еще более двух десятков известных европейских и азиатских фирм, предлагающих стабильное заводское качество. Все участники этого рынка, и мы в их числе, четко дифференцированы по ценовым нишам. При этом на рынке ежегодно появляются и исчезают все новые и новые имена из Китая с «акционной» политикой цен, и многие — без гарантии качества.
Для «МарКона», например, мелкие компании, которые завозят из Китая колодки сомнительного качества и продают их по бросовым ценам, не являются конкурентами. Но их деятельность мы расцениваем как нанесение вреда конечным потребителям, которые доверяют свою безопасность непрофессионалам, тратя свои кровные деньги на хлам, который и сертификацию-то редко проходит. Такие компании преследуют только одну цель — быстро «обернуть» деньги, не принимая во внимание самое главное: от того, что установит человек в свой автомобиль, напрямую зависит его жизнь. Поэтому беспокойство вызывает только будущее покупателей таких «колодок», а сами эти мелкие импортеры свое будущее себе уже выбрали.
Если говорить о здоровой конкуренции, то даже на таком плотном рынке можно получить преимущество — грамотно мониторя мировую автоиндустрию, первыми выпускать колодки на самые новые модели авто. Наш завод уже 25 лет поддерживает именно такой путь развития. К сожалению, у нас нет конкурентов среди российских производителей. Все существующие в России заводы выпускают свой небольшой узконаправленный ассортимент колодок.
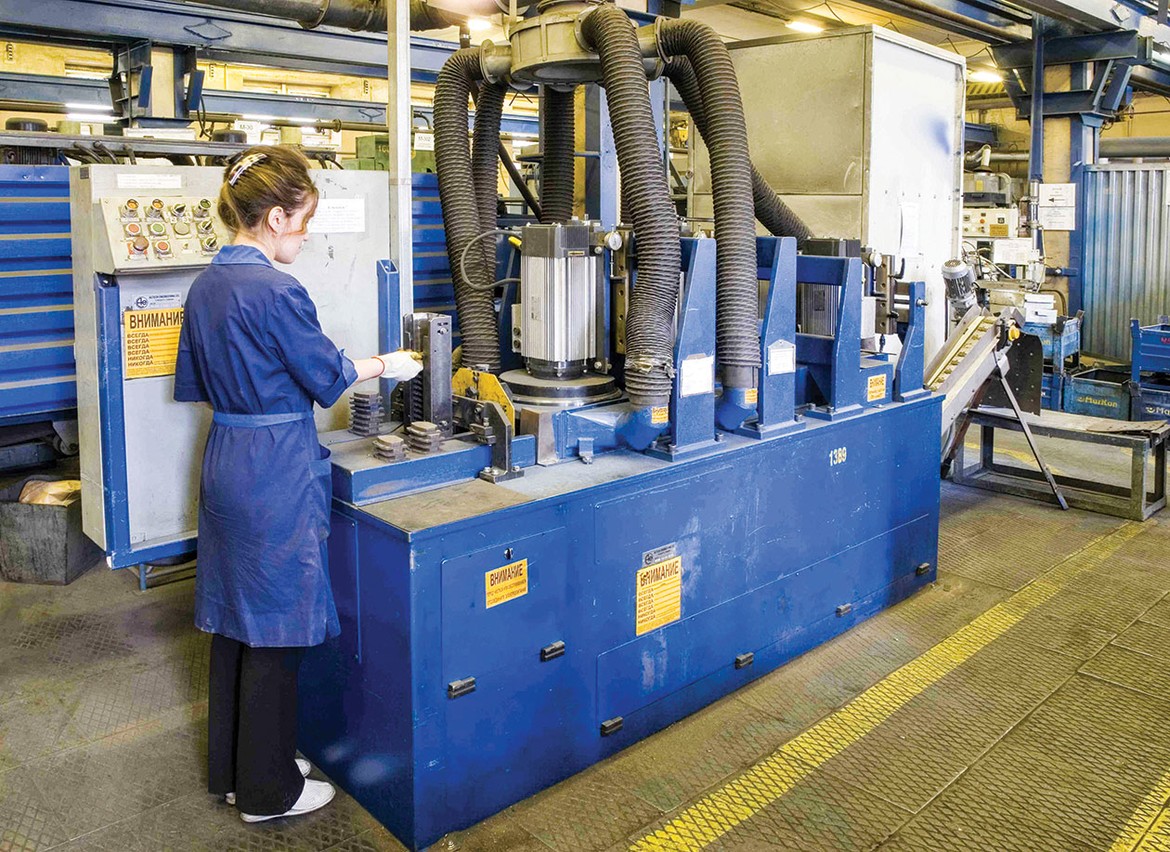
Технологический контроль
— Какие у вас планы на среднесрочную перспективу: расширение ассортимента, выход на другие рынки, работа с автопроизводителями, усиление маркетинга и пиара?
— Мировые автопроизводители ежегодно обновляют свой модельный ряд автомобилей, и мы за всеми этими обновлениями должны успевать, осваивая ежегодно от 15 до 40 новых типов колодок.
У нас сложилась надежная дилерская сеть в России и Казахстане. Сейчас мы выходим на другие рынки Таможенного союза и уже поставляем колодки в Армению, Грузию, Азербайджан.
Компания «МарКон» также планирует продолжать участвовать в тендерах автопроизводителей России, укреплять существующие партнерские связи, поддерживать свое доброе имя стабильно высоким качеством выпускаемых тормозных колодок.
Илья Огородников, журнал «ДВИЖОК», июнь 2017 #53
Как выглядит производство тормозных колодок

Многие не задумываются о том, какое значение в безопасности движения имеют тормозные колодки. Зачастую при ТО мы пытаемся сэкономить, и вместо рекомендованного производителем «оригинала» выбираем неоригинальные колодки известных марок – поставщиков для разных конвейеров, либо что-нибудь еще попроще.
Действительно, зачем переплачивать, особенно, если вы ездите аккуратно? А если что-то случится, например, экстренное торможение, окончившееся в бампере впереди идущего авто, то винить вы, скорее всего, будете не колодки, а самого себя. Даже если причина, на самом деле, в плохих колодках.
Вместе с тем, даже покупка колодок с известным брендом на этикетке не гарантирует высоких и стабильных характеристик. Процент подделок на этом рынке очень высок, и купить «левак» можно на любой популярной интернет-площадке и в практически любом магазине автозапчастей.
Впрочем, о подделках мы поговорим в другой раз, а сегодня я предлагаю перенестись на производство и посмотреть, как в России делают тормозные колодки. Специально для этого я отправился в город Тверь, где в промзоне на окраине расположен небольшой «колодочный» завод.
О производстве тормозных колодок
История этого производства началась в 2011 году, когда один из европейских «автокомпонентных» брендов решил открыть в России завод по производству тормозных колодок для поставки на конвейеры автозаводов, выпускающих автомобили иностранных марок. Таким образом, производители могли бы увеличить процент локализации своих автомобилей в том числе за счет колодок.
Производство было спроектировано европейскими специалистами. Был осуществлен подбор оборудования, разработана оптимальная рецептура фрикционных смесей.

Продукция перемещается по технологической цепочке на тележках как в супермаркете. В условиях небольшого производства это оказалось очень удобно. Такое вот ноу-хау!
Кризис внес свои коррективы – долгожданных заказов от автозаводов не последовало, и вскоре доля иностранцев в бизнесе была выкуплена российскими партнерами. В 2014 году началась история торговой марки Kotl, работающей на вторичный рынок. Сегодня мощность производства составляет 500 000 комплектов колодок в год, на заводе работает 58 сотрудников. Номенклатура составляет 225 наименований колодок, преимущественно, для иномарок.
Теперь пройдемся по технологической цепочке.
Каркас колодки
Тормозная колодка состоит из металлического каркаса и приформованной к ней фрикционной части. Соответственно, первый этап – это изготовление каркаса.

Процесс вырубки и механической обработки каркасов
Большую часть из используемых каркасов делают тут же, на заводе. При помощью вырубных штампов, механических и гидравлических прессов из листового металлопроката производства НЛМК формируется сам каркас, а также соответствующие элементы к нему — пазы для крепления аксессуаров, отверстия для электрических датчиков и так далее.

От листа металла — до заготовки каркаса
Часть каркасов закупается на стороне – в основном, это каркасы для отечественных автомобилей, которые широко распространены, что позволяет сэкономить на штампах, которые, к слову, на заводе изготавливают самостоятельно, используя в том числе электроэрозионные и фрезерные станки с ЧПУ.

Изготовление оснастки и пресс-формы
Часть «сторонних» каркасов выполнена методом лазерной резки.
Фрикционная смесь
Основная задача для производителя колодок для массовых автомобилей – это сохранение стабильности коэффициента трения, независимо от степени нагрева колодок.
Оптимальным показателем КТ является диапазон от 0.35 до 0.45. Многие производители, в том числе, KOTL, маркируют свои колодки по системе SAE двухбуквенным индексом. Например, FF означает что указанный выше диапазон коэффициента трения сохраняется и при холодной колодке, и на средней нагретости, и на горячей. Некоторые компании проводят испытания самостоятельно, в данном случае, испытания по температурным диапазонам проводятся в НАМИ в рамках сертификации продукции.
Применяемые фрикционные смеси относятся к классу низкометаллических. Состав смеси, соотношение компонентов, и, самое главное, режим прессования – все это напрямую влияет на характеристики, поэтому именно здесь и скрыта важная часть ноу-хау компании.
Фрикционная смесь – это микс из модификаторов трения, структуро-образующих веществ и наполнителей. Когда-то в качестве матрице-образующего материала широко применялся асбест, обладающий очень хорошими характеристиками стабильности и теплоотвода, но позже он был признан канцерогеном, и его использование во фрикционной промышленности было прекращено.
Вместо асбеста сегодня для создания матрицы используются различные синтетические волокна – арамидные, полиакрилатнитридные. Технологи KOTL для своих смесей выбрали более дорогой, но оптимальный с точки зрения свойств материал – оригинальный кевлар, производимый американской компанией Dupont. На вопрос, почему кевлар – не российского производства, руководители пожимают плечами, мол, весь российский кевлар идет на производство бронежилетов, и все, что доступно на рынке – измельченный «вторичный» кевлар, получаемый из содержимого списанных бронежилетов. По свойствам такой материал серьезно уступает «первичному» кевлару, зато дает право производителю гордо написать «кевлар» в рекламе.

Кевлар, металлошерсть, пыль трения и готовая фрикционная смесь
Кевлар организует структурную матрицу. В качестве наполнителей используются различные бариты и мелы. В состав смеси также входят модификаторы трения. Например, медный порошок предназначен для лучшего теплоотвода и стабилизации трения. Еще один важный компонент – так называемая пыль трения, представляющая собой измельчённую скорлупу орехов кешью. Этот продукт используется фрикционщиками испокон веков, производят пыль трения в Индии.
Также в состав смеси входит металлошерсть — рубленое металлическое волокно. В России данный продукт в хорошем качестве не производится, и его поставляют из Китая (где его делают из российской проволоки). Крупнейшее европейское производство металлошерсти расположено в Боснии.
Кроме кевлара, металлошерсти и пыли трения, все остальные компоненты фрикционной смеси (графит, сера, силикат циркония, барит и т.д.) производятся в России.

Формирование смеси происходит в специальном миксере
Компоненты смеси смешиваются в определенной пропорции (согласно технологической карте) в специальном миксере по особой программе. После этого смесь выстаивается, и попадает в цех прессования.
Прессование
Этот этап начинается с предпроизводственной подготовки ранее изготовленных каркасов. Они подвергаются машинной дробеструйной очистке – удаляются окалины, окислы и заусенцы.

Дробеструйная установка
Формируется поверхность для максимальной адгезивности.

Каркасы до и после дробеструйной обработки
Далее на каркас наносится термостабилизационный клей (российского производства). Подготовленные таким образом каркасы поступают на участок прессования, где смесь соединяется с каркасом.

Смесь засыпается в изготовленные в слесарном цеху специальные пресс-формы (уникальные для каждой модели колодок), после чего сверху устанавливается каркас и пресс начинает свою работу.

Горячее формование
Прессование выполняется «горячим» методом, для того чтобы уже на первом этапе сформировалась структура смеси, вышли первоначальные газы, обусловленные присутствием в составе фенольной смолы. В процессе происходит несколько «подпрессовок», несколько «прогазовок». При помощи пирометров контролируется температура. Также под контролем находится высота, чтобы не было недо- или перепрессовок. Управляемая компьютером программа прессования, соответствующая конкретной технологической карте – еще одно ноу-хау компании.
После прессования колодки попадают на участок термостабилизации.
Термостабилизация
Программа термостабилизации – это чередование режимов нагрева и остывания. Процесс происходит в специальной печи и занимает от 8 до 12 часов, в зависимости от типа колодки и ее назначения. Например, колодки для коммерческого транспорта «прожигаются» дольше, и при более высокой температуре. Печь работает в автоматическом режиме по технологической карте.

Печь для термостабилизации
Необходимая температура выдерживается при помощи термодатчиков, расположенных в четырех рабочих зонах. В случае выхода показателей за пределы нормы, печь автоматически отключается, отправляя соответствующий сигнал в управляющую систему. Все параметры и логи процессов сохраняются в облачной системе, к которой инженеры и руководители производства имеют удаленный доступ.
В процессе термостабилизации происходит окончательное спекание смол и формирование структуры колодки. После этого колодки будут практически готовы к использованию – для их приработки будет достаточно 20-30 обычных торможений.
Производственники особенно подчеркивают, что высокие характеристики достигаются без использования так называемого «скорчинга» — «ударного» нагрева контактной части колодки до 650-700 градусов Цельсия. С точки зрения тверских инженеров, этот «стрессовый» процесс не идет на пользу материалу колодок, в отличие от другой, также используемой на производстве, технологии – аналога разработки COTEC от TRW.
Специальное покрытие, нанесенное на рабочую поверхность, позволяет добиться максимального коэффициента трения с первого нажатия педали тормоза. Из-за высокой стоимости данное покрытие применяется только на «премиальных» колодках (отличить их легко по цветному покрытию рабочей поверхности колодки).

Колодки со специальным покрытием не требуют приработки и эффективны с первого нажатия на педаль.
Но не будем отходить от темы, ведь нас ждет следующий этап жизненного цикла тормозной колодки – механическая обработка.
Механическая обработка
На данном этапе происходит окончательное формирование размера колодки по ее габариту, рекомендованному производителем тормозной системы либо автомобиля, придание ей необходимого внешнего вида, формирование пропилов (для отвода «мусора») или скосов (для лучшей притирки и снижения шумовой нагрузки).


После этого колодки направляются на покраску.
Покраска
На данном этапе на колодки наносится антикоррозионное покрытие методом порошкового напыления полимерной краски в туннельной печи конвейерного типа.

Процесс практически полностью автоматизирован, благодаря чему достигается высокое качество покраски. Процесс прохождения конвейера занимает около 45 минут. После этого мы получаем практически готовый продукт – осталось установить аксессуары и нанести маркировку.

На каждом этапе осуществляется визуальный контроль качества.
Комплектация
На финальном этапе происходит маркировка колодок и установка аксессуаров – датчиков износа (механических или электрических), пружинки, противошумные пластины. Поставщиком аксессуаров выступает итальянская компания Daico – китайские комплектующие имеют нестабильное качество, а в России производятся лишь самые простые виды «навески».

Примечательно, что маркировка на колодке позволяет проследить весь ее путь по производству – не только конкретную технологическую карту, но и логи производимых процессов по данной партии.

Колодки закатываются в термовакуумную пленку, после чего упаковываются в коробки. Коробки отправляются на склад, а оттуда – к потребителям, но лишь после того, как образцы партии пройдут тестирование.
Тестирование
Образцы каждой партии колодок направляются в собственную технологическую лабораторию на тестирование по ряду показателей.

Проводятся тесты колодок на отрыв, сжимаемость, изменение толщины в зависимости от температуры, коэффициент трения при различной температуре. Лишь после успешного прохождения всех тестов партия колодок готова к отгрузке.
Источник
Как выглядит производство тормозных колодок
5 (100%) 2 голос[а]Производство тормозных колодок в России КЁТЛ
Компания Kötl является российским производителем колодок дискового тормоза для легкового и легкого коммерческого транспорта.
Компания ведет свою историю с 2011 г., когда группа европейских инвесторов, обладающая значительными активами в производствах автозапчастей в Европе, решила открыть кластер производств автокомпонентов в России и начала с завода по производству фрикционных колодок дискового тормоза.
Это решение было обусловлено тем, что к тому времени на территории Российской Федерации было уже открыто много зарубежных автомобильных производств, таких как Volkswagen, Ford, Toyota, GM, Nissan и др. Каждое из них имело программу локализации производства комплектующих вследствие правительственных требований и конечно было заинтересовано в появлении на территории РФ компании-поставщика авто компонентов мирового уровня.
В конце 2012 г. предприятие Kötl начало производство тормозных колодок в России. Были проработаны поставки (продукция прошла омологацию) на некоторые сборочные автомобильные конвейера внутри Российской Федерации и начаты отгрузки продукции некоторым европейским брэндам автозапчастей для продажи.
Однако в 2014 г. европейские инвесторы решили уйти из России в связи со сложной обстановкой в политической и экономической сферах. В результате работающий завод по производству фрикционных колодок дискового тормоза был приобретен российским инвестором отчасти и благодаря программе по импортозамещению Министерства Промышленности РФ.
При этом условия контракта гарантировали длительное сопровождение контроля качества и технологии европейскими технологами, а российская сторона обязалась сохранять технологический уровень производства и качество готовых изделий на прежнем уровне с целью продолжения осуществления долгосрочных контрактов, заключенных предыдущим собственником.
Таким образом продукция нашего предприятия по своим техническим характеристикам вполне сопоставима с европейской, так как сделана по европейским технологиям на оборудовании, удовлетворяющем строгого потребителя в лице автопроизводителей. Мы предлагаем высокое качество по разумной цене, так как работаем в России. Наша цена сопоставима по цене с азиатской продукцией, которая существенно проигрывает в таких потребительских свойствах как комфорт, безопасность и экономичность. Ни для кого не секрет, что при поставках в Россию за красивой упаковкой многих известных европейских и японских брендов прячется китайская продукция низкого качества! Мы предлагаем честный продукт высокого уровня по доступной цене.
Торговая марка Kötl — это надежная российская продукция с европейским качеством.
Экология
Мы стремимся не только выполнить требования законодательства, но и свести к минимуму воздействие на окружающую среду и здоровье людей, снижая количество отходов и выбросов, более ответственно используя природные ресурсы и сохраняя природные экосистемы. Компания Kötl считает важнейшей задачей руководствоваться основополагающими принципами в вопросах экологии:
- признание конституционного права человека на благоприятную окружающую среду;
- безусловное выполнение требований законодательства и международных договоров, стандартов и правил в области природопользования, охраны окружающей среды и экологической безопасности;
- сокращение образования отходов производства и экологически безопасное обращение с ними;
- приоритет принятия предупредительных мер над мерами по ликвидации экологических негативных воздействий;
- рациональное использование природных ресурсов на всех этапах производственной деятельности Компании.
Социальная ответственность
Основной целью социальной политики компании является производство необходимой обществу безопасной продукции в объемах и ассортименте соответствующему потребностям динамично меняющегося рынка и запросам партнеров.
Решение социальных проблем занятых в производстве наемных работников также является одним из главных аспектов деятельности компании.
- компания предоставляет рабочие места с конкурентоспособной оплатой труда;
- обеспечивает работникам безопасные условия труда, отвечающие современным требованиям;
- cоздает социально-бытовые условия на производстве с приоритетом безопасности работников и сохранения их здоровья;
- предоставляет полное содействие всестороннему профессиональному развитию сотрудников и повышению их квалификации;
- несет ответственность перед партнерами компании и ее инвесторами.
Компания организовывает свое производство максимально эффективным образом с применением ресурсосберегающих технологий и оптимальным распределением рабочей силы.
Охрана Труда
Одной из основных задач компании является обеспечение безопасных и здоровых условий труда на всех рабочих местах предприятия – при эксплуатации оборудования, осуществлении технологических процессов, а также использование применяемых в производстве инструментов, сырья и материалов в соответствии с действующим законодательством в области охраны труда.
Достигается это путем систематического проведения комплекса организационно-технических, санитарно-гигиенических и других мероприятий в соответствии с действующим законодательством. На предприятии организована система проведения производственного контроля за состоянием условий и охраны труда, приобретается и своевременно выдается сертифицированная специальная одежда, специальная обувь и другие средства индивидуальной защиты в соответствии с установленными нормами в области охраны труда.
Производство тормозных колодок в России
Производители тормозных колодок на рынке России предлагают достаточно большой выбор своих изделий разного уровня качества. Колодки Kötl производят только из высококачественных материалов, которые прошли специальную проверку и соответствуют европейским стандартам компании. Тормозные колодки Kötl это:
- высокое качество;
- стабильность работы тормозной системы;
- надежность;
- уверенность в работе автомобиля;
- долгий срок службы.
Руководство нашей компании продолжает работать над совершенствованием качества продукции, современное оборудование для производства тормозных колодок регулярно обновляется. Производство тормозных колодок в России отвечает высоким европейским стандартам. Сотрудники компании стремятся не только поддерживать текущее качество производимых тормозных колодок, но и постоянно работают над развитием своего бренда и выпускаемых изделий.
10 Лучших Тормозных Колодок – Рейтинг 2019 года
Дисковые тормоза появились в далеком 1902 году, однако не получили распространения в то время. Сегодня каждый водитель точно знает, что хорошие тормоза – главный секрет безопасной езды на машине. Лучшие тормозные колодки обеспечивают короткий тормозной путь, а также сохраняют целостность диска. Рейтинг лучших расскажет, как сделать верный выбор и на что обратить внимание при покупке тормозной системы.


Как выбрать тормозную колодку
При обзоре предложений автомагазинов были изучены технические характеристики продукции, отзывы пользователей, обзоры и мнения специалистов. При сравнении моделей и добавлении их в ТОП лучших учитывались следующие критерии:
- Качество и материал изготовления;
- Репутация бренда;
- Наличие датчика износа;
- Уровень абразивности;
- Бесшумность;
- Рабочая температура;
- Результаты тестов;
- Соотношение цены-качества;
- Доступность в автомагазинах;
- Популярность у покупателей.
У водителей легковых машин, коммерческого авто и владельцев мототехники общие требования к тормозным системам одинаковы. Выбор колодок зависит в первую очередь от их совместимости с дисками авто и манеры вождения. Так, для медленной езды подойдут бюджетные аналоги. Для активной лучше брать модели проверенных производителей.
Лучшие тормозные колодки для иномарок
Мировые бренды тормозных систем нацелены на автомобили иностранного производства. Мы изучили предложения рынка и выделили 7 лучших производителей, которые делают запчасти для немецких, японских, американских и других легковых и коммерческих автомобилей.
Ate
Лучшие тормозные колодки немецкого производства из представленных в рейтинге. Их производству более 100 лет, за это время тормозная система Ate зарекомендовала себя наилучшим образом.
Рецептура фрикционного материала постоянно дорабатывается. А добавление цветных металлов улучшает его характеристики и выносит продукцию производителя в премиальный класс. Каждое изделие досконально проверяется перед выпуском на рынок. Благодаря этому качество изготовления всегда на высоте: структура смеси плотная однородная, прокраска по бокам аккуратная, основание сделано добротно.
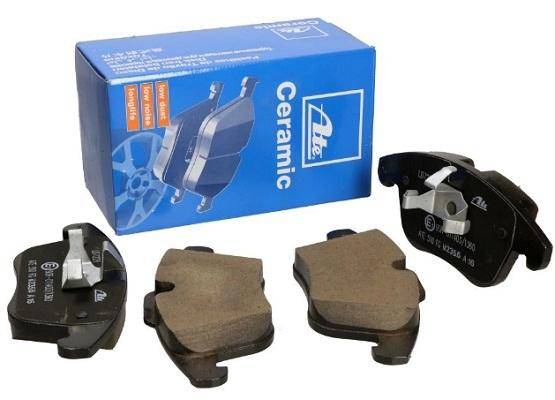
Достоинства:
- Стойкость к ржавчине;
- Долговечность;
- Отсутствие пыли;
- Нет шумов или скрипов;
- Качественная упаковка из плотного картона;
- Защита от подделок.
Недостатки:
- Цена выше, чем у конкурентов;
- Сложно найти в наличии.
Ate предлагает оригинальные и керамические модели. Оба варианта бережно относятся к дискам, продлевая их срок службы.
Nisshinbo
Nisshinbo возглавляют рейтинг тормозных колодок для иномарок японского производства. Вековая история бренда доказывает их качество и надежность. А уникальная конструкция с диагональным пазом обеспечивает равномерный контакт с диском для минимизации вибраций и шума.
Изделия отличаются оптимальной прочностью, гибкостью, стабильной работой. Они бережно относятся к дискам, предупреждая их преждевременное изнашивание.

Достоинства:
- Отсутствие свистов;
- Оптимальный уровень теплового расширения;
- Органический состав;
- Нет запаха;
- Большой выбор моделей.
Недостатки:
- Высокая цена для неоригинальных запчастей;
- Много подделок.
Nisshinbo нужно покупать только у проверенных продавцов, поскольку на рынке много подделок этого бренда.
Zimmermann
Самые надежные колодки. В ассортименте производителя более 1,000 позиций для разных марок и моделей автомобилей. Скрупулезный контроль в процессе изготовления и дальнейшее тестирование заявленных технических характеристик всех изделий проводится в лаборатории компании при производстве каждой новой партии.
Особое экологически чистое покрытие защищает пластину от коррозии и грязи. А технология спекания позволяет минимизировать время притирки. При нагревании четкость торможения только увеличивается.

Достоинства:
- Качественная упаковка;
- Нет асбеста в составе;
- Соответствие европейским стандартам качества;
- Комфортное торможение.
Недостатки:
- Высокая стоимость.
При покупке колодок производитель также рекомендует менять диски, так как одновременная замена тормозной системы и установка запчастей одного бренда увеличит их производительность, а также продлит срок эксплуатации.
Wagner
Лучшие тормозные колодки, пришедшие из Северной Америки. По ценовому сегменту Wagner охватывает все ниши – от самых бюджетных до премиального класса. Керамические цельные модели считаются одними из наиболее тихих. Благодаря плотному соприкосновению фрикционного материала и скобы увеличивается срок эксплуатации изделия и комфортное мягкое торможение при любых условиях езды.

Достоинства:
- Обеспечивают меньший тормозной путь;
- Не ест диски;
- Репутация производителя.
Недостатки:
В период обкатки водители замечают туговатость педали, но со временем она уходит, обеспечивая комфортное торможение.


Ferodo
Самые экологичные тормозные колодки из представленных в рейтинге. Модельный ряд Eco-Friction – результат 5-летних исследований технологов фирмы. Для эффективности тормозной системы в них заложено 25 компонентов с низким уровнем содержания тяжелых металлов, что минимизирует вредные выбросы в окружающую среду. Продукция Ferodo является оригинальными запчастями для конвейерных авто нескольких моделей Mercedes и Audi.
Для коммерческих автомобилей компания представляет модели Premier. Они имеют увеличенный срок эксплуатации. Линейка Target предназначена для разного стиля езды. Она идеально для машин с несколькими водителями. Маркировка Perfomance подходит автолюбителям, предпочитающим спортивную манеру езды. Они остаются максимально эффективными даже при долгом нажатии на педаль тормоза.

Достоинства:
- Подавление шума;
- Эффективность торможения на 17% выше, чем у аналогов;
- Продаются в большинстве магазинов;
- Недорогая цена;
- Защита от подделок;
- Чугунная несущая пластина.
Недостатки:
Ferodo – компания, предлагающая широкий ассортимент моделей. Несмотря на продуманную защиту от поддельных изделий, автолюбители жалуются, что на рынке их остается довольно много.
Trw Lucas
Хорошие тормозные колодки, по отзывам автолюбителей. Особое силикатное покрытие Cotec улучшает соприкосновение между диском и фрикционной смесью, уменьшая тормозной путь на 7 метров. Это особенно важно при экстренном торможении в период обкатки. Линейка керамических изделий Dtec отличается низким уровнем образования пыли. Это благотворно влияет на чистоту колес, а также на безопасность торможения.
Вся продукция проходит нагрев до 600-700 градусов. Эта технология уменьшает время притирки и увеличивает эффективность при большом нагреве. Формовка происходит под высоким давлением для оптимальной плотности состава и уменьшения его пористости. Порошковое покрытие на пластине предотвращает появление коррозии.
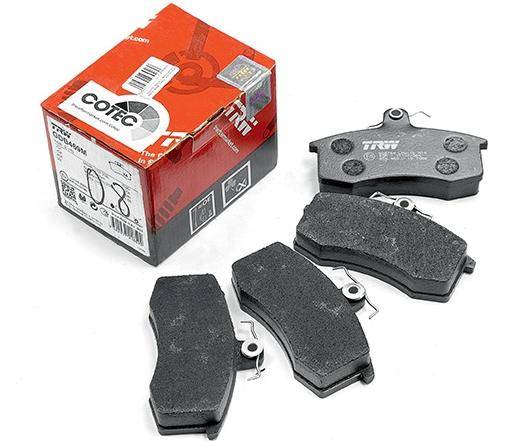
Достоинства:
- Модельный ряд для большинства автомобилей и мототехники;
- Продолжительный срок эксплуатации;
- Доступная цена;
- Репутация производителя.
Недостатки:
- Иногда скрипят.
Trw Lucas заботится об окружающей среде и не использует в производстве тяжелые металлы или токсичные материалы.
Ebc Brakes
Хорошие передние и задние тормозные колодки, произведенные на заводе компании в Британии. Под брендом Ebc Brakes выпускается 2 линейки моделей:
- Ultimax;
- Bluestuff Ndx.
Первые – это качественная замена оригинальных запчастей для ежедневной городской езды. Модельный ряд широк – от легковых машин до тяжелых грузовиков и полноприводных внедорожников.
Bluestuff Ndx – линейка для автоспорта или для водителей с агрессивным стилем вождения. Она эффективна даже на холодную зиму без предварительного прогрева тормозной системы.
Вся продукция производителя имеет особое крепление фрикционного материала к основе через прослойку, которая поглощает вибрацию, не дает ему сдвинуться или отделиться от металлической пластины в экстремальных условиях.
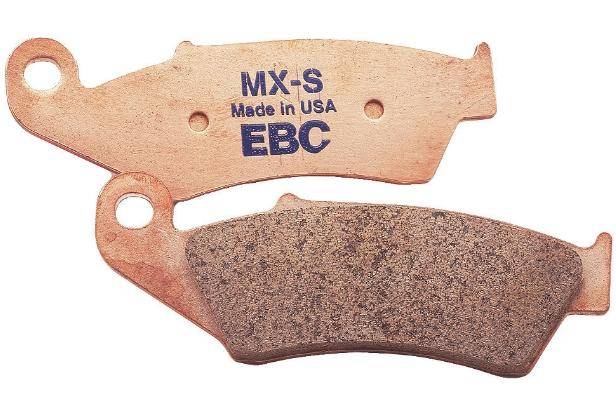
Достоинства:
- Оптимальный тепловой режим, подобранный под стиль езды;
- Долгий износ;
- Соответствие Европейским требованиям безопасности;
- Не пылят.
Недостатки:
- Много подделок на рынке.
Ebc Brakes – вариант для тех, кто хочет отказаться от оригинальных тормозных систем. Это достойная замена при более низкой стоимости.


Лучшие тормозные колодки для отечественных авто
Количество производителей, изготавливающих колодки для российских машин, гораздо меньше, но и о них важно упомянуть. Российский завод существенно увеличил свою долю в автопарке, что имеет важное значение и для рынка автомобильных деталей. Мы провели анализ отечественной продукции и выявили 3-х лучших.
Sts
Одни из лучших российских тормозных колодок. Ассортимент изделий высок. Здесь есть варианты практически на любую модель российского автопрома, а также на совместно разработанные машины Киа и Рено. Фрикционные смеси состоят из 15 компонентов, включают добавки для стабилизации авто и снижения уровня шума при работе, надежно защищены от отрыва от пластины.
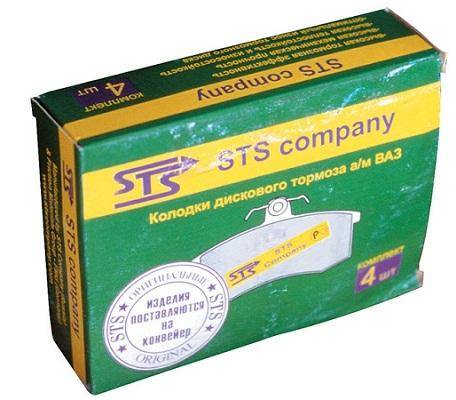
Достоинства:
- Высокий ресурс;
- Соответствуют европейским стандартам;
- Низкая цена.
Недостатки:
- При многократном торможении коэффициент трения снижается.
Качество продукции Sts не хуже импортных изделий. Однако ее цена гораздо ниже.
Вати
Хорошие экологичные колодки для отечественных автомобилей. Вати предлагает продукцию, подходящую только для автомобилей ВАЗ. Из их состава исключен асбест. Фрикционные свойства показывают удовлетворительные результаты в холодном режиме, а также при высоких температурах после прогрева.
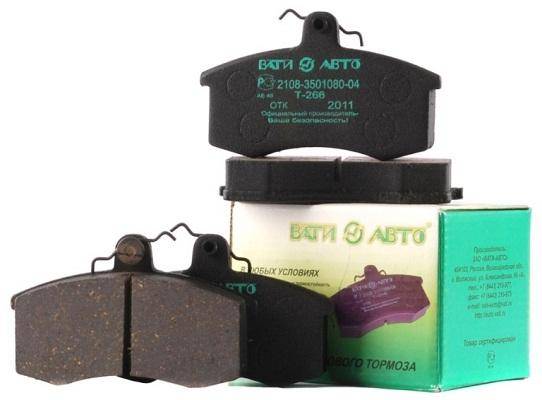
Достоинства:
- Тихая работа;
- Высокая изностойкость;
- Нет скрипов или шумов;
- Низкая цена.
Недостатки:
- Небольшой модельный ряд;
- При сильном нагреве возможна усадка фрикционного материала.
MarKon
Лучшие тормозные колодки для ВАЗ бюджетного сегмента. В ассортименте компании более 500 моделей. Благодаря мягкой фрикционной смеси изделия бережно прилегают к дискам, не дают им изнашиваться раньше времени. Хотя сами колодки достаточно быстро стираются, требуя замены. В среднем их хватает на 30,000-50,000 пробега. В процессе притирки колодки издают скрипы, однако затем они исчезают до конца процесса эксплуатации.
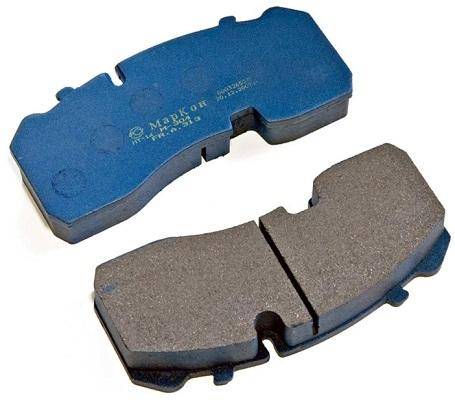
Достоинства:
- Низкая цена;
- Хороший отвод тепла;
- Ремонтопригодность.
Недостатки:
- Нужно часто менять;
- Пылятся.
Какую тормозную колодку лучше купить
При выборе колодок нужно обратить внимание на качество упаковки, ровность, отчетливость надписей на ней. Также обязательно должен быть указан год, страна выпуска, нужно просмотреть наличие знаков сертификации товара, затем осмотреть внешний вид товара. На ней не должно быть сколов или вмятин, накладка должна плотно лежать на основе.
Помимо самого изделия в упаковке обычно лежит паспорт, гарантийный талон, сертификат качества, инструкция по эксплуатации. Специалисты рекомендуют ставить на авто передние и задние колодки одновременно для их равномерного износа.
Выбор тормозных систем для иномарок велик, в ТОП производителей этой продукции вошли:
- Ate – один из лидеров мирового рынка. Эти изделия хороши при любом стиле езды. Также они долговечны и увеличивают срок службы дисков;
- Nisshinbo – самый надежный японский производитель из представленных в рейтинге. Его модели имеют продуманную конструкцию для равномерного контакта с диском;
- Zimmermann – компания, которая гарантирует качество каждого поставляемого на рынок товара благодаря контролю производства и тщательной проверке характеристик. Этим колодкам не нужно время для притирки, они выдают максимальную эффективность сразу после выезда автомобиля из автосервиса;
- Wagner – лучший американский производитель тормозных систем, охватывающий все ценовые сегменты рынка;
- Ferodo – автор экологичных колодок с минимальным добавлением тяжелых металлов во фрикционную смесь;
- Trw Lucas производит лучшую по эффективности торможения продукцию. Они не пылят, выдерживают экстремально высокие температуры. Модельный ряд бренда широк: представляет тормозные системы для автомобилей и мотоциклов;
- Ebc Brakes – лучшие неоригинальные колодки с хорошими показателями эффективности и безопасности торможения.
Лучшими производителями колодок для российского автопрома оказались:
- Sts – компания с самым широким ассортиментом. Ее качество изделий сравнимо с импортными изготовителями;
- Вати – изделия с экологичным составом без асбеста для автомобилей ВАЗ;
- MarKon – самые дешевые колодки из представленных в рейтинге.
Изучив ТОП-10, водитель поймет, тормозные колодки какой фирмы лучше купить для автомобиля, исходя из его манеры езды, финансовых возможностей и технических приоритетов.
Производство Brembo, часть 2: изучаем завод суппортов
В прошлый раз мы побывали на фабрике, которая занимается производством тормозных дисков Brembo. Теперь пришло время отправиться в городок Курно в предместье Бергамо. Здесь находится не только штаб-квартира известного на весь мир производителя тормозов, но и его завод по выпуску суппортов. Смотрим своими глазами на процесс производства.
Напомним, что компания Brembo является предприятием полного цикла, начиная от металлургического производства и заканчивая упаковкой продукции для афтермаркета. У него вообще нет внешних поставщиков: в Brembo абсолютно все делают и контролируют сами. Собственно, это одна из главных причин высочайшего уровня качества и мирового признания компании.
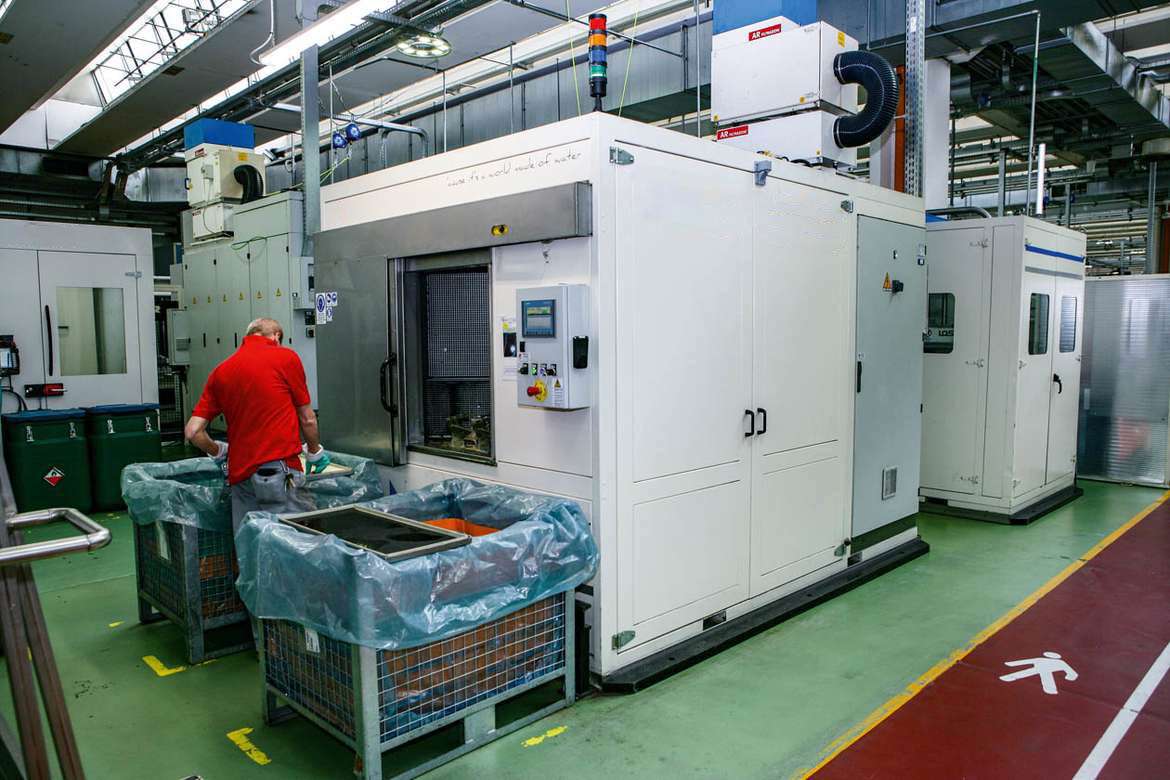
Что касается суппортов, то с точки зрения технологии производства корпуса они делятся на два вида: составные и моноблочные.. Композитный двусоставной суппорт обрабатывается на одном станке и затем собирается в единое целое при помощи болтов. Для моноблочного суппорта нужно уже два станка: на одном обрабатываются наружные части, на другом — внутренние. Основная проблема в том, чтобы качественно обработать места, куда будут установлены поршни. Специально для этого был разработан робот, который может выполнить подобную работу.
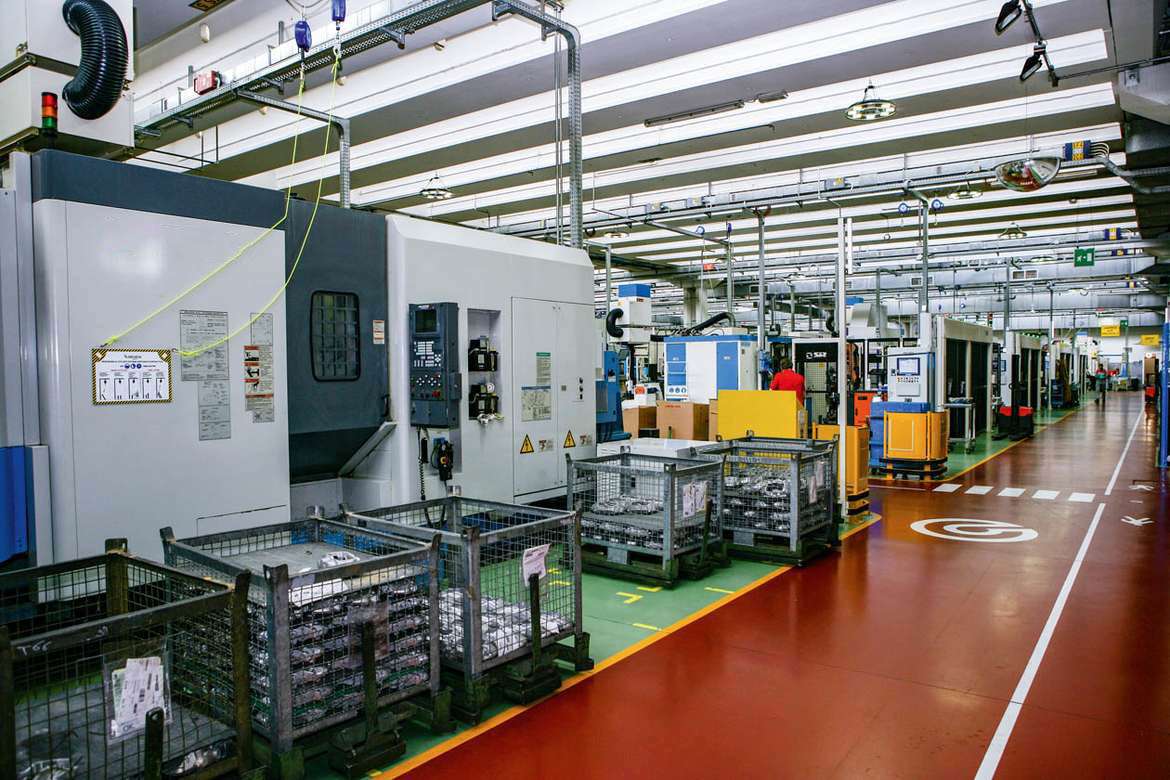
Кстати, вся линия по обработке суппортов полностью автоматизирована, то есть работает вообще без оператора. В начале линии располагается робот, который замеряет все размеры заготовки суппорта в трехмерном измерении. Это нужно для того, чтобы внести корректировки в дальнейшую обработку конкретной заготовки. Раньше этим занимался оператор, теперь же он только загружает заготовки на линию, а далее все автоматически делает машина.В ближайшее время даже процесс загрузки предполагается автоматизировать. Робот будет контролировать уровень загрузки линии и заполнять ее при необходимости.
Производство суппортов работает 24 часа в сутки в три смены. Начинают в 6:00 в понедельник и заканчивают в 18:00 в субботу. Воскресенье — выходной
После обработки заготовок сразу идет зона контроля, где помимо автоматической сверки на линии осуществляется и выборочный контроль качества сотрудником компании. Затем все заготовки суппортов моются под высоким давлением и помещают на специальную раму, чтобы отправить на анодирование.
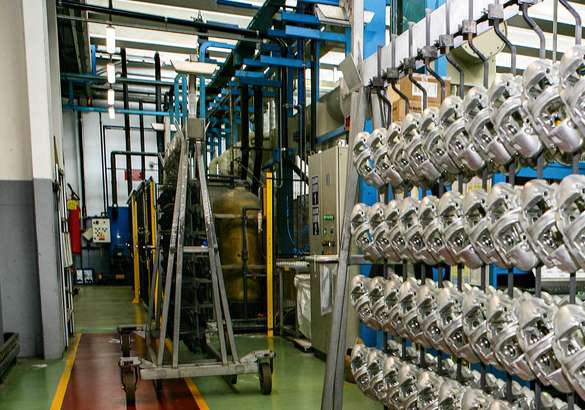
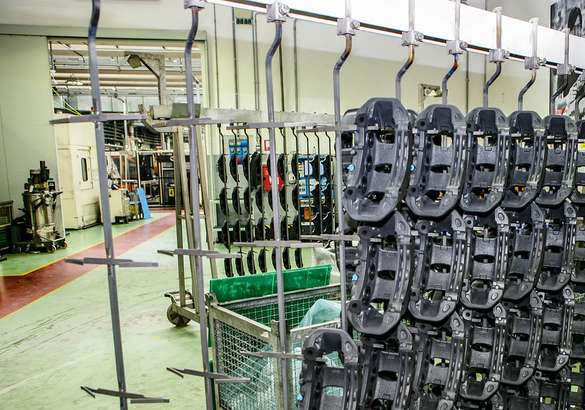
Анодирование — это процесс получения оксидной пленки, которая выполняет защитные функции, в частности оберегает изделие от коррозии и внешних воздействий (соли, реагентов, гидравлических жидкостей), а также придает конечному продукту эстетический вид.
Интересно, что окрашивание в базовые цвета в ходе анодирования сопровождается фирменным процессом фиксации краски, благодаря которому цвет суппорта сохраняется весь срок его службы. Как именно это делается, компания Brembo хранит в секрете.
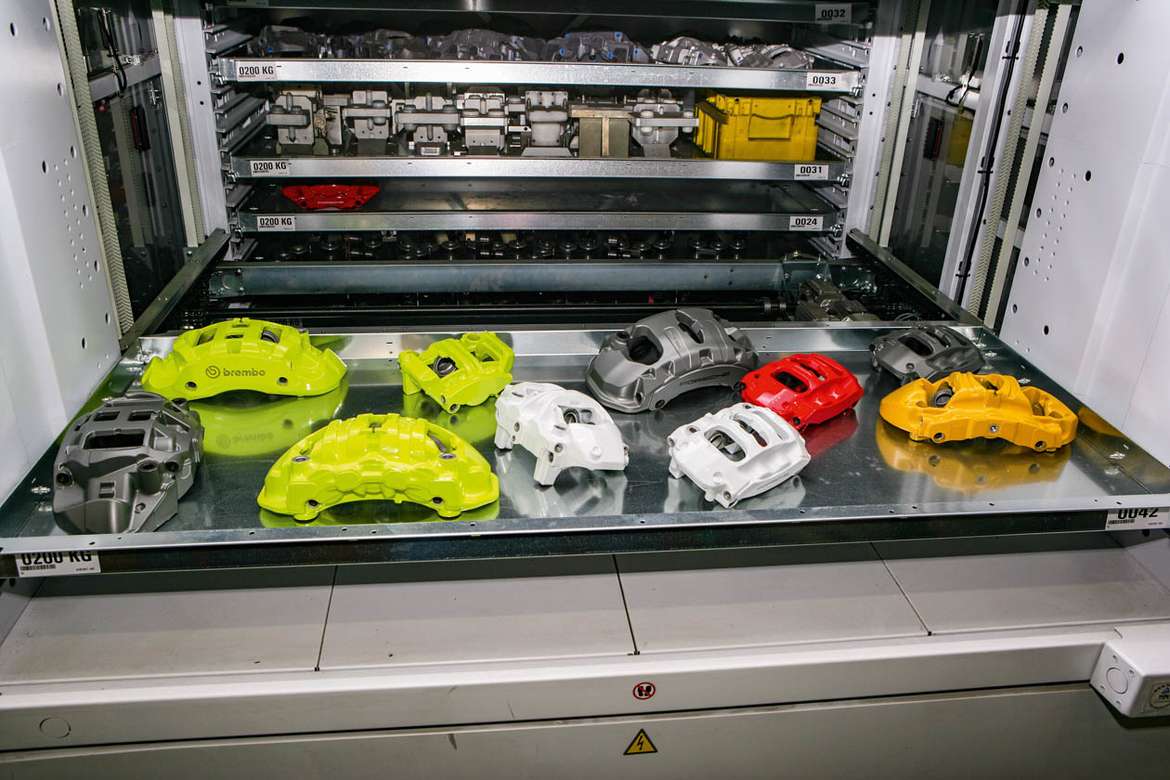
Базовая окраска — 80% суппортов красится в черный цвет, в серый и тёмно-серый — 19%, 1% — голубой цвет для одного заказчика — Maserati.
Линия порошкового окрашивания
На предприятии находится отдельная специальная линия порошкового окрашивания суппортов. Здесь окрашивают суппорта, например, для одного известного немецкого автомобильного бренда. Само собой, линия полностью автоматизированная, все операции делают роботы.
В зеленый цвет Brembo красит суппорты для только для гибридных версий
После окрашивания и сушки на суппорт наносится логотип — Brembo или компании-заказчика, в соответствии с коммерческим договором. Интересный момент: машина для нанесения логотипа использует всего четыре цвета. Логотип в четырех цветах наносится только для М-серии BMW.
На этом конкретном производстве выпускается около 2,5 миллиона суппортов в год.
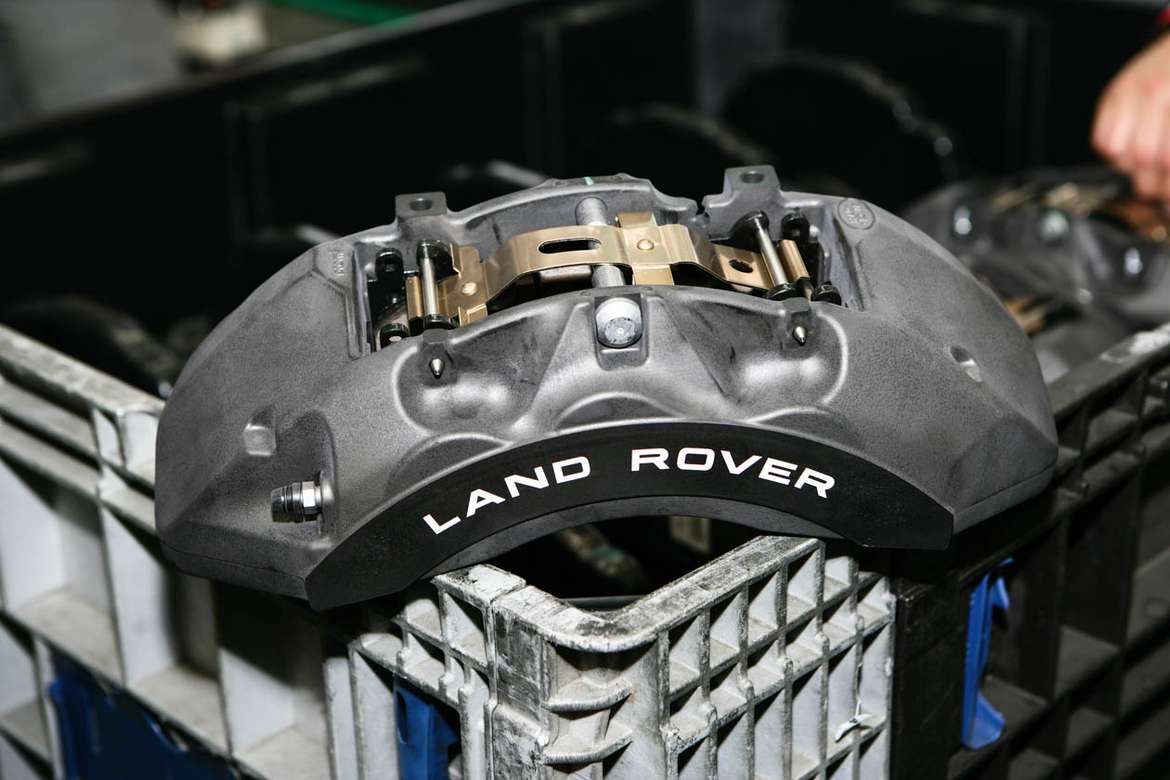
Цех производства тормозных колодок
Производство колодок расположено в отдельном цехе.
Линия по изготовлению тормозных колодок, в отличие от механической обработки дисков или суппортов, не такое эффектное и, в силу самого технологического процесса, достаточно закрытое от глаз производство. В одной части варится фрикционная смесь, которая поступает в формы, находящиеся в другой, нижней части линии. Там, после нанесения смеси на подготовленные специальным образом для лучшей адгезии металлические каркасы, колодки формуют под давлением. Затем их отправляют в печь, где проходит процесс запекания для того, чтобы все компоненты фрикционной смеси соединились воедино. Далее те колодки, для которых предусмотрено спецификацией, отправляются на специальную термическую обработку – скорчинг. В финале готовые колодки ожидает покраска и маркировка.
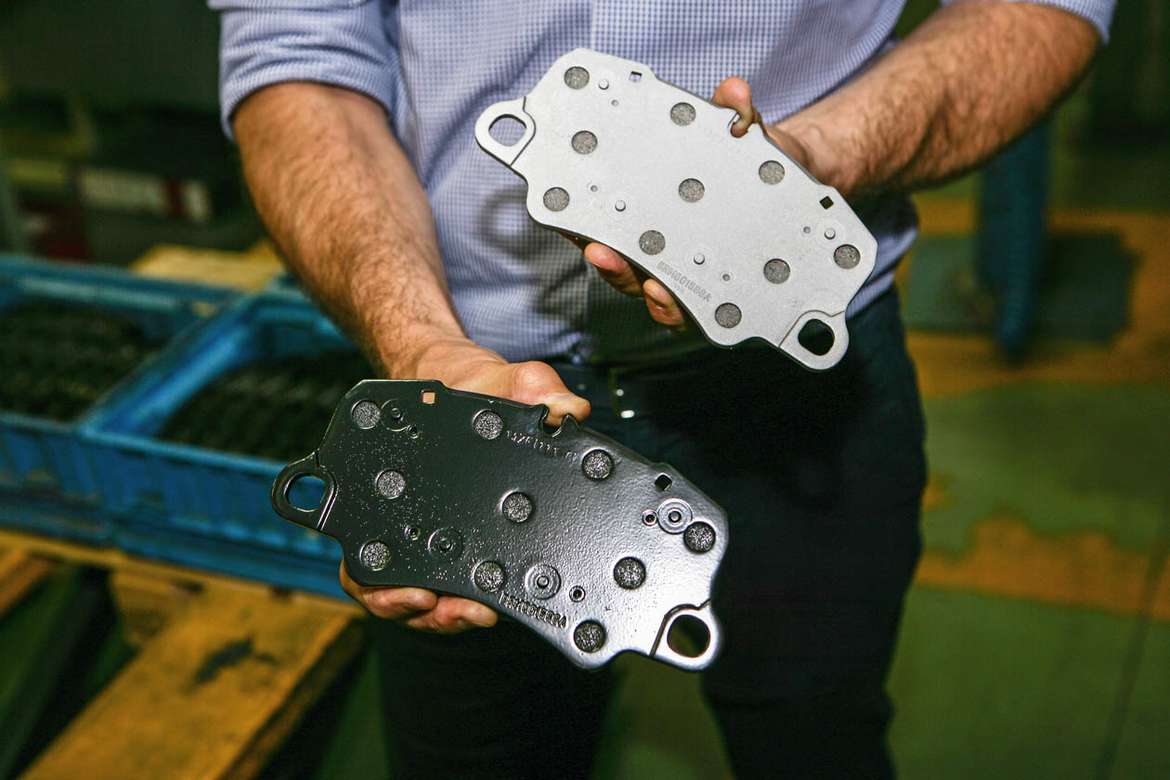
Рецепты фрикционных смесей у Brembo свои. Компания закупает порядка трехсот различных компонентов, которые используются для приготовления 40 различных рецептур смеси.
Стоит обратить внимание, что многие автопроизводители сотрудничают не с одним поставщиком колодок, потому, согласно контрактам, в суппортах Brembo при поставке на конвейер могут стоять тормозные колодки и других производителей.
Сборочный цех
Здесь же, в Курно, находится центральная сборочная линия суппортов, на которой изучают и улучшают все процессы сборки, чтобы в дальнейшем перенести опыт на другие производственные площадки Brembo.
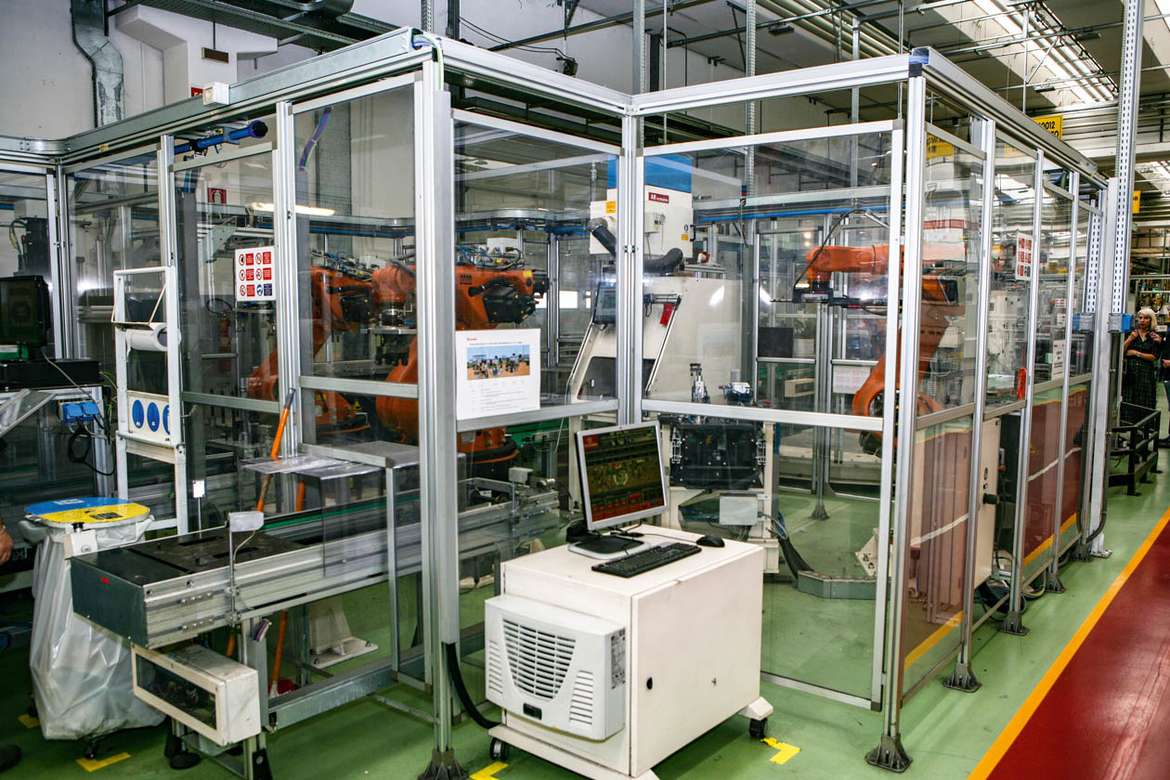
Сборка начинается с установки в суппорт штуцеров для прокачки тормозной системы, а далее лазером наносятся данные (серийный номер, номер партии, дата производства и т. д.), по которым в дальнейшем можно отследить всю историю производства конкретного суппорта.
На следующем этапе суппорт попадает на проверочный стенд, где в тормозной контур под давлением через установленные на первом этапе штуцеры подается воздух. Как только суппорт прошел тестирование и проверку, робот наносит в отверстия для тормозных поршней небольшое количество смазки, после чего суппорт отправляется на установку манжет, поршней, пыльников и прочих компонентов.
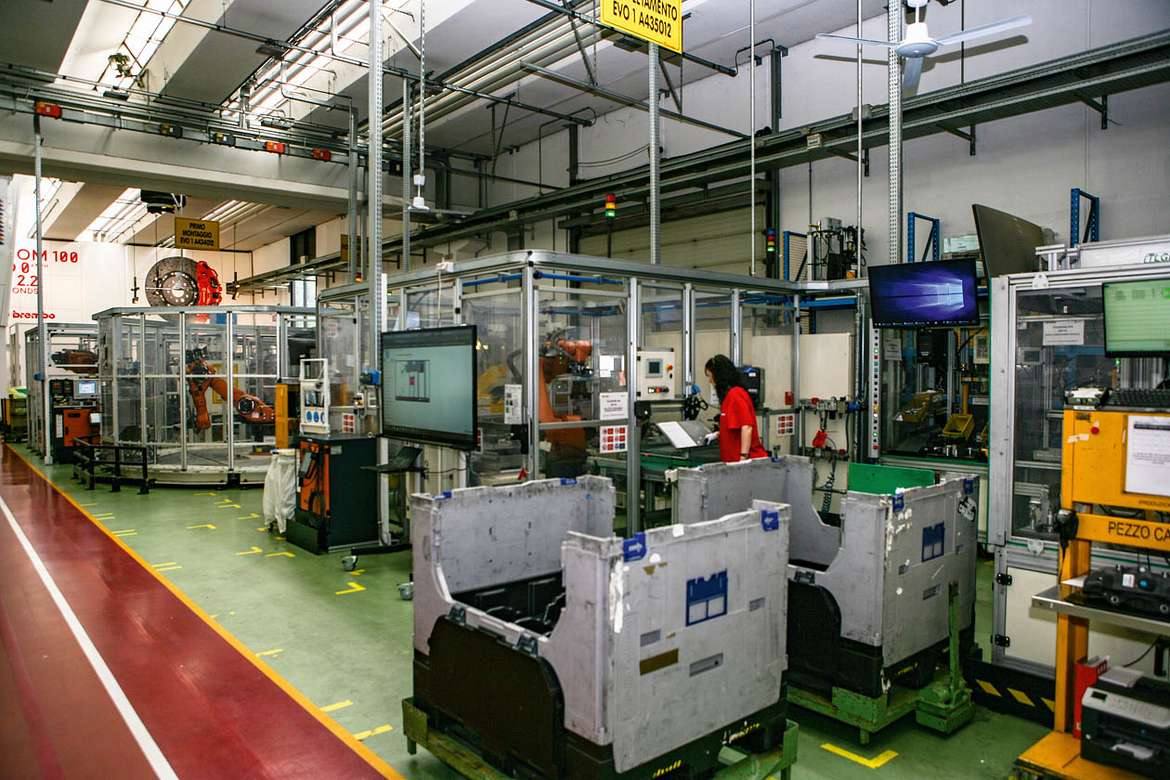
Далее суппорт попадает на стенд, где испытывается на высокое давление и деформацию. Его тестируют под давлением 200 бар, после чего проверяют все параметры на наличие деформаций и повреждений. Если все хорошо, то суппорт попадает на вакуумный тест.
Ну а затем идет уже финальная сборка, когда устанавливаются пружины, направляющие пальцы и остальные детали. Оператор только контролирует подачу комплектующих на линию, а установка осуществляется роботами. На финальном этапе суппорты упаковывают и отправляют клиенту.
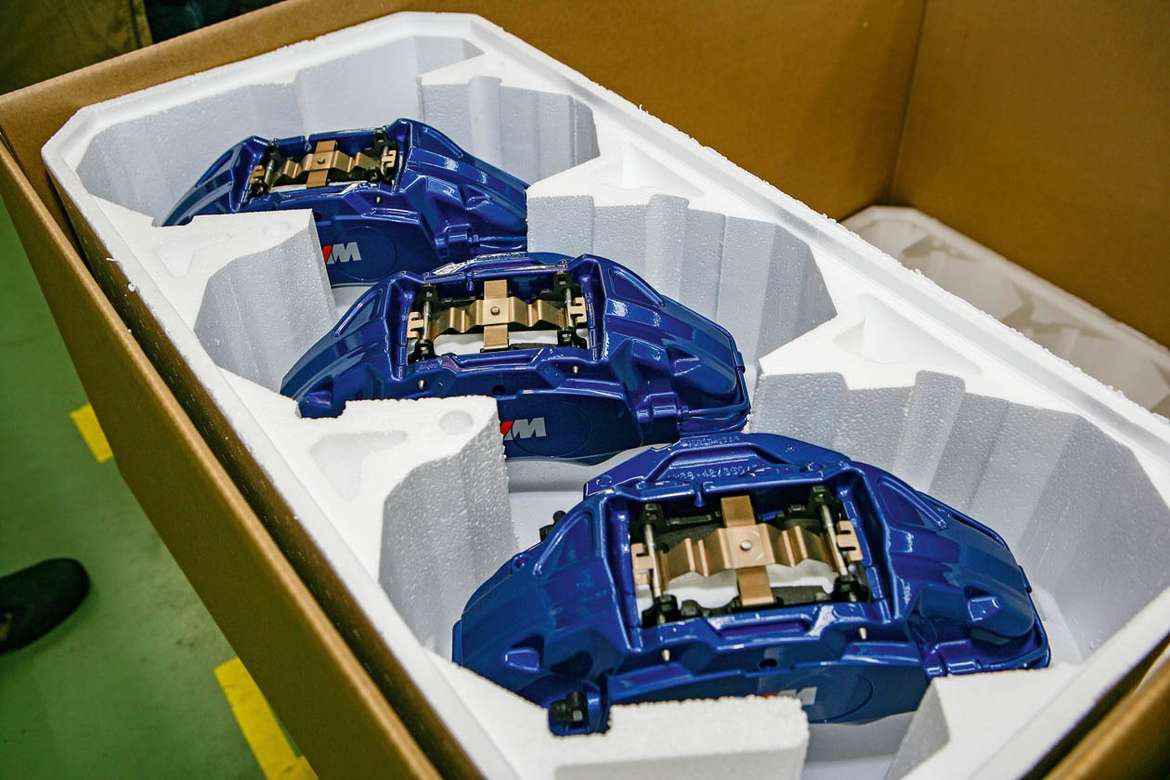

Программа «Индустрия 4.0»
Все производственные линии подсоединены к единой сети и базе данных Brembo. В режиме онлайн можно отследить каждое изделие, на какой производственной стадии оно находится. Данные на мониторе отображаются в реальном времени. После регистрации суппорта все сведения по нему попадают в базу данных и отслеживаются программой.
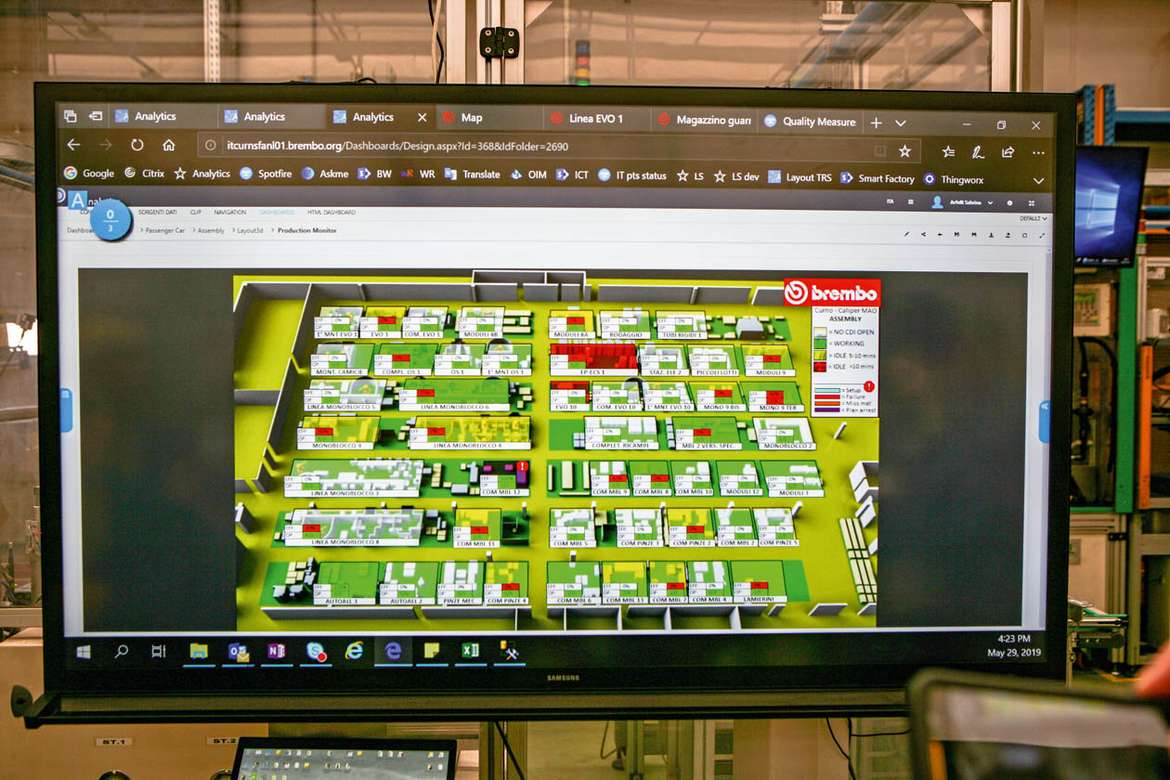
Также программа «Индустрия 4.0» позволяет видеть, какое количество деталей на данный момент находится на конкретной линии, какой артикул сейчас производится, какое количество изготовлено в текущую смену, текущее состояние линии и т.д. Это инструмент, который позволяет полностью следить за процессом производства, получая и анализируя детальную информацию по продуктам.
В дальнейшем на базе программы планируется внедрение интерактивной видеоинструкции для подготовки производственного персонала, где будут пошагово показаны все этапы производства.

Испытательный центр Brembo
В знаменитом технологическом парке Kilometro Rosso, в городке Стеццано, также расположенном недалеко от Бергамо, находится испытательный департамент Brembo. Это тестовая площадка для всех видов транспорта — от мотоциклов до грузовых автомобилей. Обычно процесс происходит следующим образом: сюда доставляются транспортные средства, на которые устанавливаются различные тормозные системы, и затем проводится цикл всевозможных испытаний, чтобы в дальнейшем разработать наиболее эффективные и подходящие под требования тормозные механизмы.
На испытания попадают как предпроизводственные прототипы автомобилей, так и серийные образцы, которым требуется усовершенствование тормозной системы. Например, новый суппорт с улучшенной системой охлаждения или 10-поршневые суппорта с карбон-керамическими дисками и плавающей центральной частью для «заряженных» версий автомобилей премиум-класса.
Здесь же находится передовая лаборатория Brembo Mehatronic Lab, про которую можно без преувеличения сказать, что здесь занимаются будущим торможения.
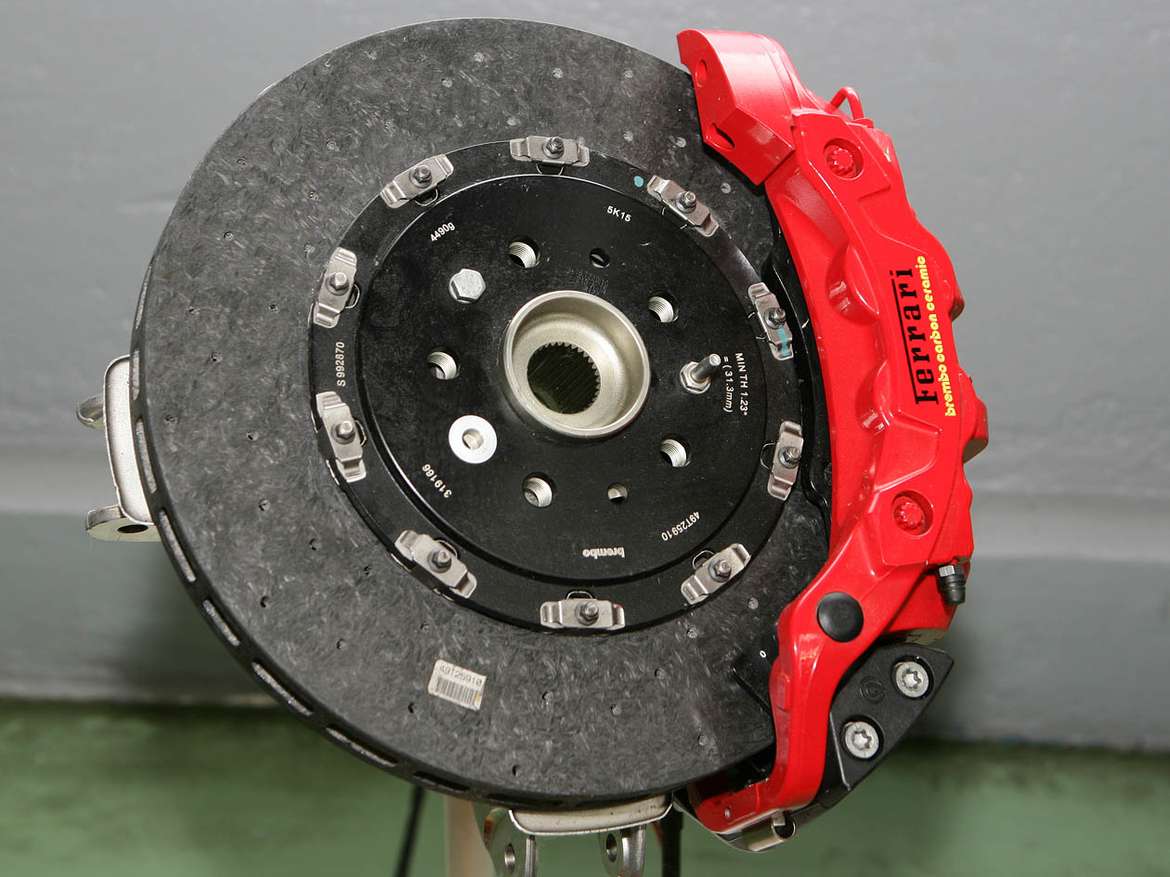
Производство тормозных колодок
Уважаемый читатель, этим материалом мы открываем серию уникальных статей, посвященных производству тормозных систем. Вас ждут уникальные фотографии с фабрики GALFER, которые ни разу ни разу не публиковались ни в одном из изданий. Надеемся, что вам будет интересно.
Завод GALFER, выпускающий тормозные системы для мотоциклов, расположен в Испании на территории, прилегающей к Автодрому Каталунья. Близость к треку позволяет оперативно тестировать продукцию, а так же ускоряет поиск новых составов и решений.
Заводы, изготавливающие тормозные колодки не производят металлические подложки. Дешевле заказывать подложки у специализирующихся заводов чем производить их самим. На фотографии ниже — металлические пластины, подготовленные к усадке фрикционного материала.
В фрикционном материале полу-металлической колодки используется более 20 компонентов — смолы, волокна, частицы металла, клей, органические частицы
Ниже — фотография с опрессованным фрикционным материалом. Специальная машина из подготовленной смеси вырубает пластины заданной формы и толщины. Пластинка кажется толстой? После обработки пластины давлением — она примет точно заданную толщину.
Ниже — уникальное фото — молдинговая машина. Используется при изготовлении не SINTERED составов. Машина использует высокое давление и температуру для «склеивания» фрикционной пластины с металлической подложкой.
Наполовину готовые полу-металлические колодки, вынутые из молдиноговой машины
Оператор, забирает колодки из молдиноговой машины
Ниже — один из важных процессов — доводка. После того как процесс производства закончен, лицевую часть фрикционной пластины с технологическими дефектами стачивают до точной заданной толщины.
С помощью машины ниже, каждая партия проходит проверку на отрыв. Проверка на отрыв определяет насколько прочно фрикционная пластина «приклеилась» к металлической подложке.
Ниже на фотографии — готовые полу-металлические колодки, ожидают нанесения маркировки на металлическую пластину.
Пластины для башмаков (тормоза барабанного типа) изготавливаются отдельно и затем наклеиваются на алюминиевый башмак.
А сейчас вас ждет сюрприз. Один из мифов созданный на отечественном рынке — то что SINTERED тормозная колодка это СИНТЕТИКА. SINTERED не имеет никакого отношения к синтетике и является названием технологии. Эта технология спекания размолотых примесей
металлов и композитов с помощью специальной машины.
Изготовление SINTERED колодок — многоступенчатая обработка температурой и давлением. GALFER использует 6 ступений, обработка начинается с температуры 150С и заканчивается 740С, при этом увеличивается давление, оказываемое на пластину.
Печь загружена, идет пуск. На изготовление SINTERED колодок тратится на 30% больше энергии.
Ниже — уникальная фотография — процесс спечения SINTERED составов. Температура 600С.
SINTER машина
SINTER машина
Изготовленные тормозные колодки упаковываются в цеху. На небольшие парии этикетки (баркод и название) расклеиваются в ручную.
Для больших партий используется специальная машина для расклейки этикеток.
Тормозные диски и колодки: оригиналы и подделки
На глаз, на ощупь и на штангенциркуль
Мы уже сравнивали оригинальные фильтры и их аналоги. Теперь перейдём к не менее важным деталям – тормозным колодкам и дискам. Для сравнения возьмём оригинальные запчасти той же компании Hyundai-Kia и аналоги одной фирмы – китайской Miles. Начнём с колодок.
У нас их четыре комплекта: оригинальные колодки 581012SA70, их аналог Miles с кодом E400055, оригинальные 581014LA00 и их аналог той же фирмы с кодом Е100036. Первые колодки стоят на автомобилях Hyundai ix35, Kia Sportage и Carens, вторые – на Hyundai Solaris и Kia Rio. Итак, берём первую пару.
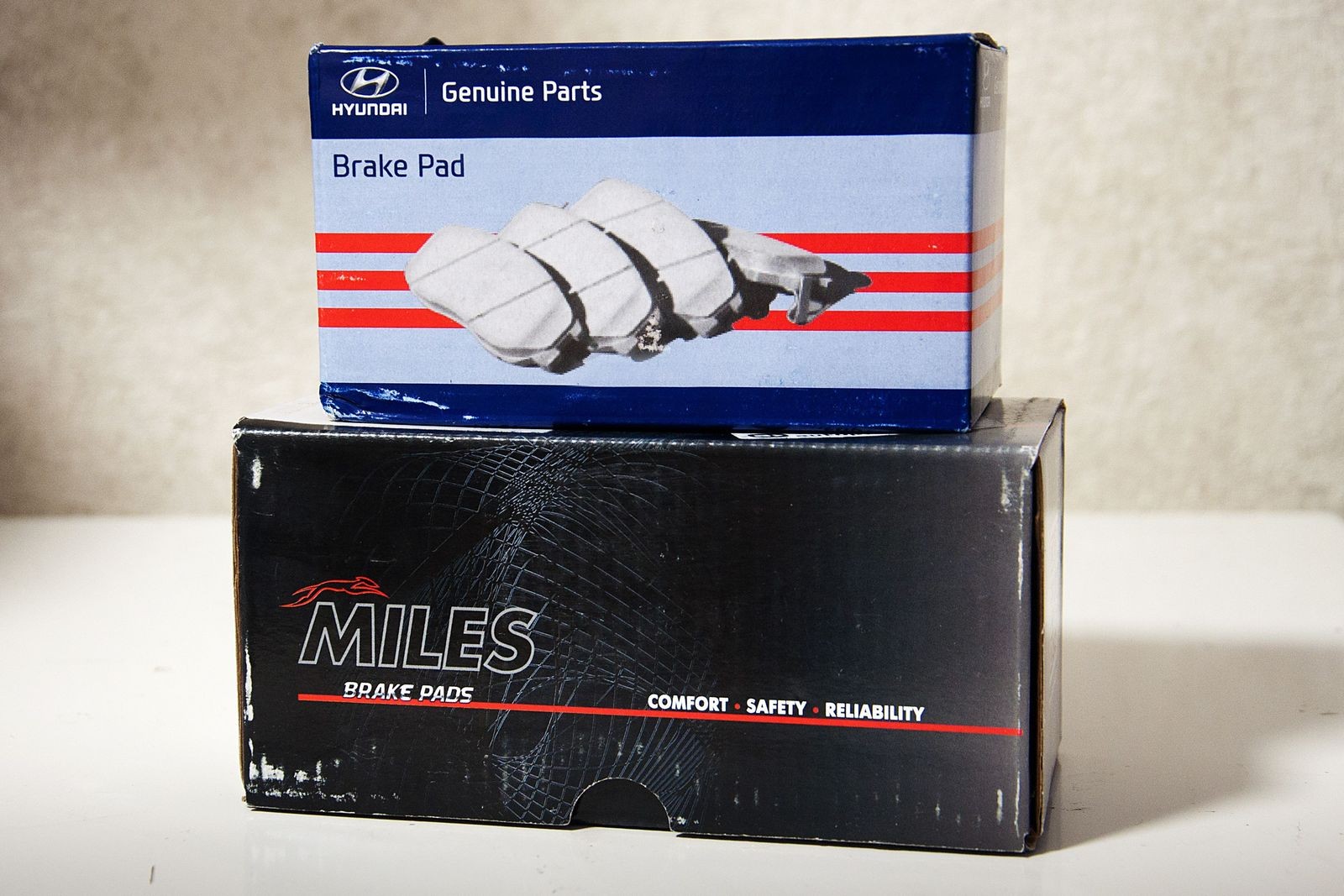
Несмотря на то, размеры оригинальных колодок и их аналогов одинаковы, коробка Miles заметно больше, чем у Hyundai. Интересно, почему? Может, там есть ещё что-то? Да если бы! Но об этом чуть позже.
В целом обе коробки выглядят добротно. У Hyunda-Kia никаких русских надписей на упаковке нет и быть не должно. Впрочем, иногда бывает, что русский язык на упаковке есть, но в этом случае надо сказать «спасибо» тем, кто эти колодки подделал. На оригинальной коробке такого не бывает, но мы в истинности происхождения этих колодок не сомневаемся – они куплены у дилера. И сделали мы это только для того, чтобы быть уверенными в оригинальности запчастей. Как бы это грустно ни звучало, но только таким способом можно обезопасить себя от подделки. Ну а сравнивать подделку и аналог – это то же самое, что сравнивать песни Ольги Бузовой и группы Rasa: убивать в себе эстета.
Информации на коробке Hyundai-Kia традиционно немного.
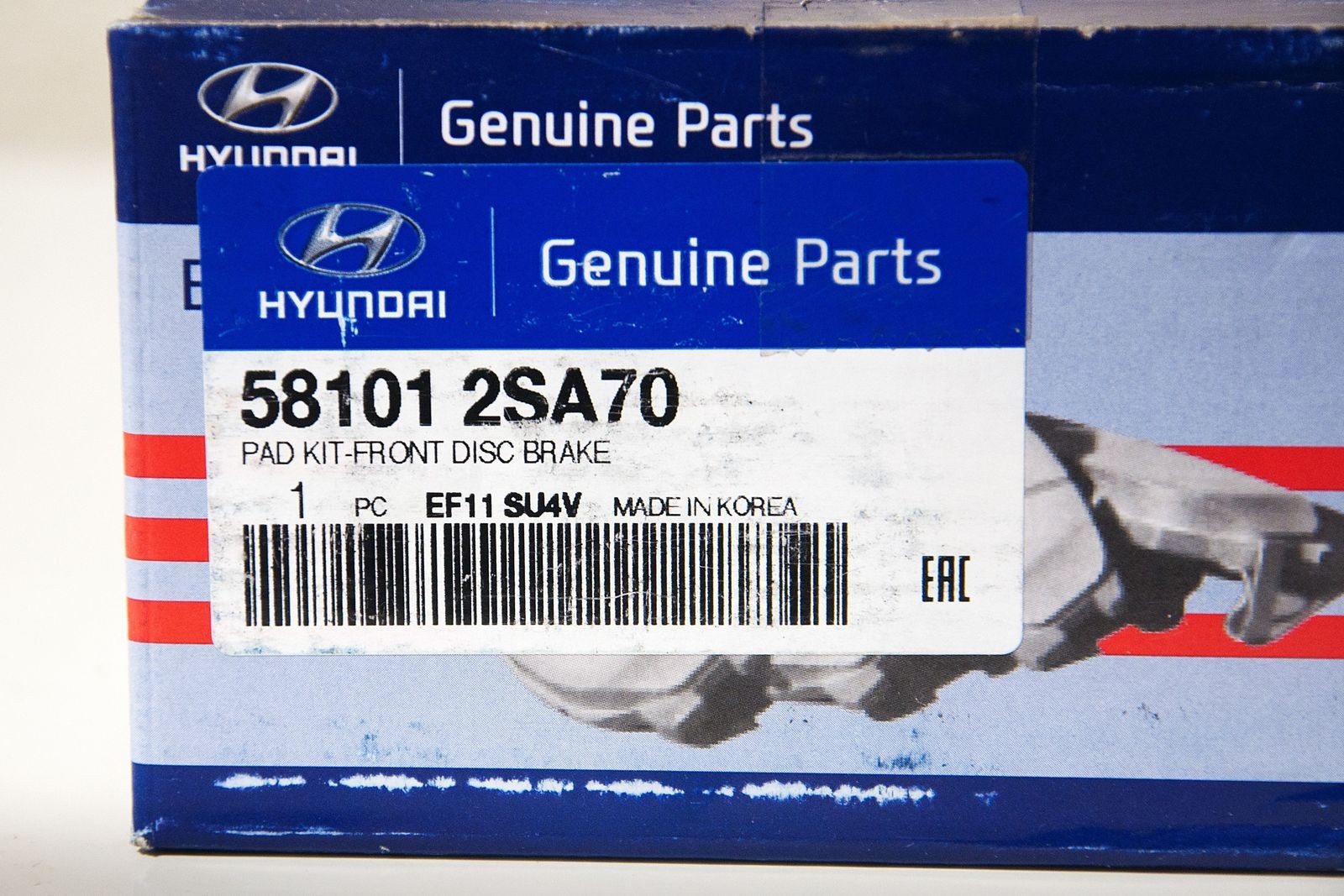
И всё же вся необходимая информация есть: в коробке лежит комплект передних тормозных колодок с номером 58101 2SA70. Этого вполне достаточно. Производитель ОЕМ-колодок для Киа и Хёндэ – корейская компания Mobis. Об этом нигде не говорится, но это и не так уж важно. Теперь открываем коробку и смотрим, что нам туда положили.
Сразу есть хорошая новость: у нас тут есть новые пружинящие и противоскрипные пластины.

Да и сами колодки выглядят прямо-таки богато, а не просто добротно. Приятно даже в руки брать.
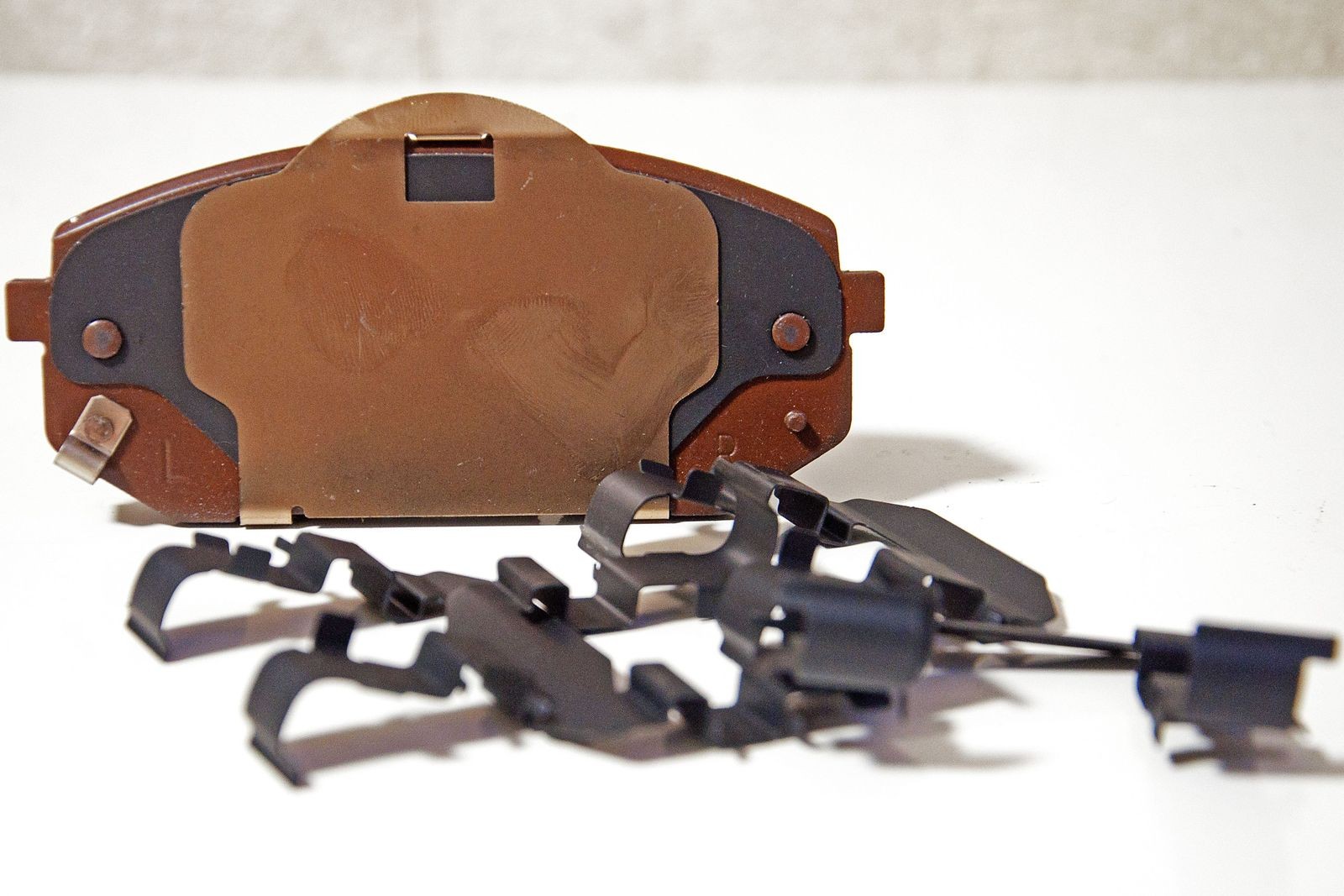
А вот инструкция далеко не подробная. Видимо, сделан расчёт на то, что купленные у дилера колодки ставить должен тоже дилер. Наверное, это правильно: если автолюбителя останавливает отсутствие инструкции, колодки самостоятельно ему лучше не менять. Целее будет.
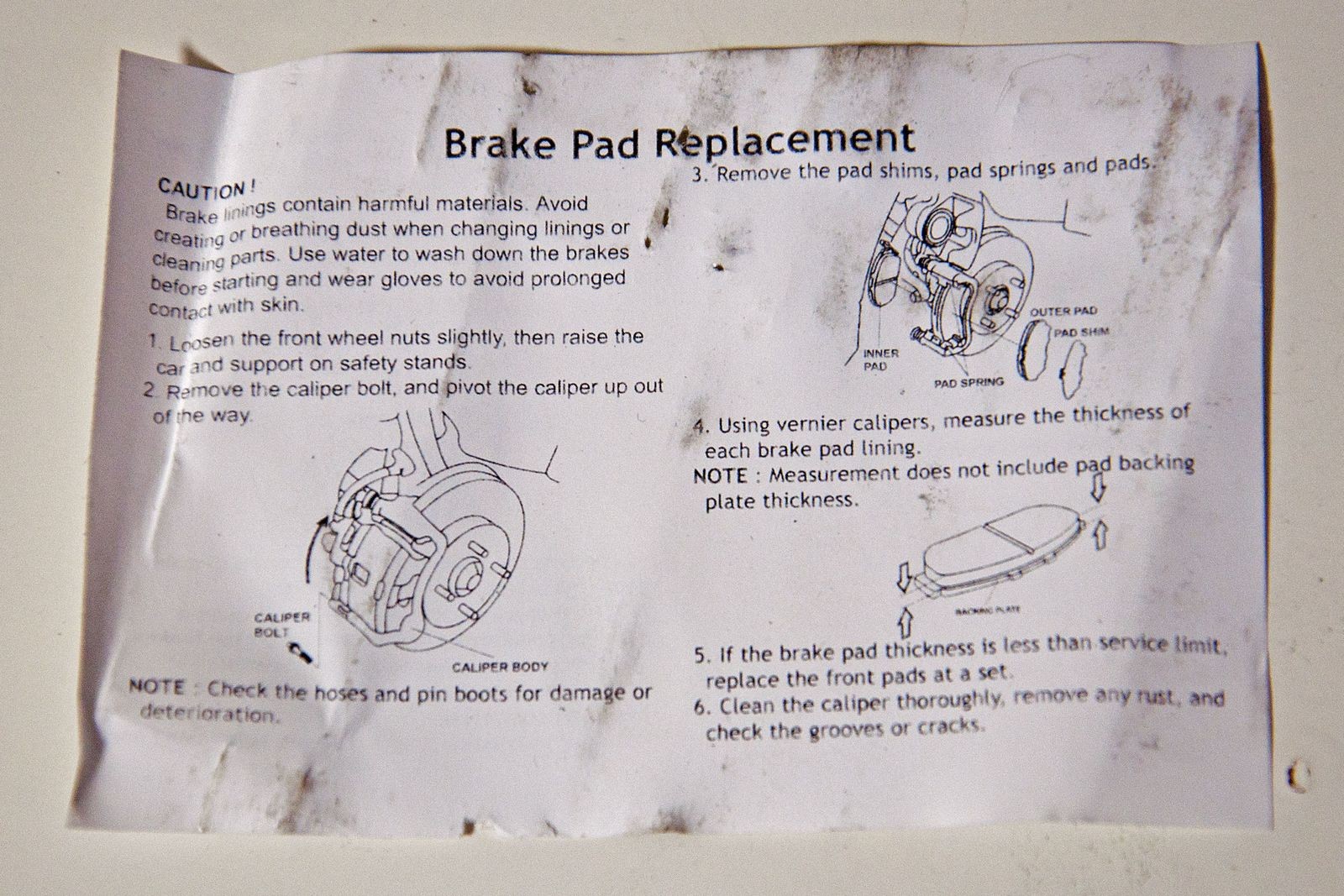
Нельзя не отметить очень однородный состав фрикционных накладок. Никаких крупных вкраплений не видно, все края ровные и аккуратные.
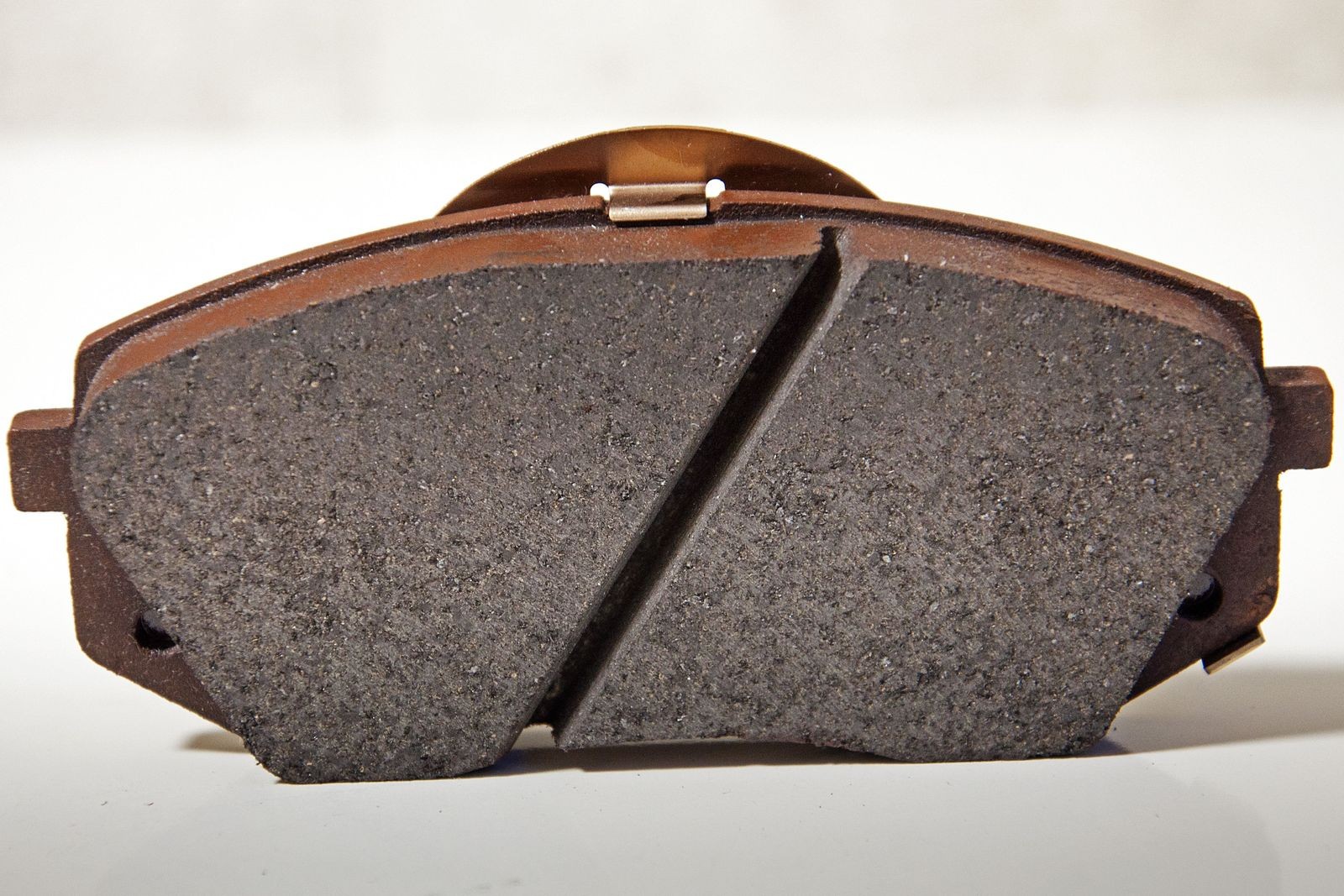
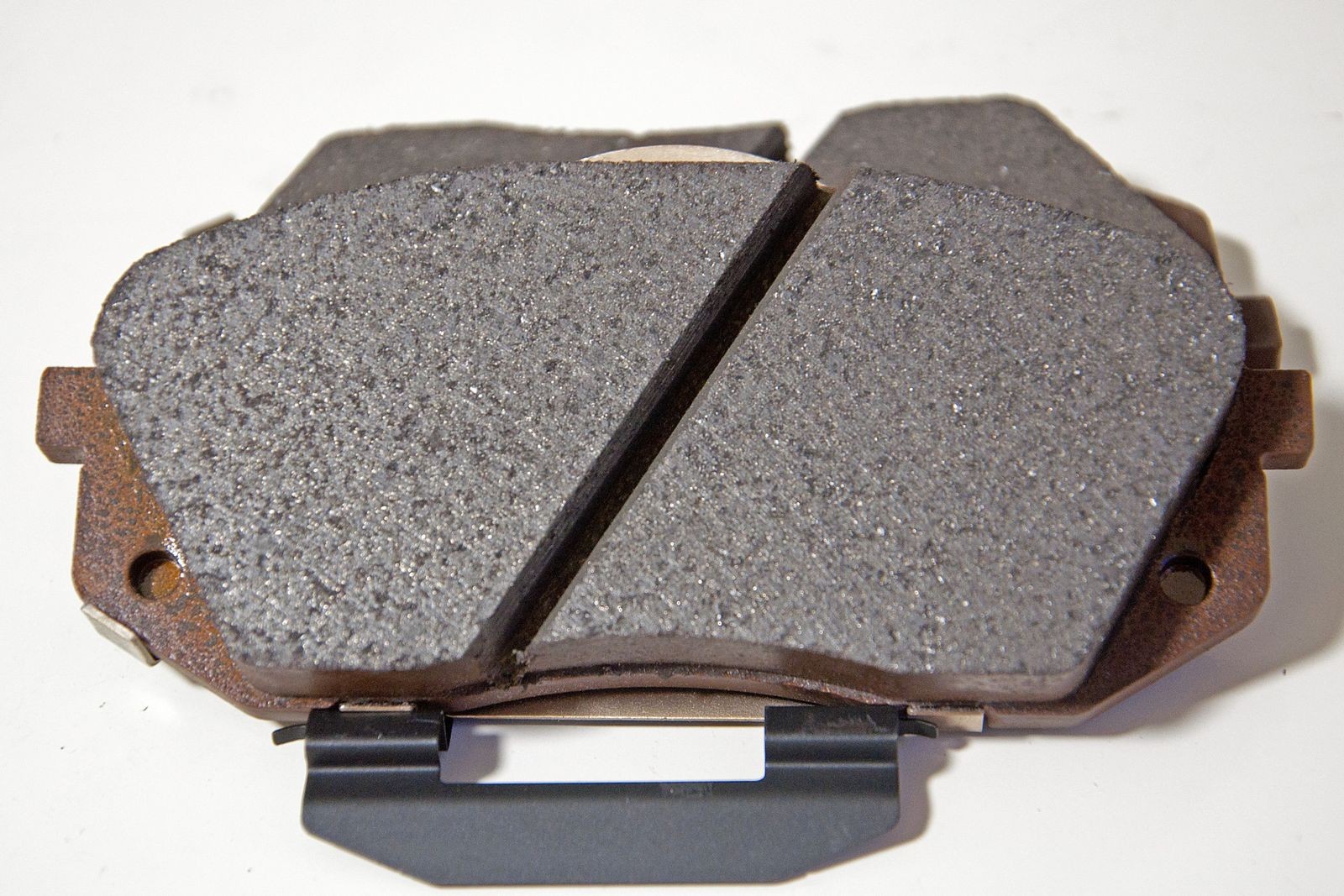
На глаз-то всё кажется ровным. Но давайте ради интереса проверим толщину колодки и накладки штангенциркулем. Это поможет нам выяснить, насколько ровно сделана и накладка, и стальная основа колодки.
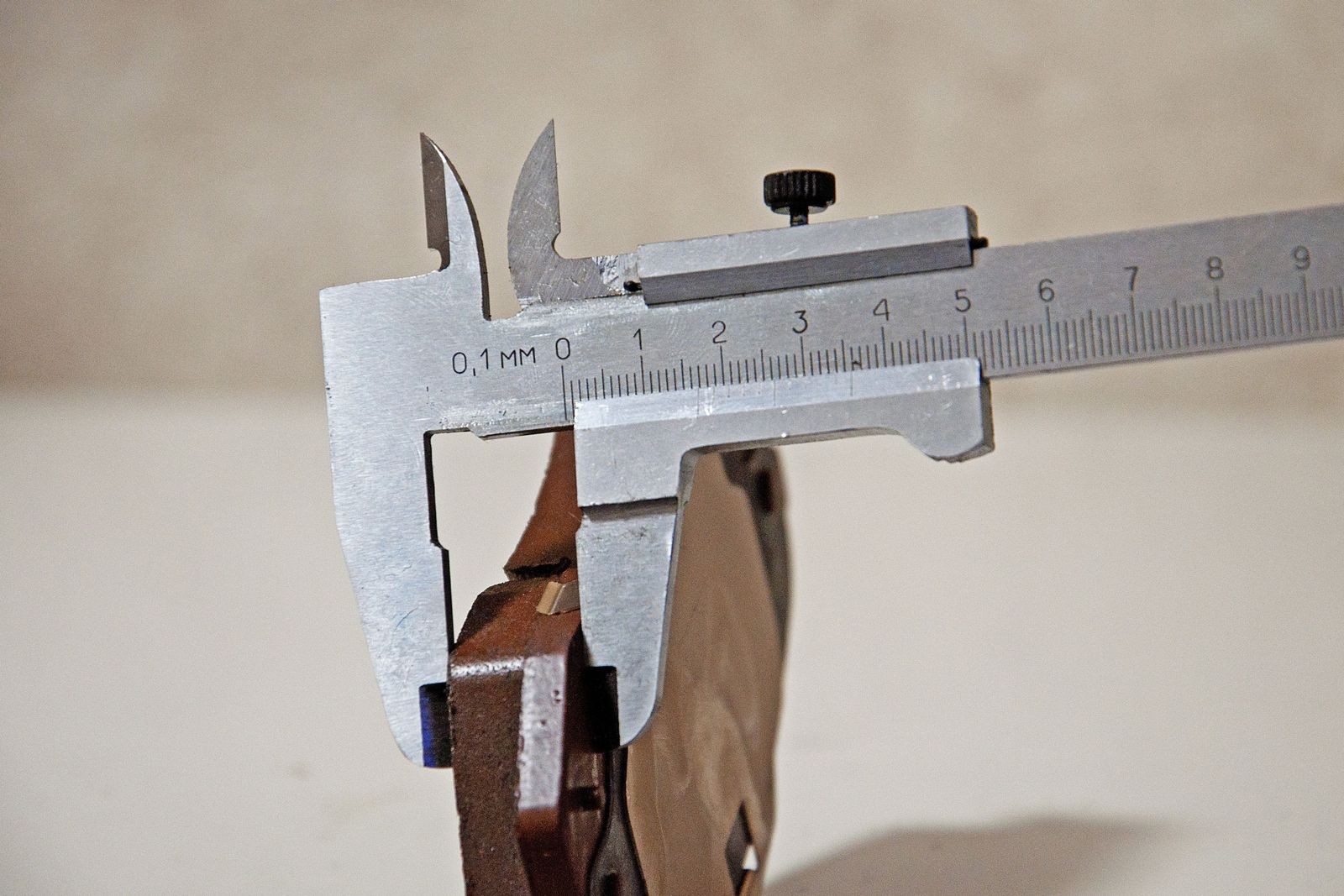
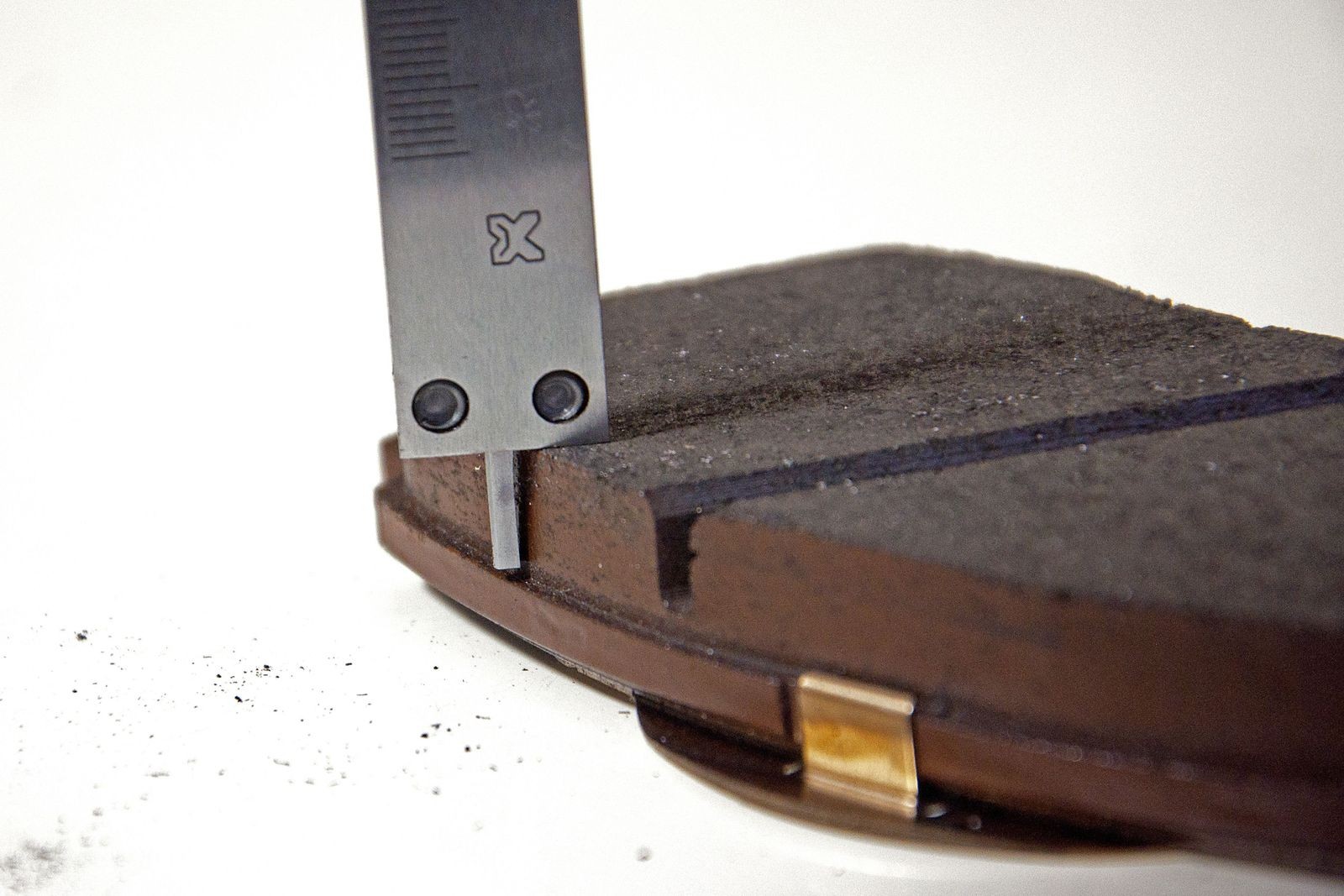
Толщина колодки целиком – 17,6 мм. Самое интересное, что все четыре расходника во всех точках замера показали абсолютно одинаковую толщину. То же самое произошло и с накладкой – её толщина везде равна 11,0 мм. Сами по себе нам эти цифры ничего не дают, но мы их запомним. И перейдём к коробке с аналогом.
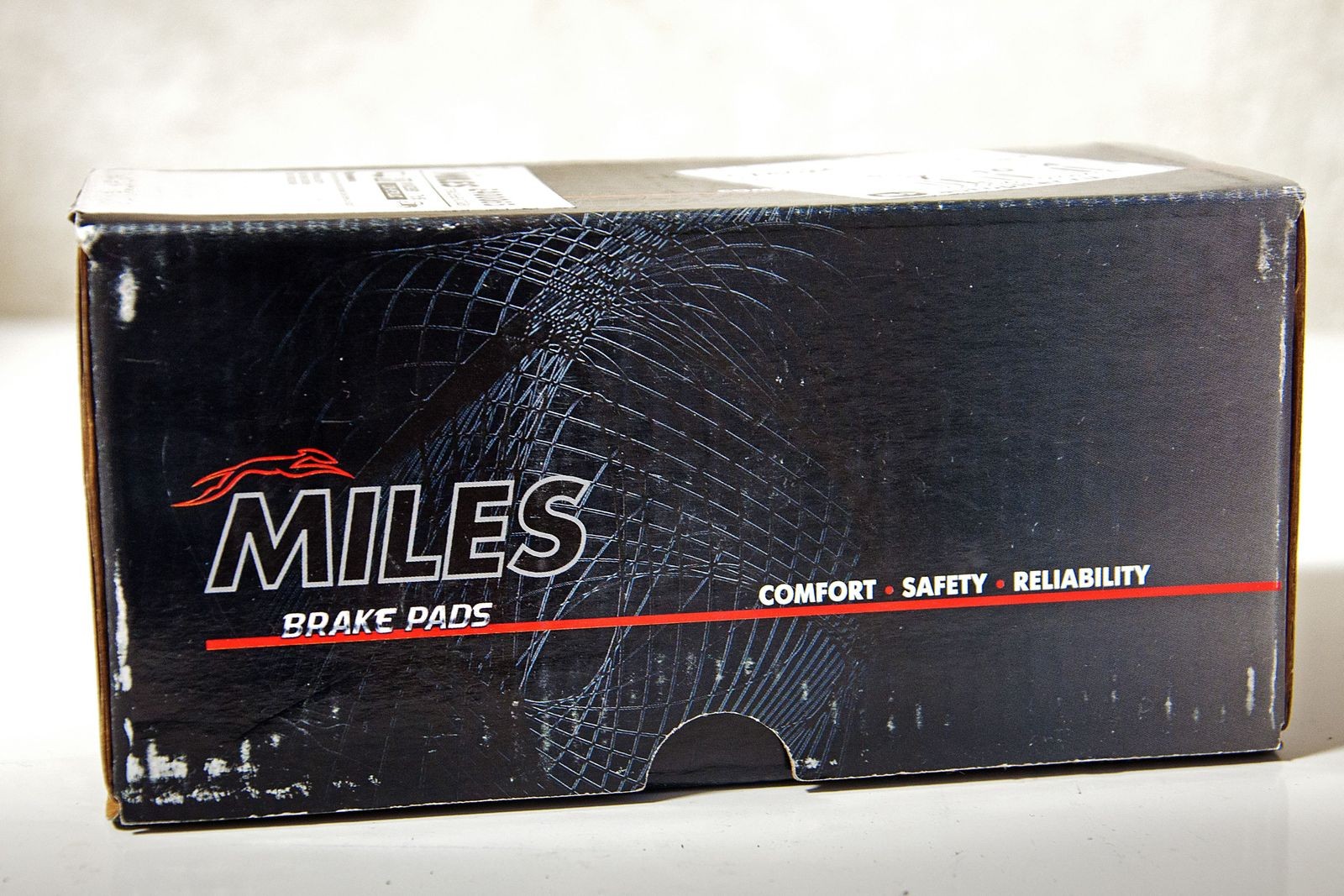
Как я уже говорил, упаковка у этих колодок неплохая. Есть и список машин, на которые при желании их можно поставить.
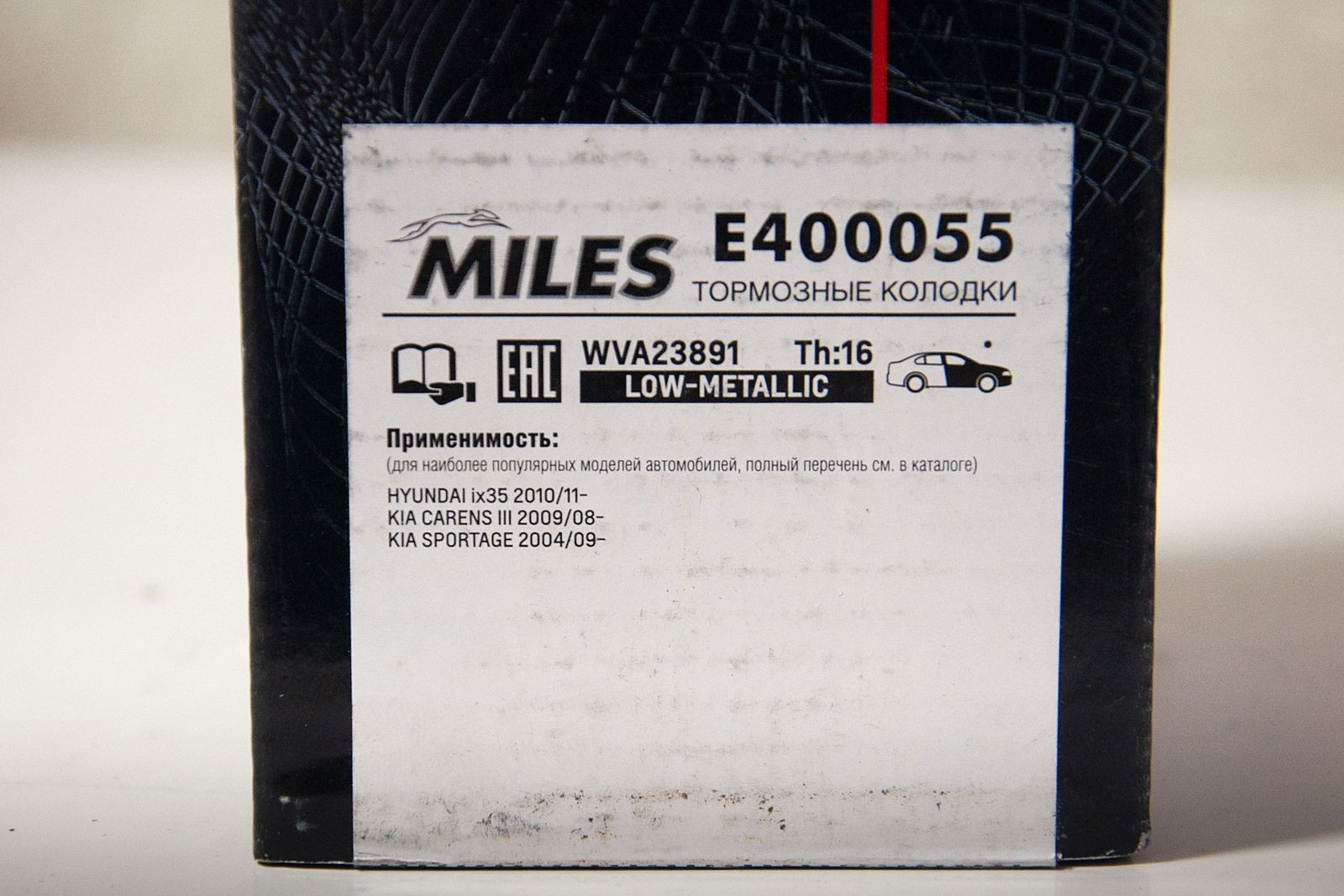
Колодки не просто так лежат в коробке, а упакованы в полиэтилен. Есть даже весьма подробная инструкция по их замене с незначительными ошибками в русском языке. А с другой стороны инструкции – просто нарисованная схема замены. По-моему, неплохо.
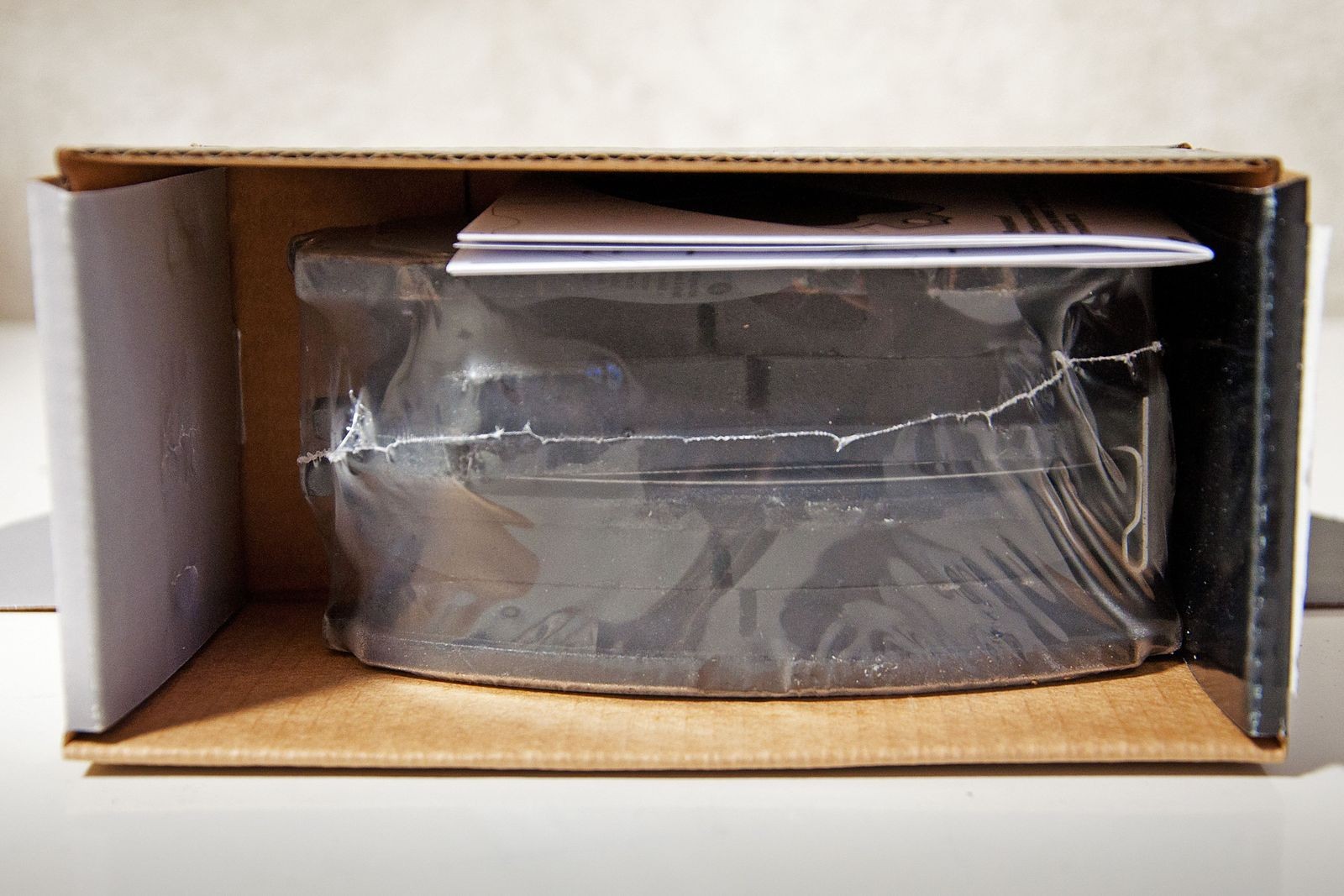
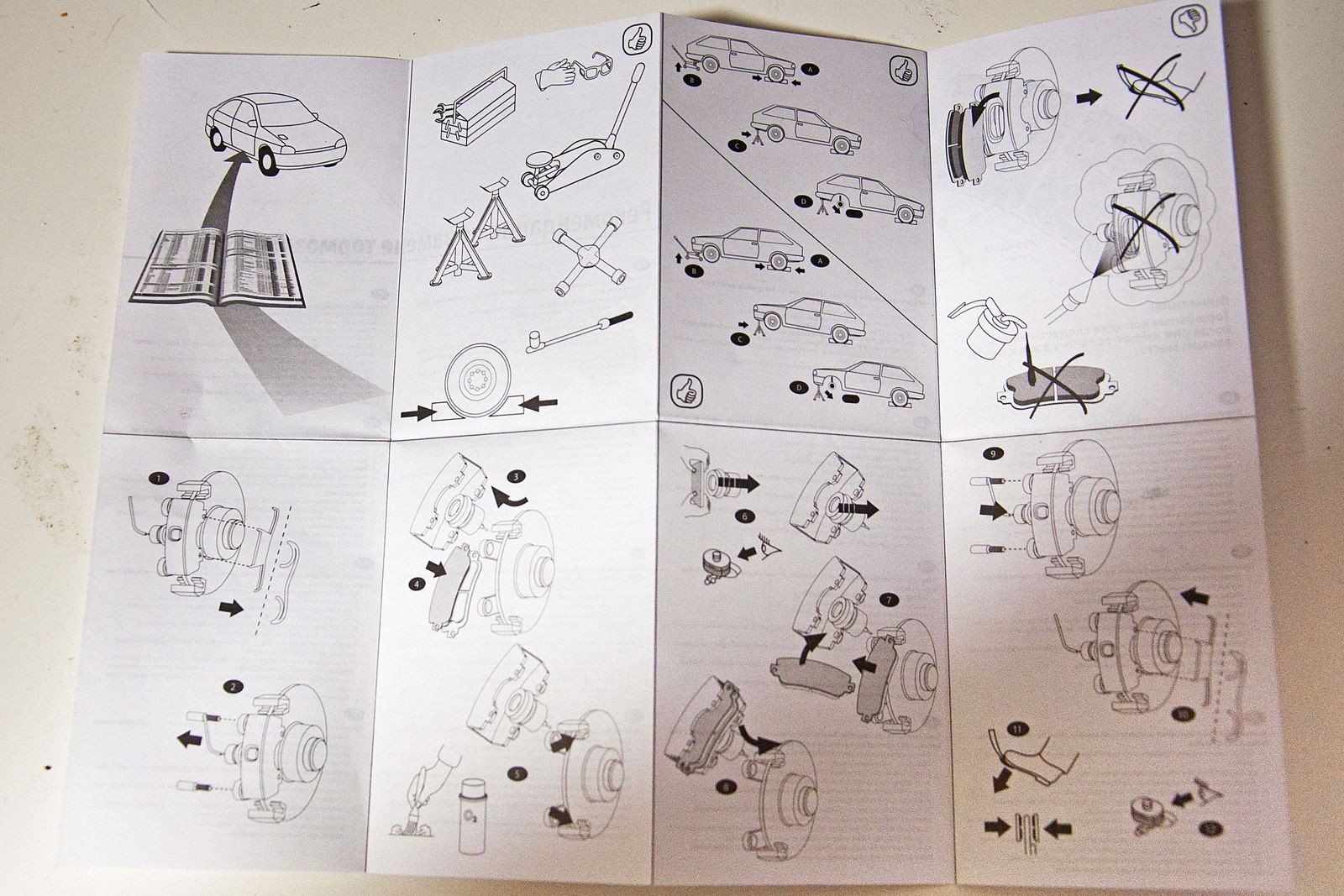
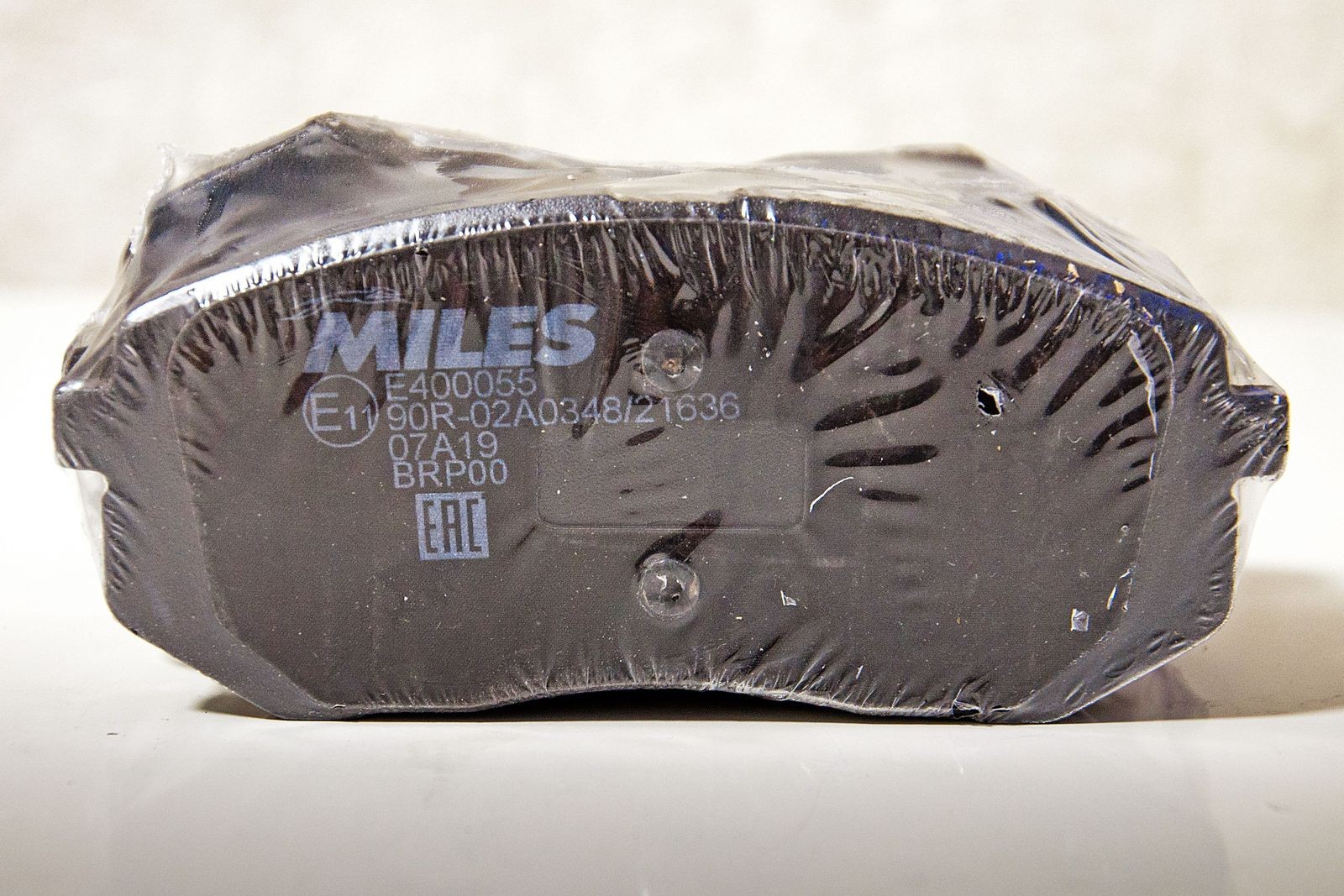
К сожалению, на этом хорошие новости заканчиваются.
Во-первых, тут нет никаких скоб. Это не очень хорошо, потому что придётся или ставить колодки без них, или ставить старые скобы. Вроде бы пустяк, но ездить с грохотом из суппортов – занятие не самое приятное. Кроме того, лишнее соприкасание колодок с дисками приводит к ускоренному износу первых, а иногда – к перегреву тормозных механизмов. Каких-то слишком тяжелых последствий не будет, но всё же.
Во-вторых, сами колодки без упаковки выглядят заметно хуже. Рассмотрим внимательно накладку.
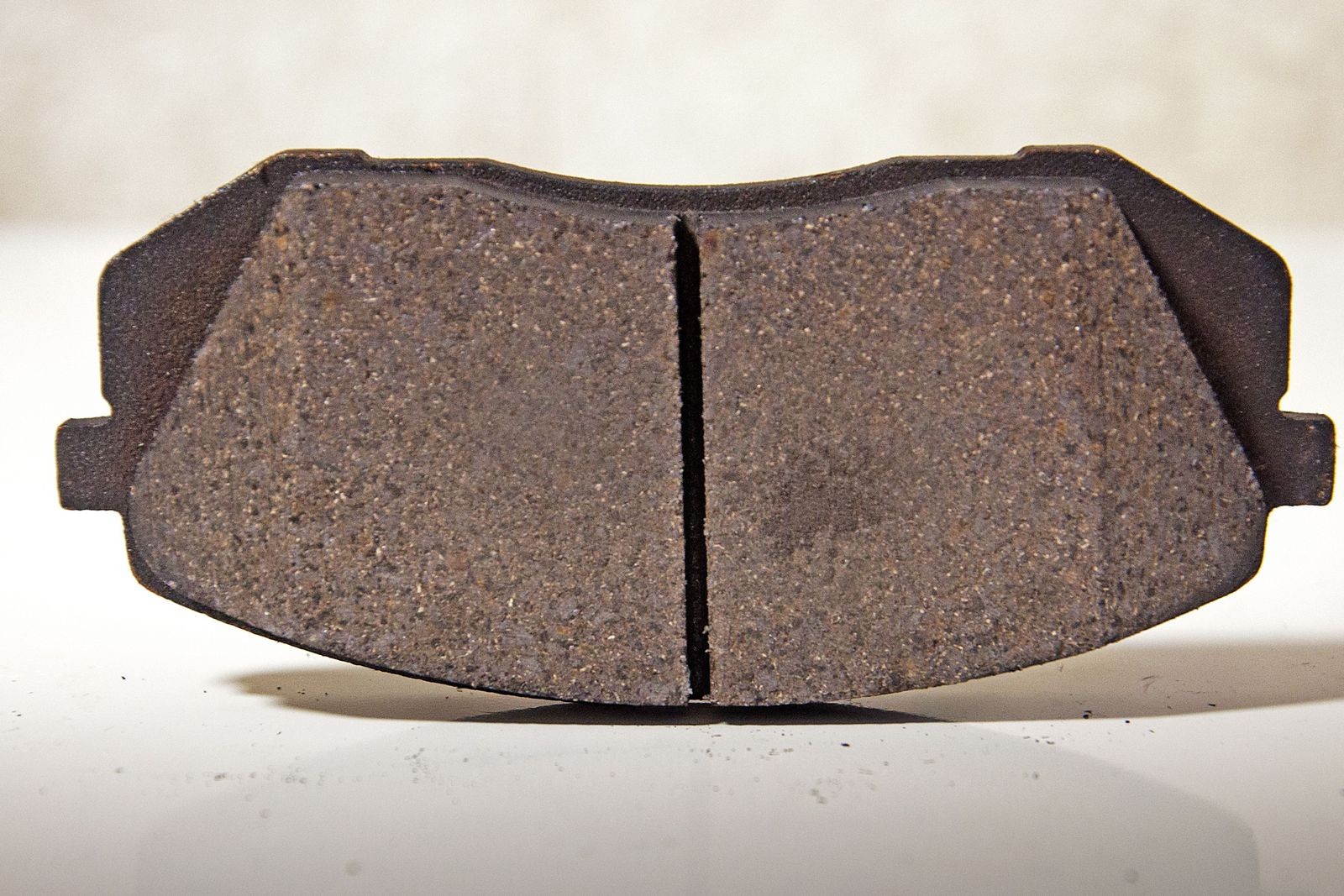
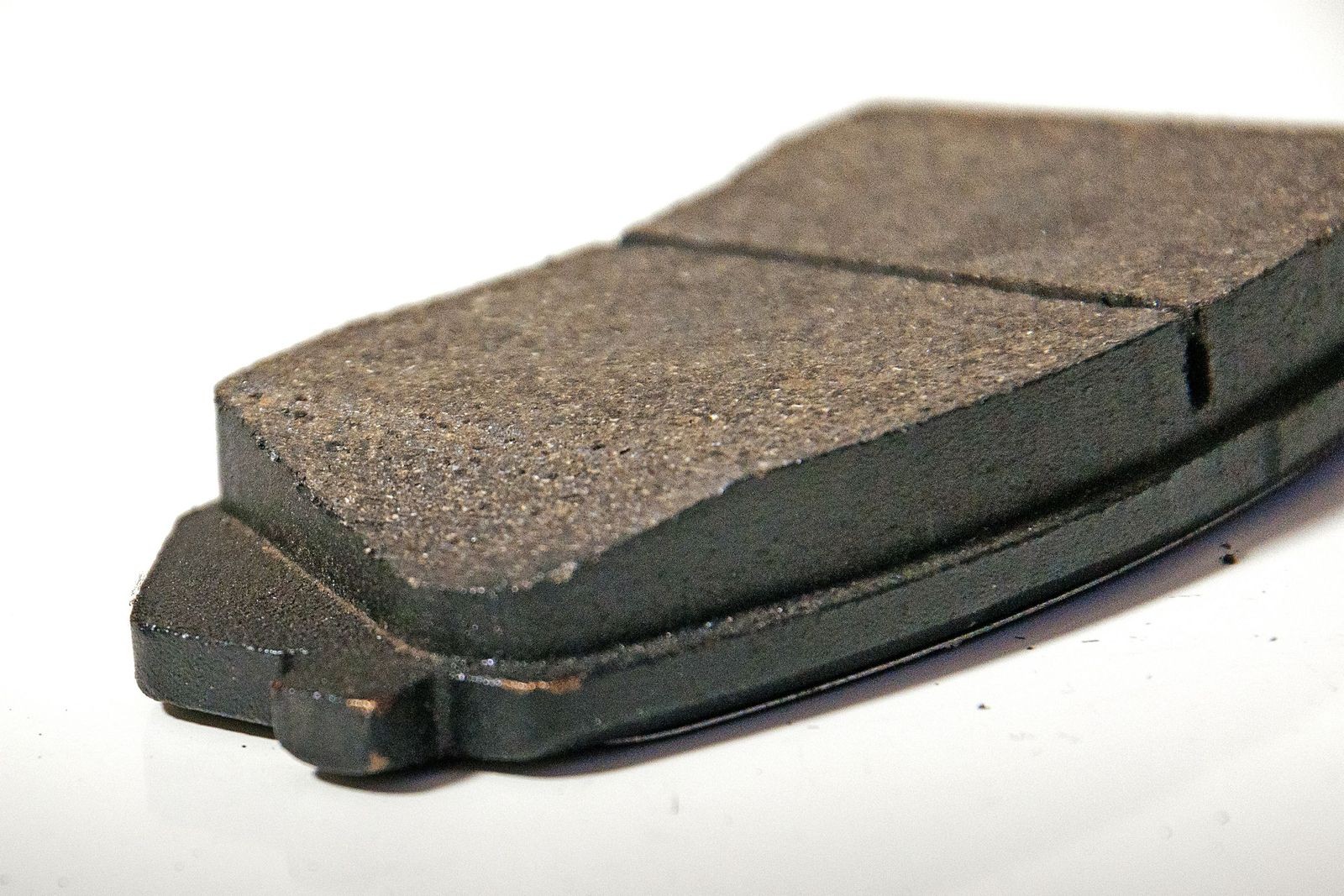
Она не такая однородная, как на оригинальной колодке. Очень заметны крупные вкрапления, которые даже делают край рабочей поверхности неровным. Чем плохи такие крупные частицы? Во-первых, они быстро выпадают из накладки. И как минимум сильно загрязняют и тормозные механизмы, и диск колеса. Ну а во-вторых, они быстро изнашивают тормозной диск. Если, конечно, частицы для этого достаточно твёрдые. А обычно они как раз и нужны для того, чтобы сделать накладку более жесткой: от этого зависит ресурс самой колодки. Но у этой медали есть и обратная сторона: чем колодка твёрже и чем выше её ресурс, тем быстрее «кончается» диск. По большому счёту желательно использовать диски и колодки одного производителя – они должны работать в паре. И если на машине стоит ещё родной диск, то и «родная» (то есть оригинальная) колодка с ним будет работать лучше всего. А что сделает с диском такой аналог – это вопрос.
И это ещё не всё. Колодка оказалась немного кривой и… тонкой! Как я уже говорил, толщина всех оригинальных колодок во всех точках замера была одинаковой – 17,6 мм. А вот толщина колодок-аналогов оказалась в пределах 16,4-16,5 мм. А толщина накладки – 9,5-9,6 мм против 11,0 мм у аналога. Полтора миллиметра – это довольно существенная разница, около 15%. Если представить, что физические свойства накладок у аналога и оригинала одинаковые, то получается, что на колодках Киа можно проехать 100 тысяч километров, а на аналогах – 85 (тут, конечно, всё зависит от характера вождения, поэтому цифры очень условные). Если же состав отличается (а, судя по внешнему виду, так оно и есть), то либо ресурс колодок будет одинаковым за счёт сокращения ресурса диска, либо колодка износится ещё быстрее (если накладка аналога будет не такой твёрдой, как у оригинала). И то, и другое – дополнительные траты, которые вполне способны перекрыть мнимую экономию при покупке аналога. А что поделать: бесплатный сыр бывает только в мышеловке.
Давайте теперь откроем вторую пару колодок: Kia 581014LA00 и Miles с кодом Е100036.
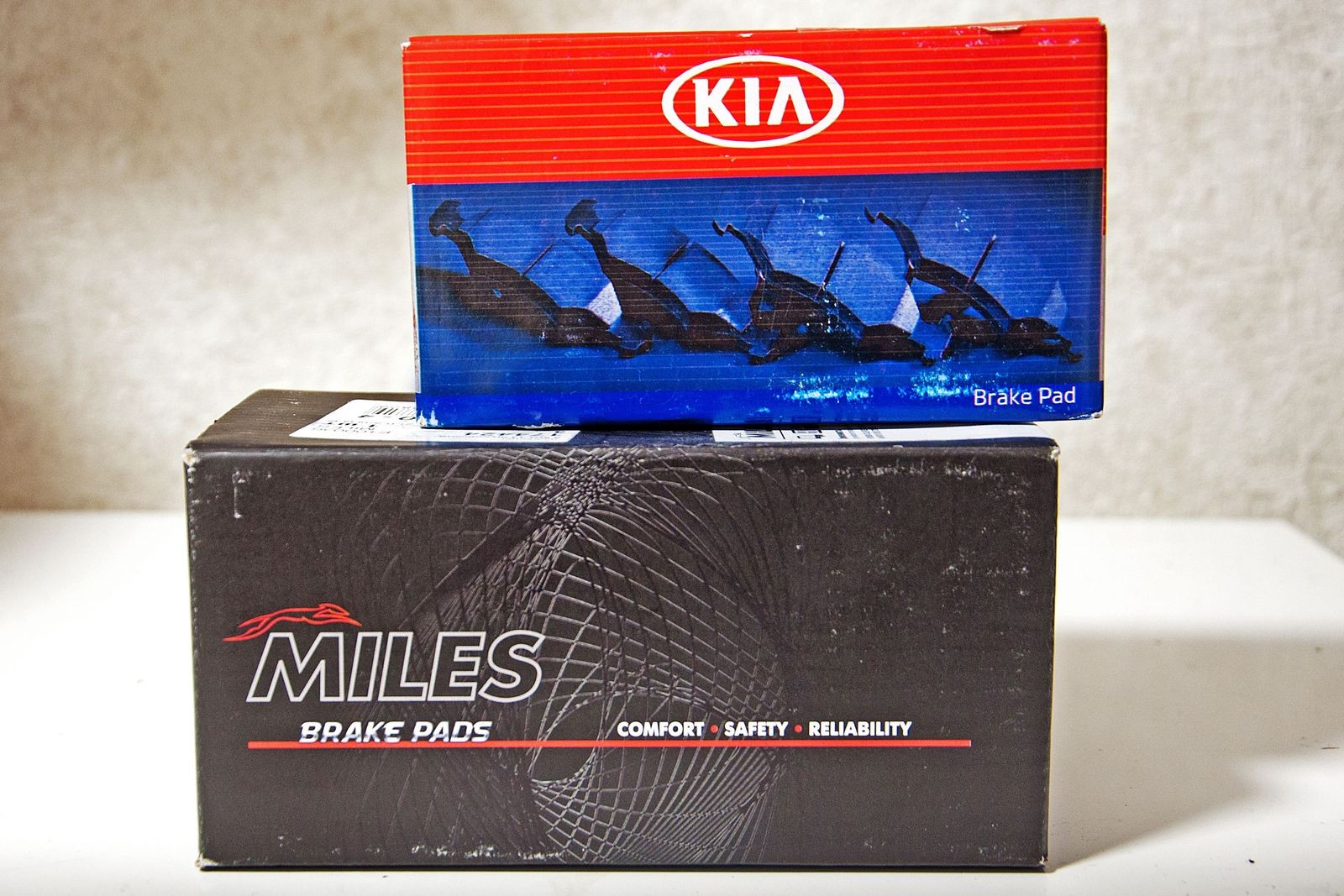
Тут оригинальные колодки упакованы в хорошо узнаваемую коробку от Kia, а не Hyundai. В остальном упаковка такая же: только необходимая информация и не слишком подробная инструкция.
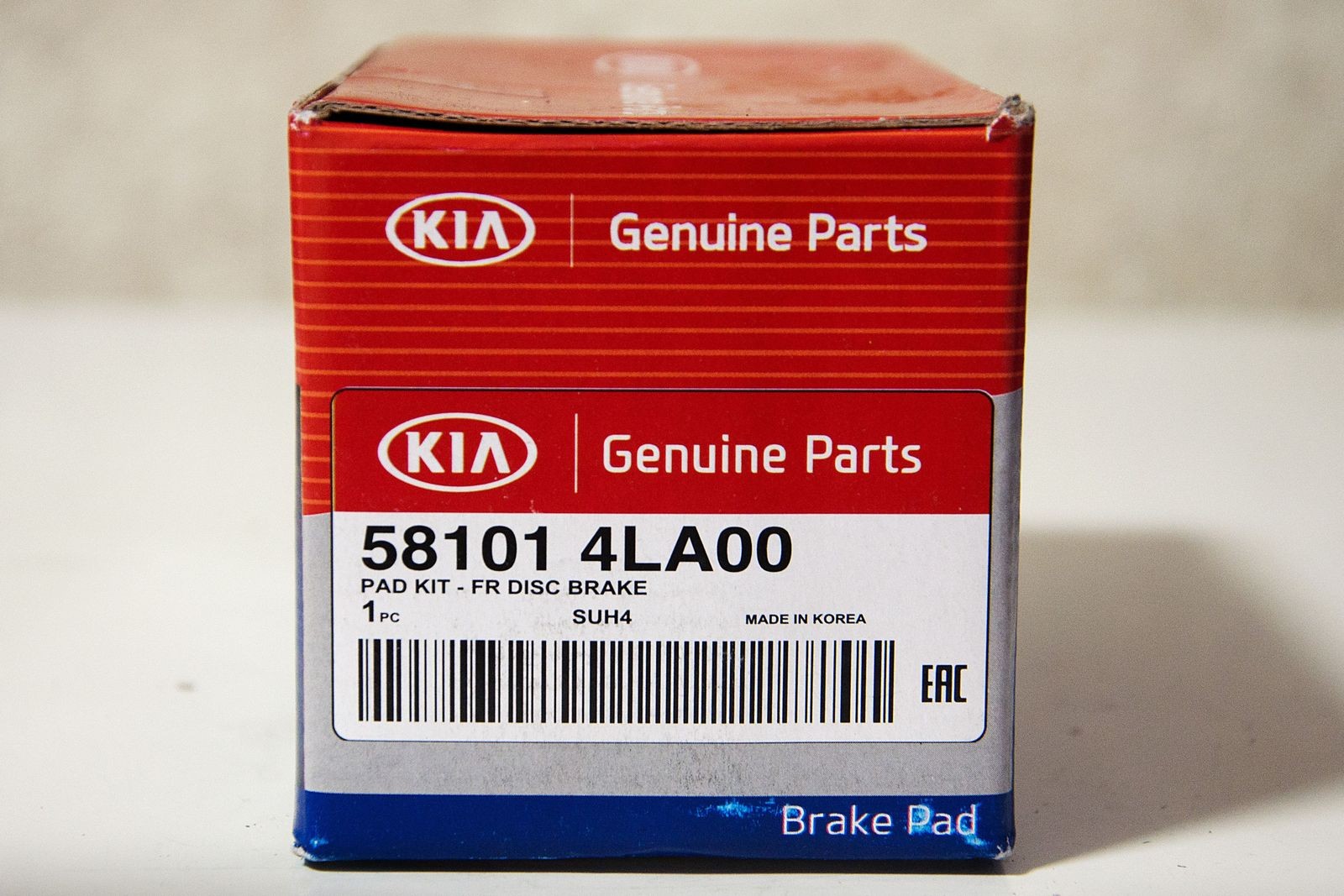

А упаковка аналога вообще точно такая же, что и предыдущая – добавить нечего.
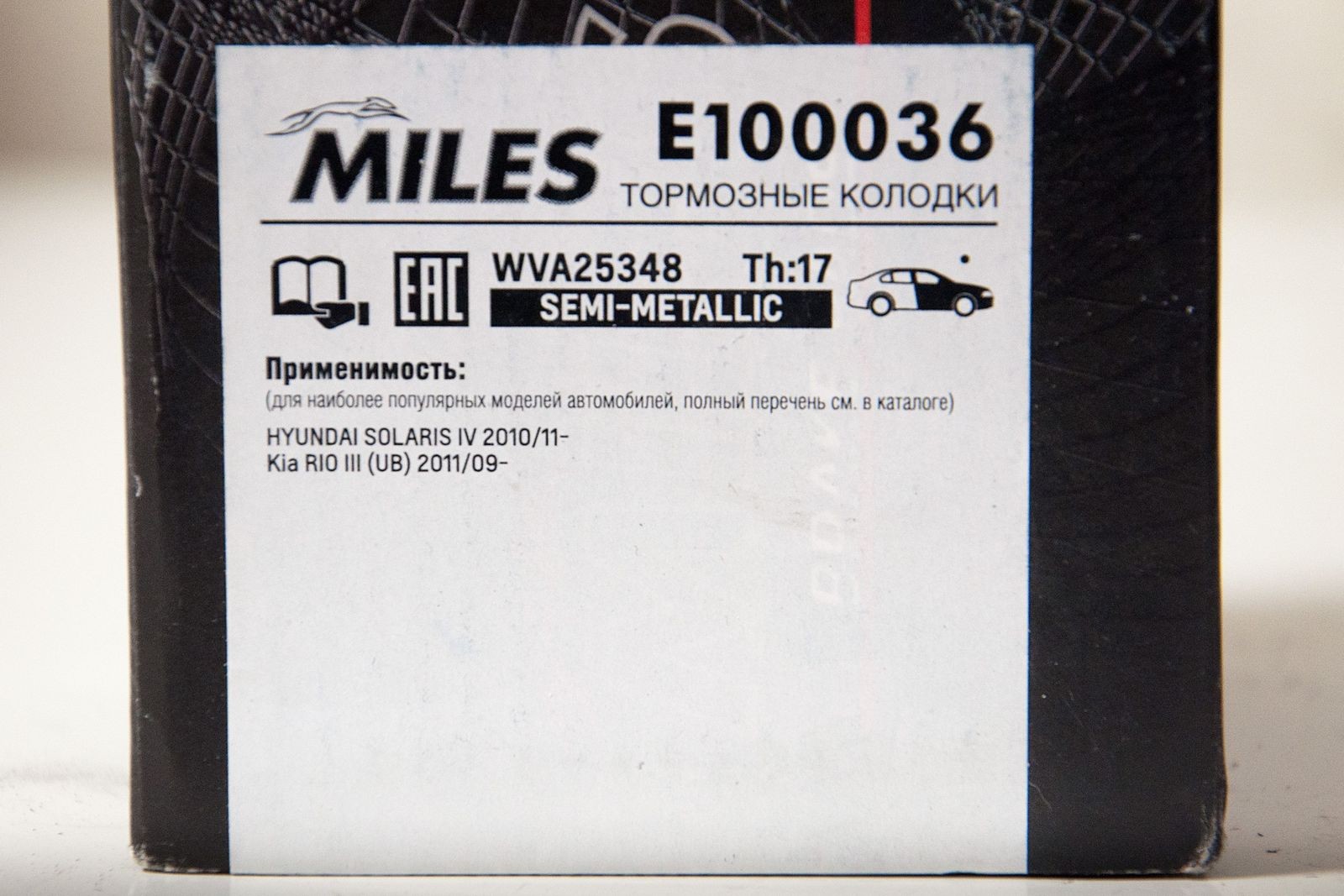
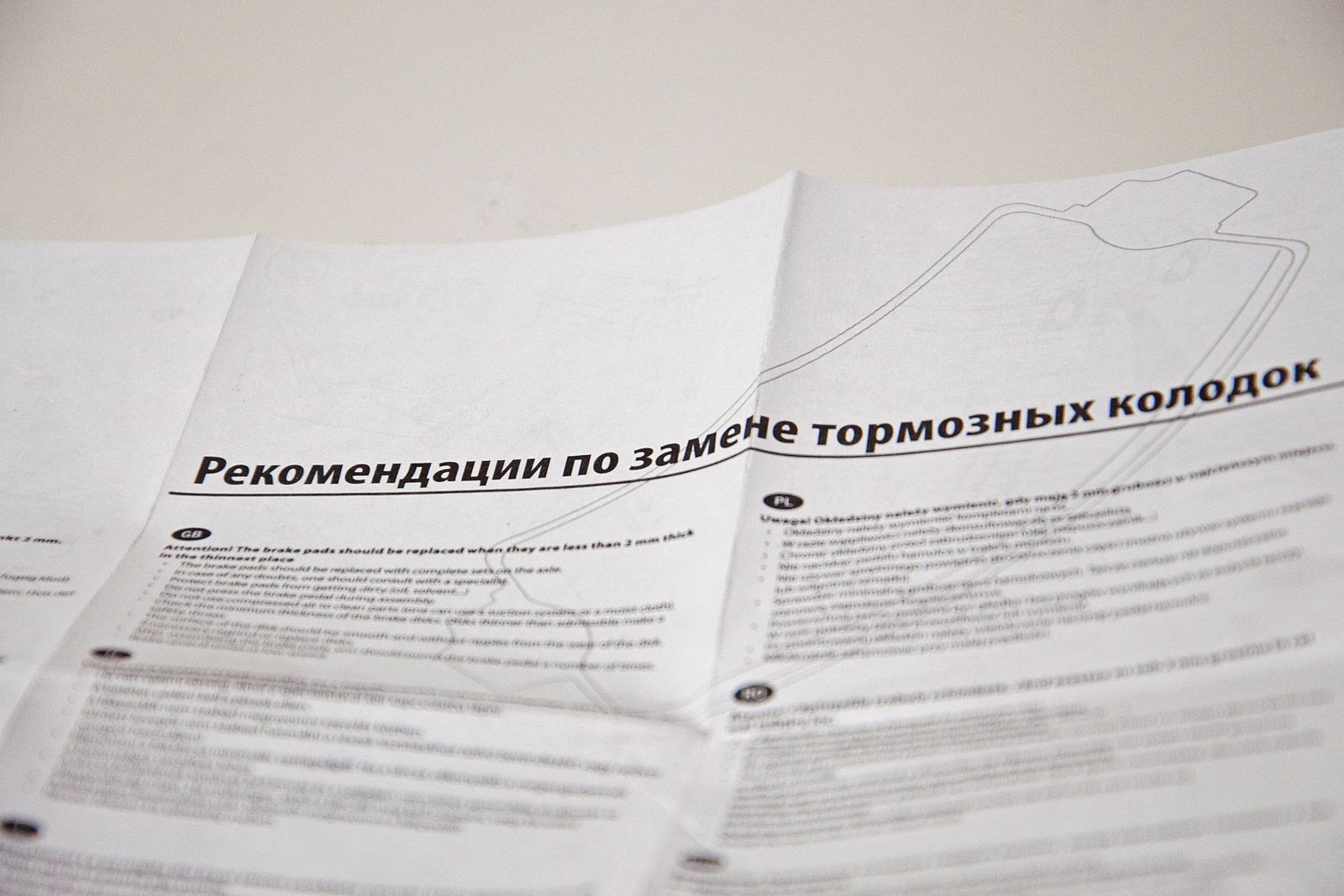
Внутри – та же классика жанра: Miles не пожалел денег на полиэтиленовую упаковку, но гораздо более нужные скобы класть в коробку не стал. У колодок Kia они есть в комплекте.
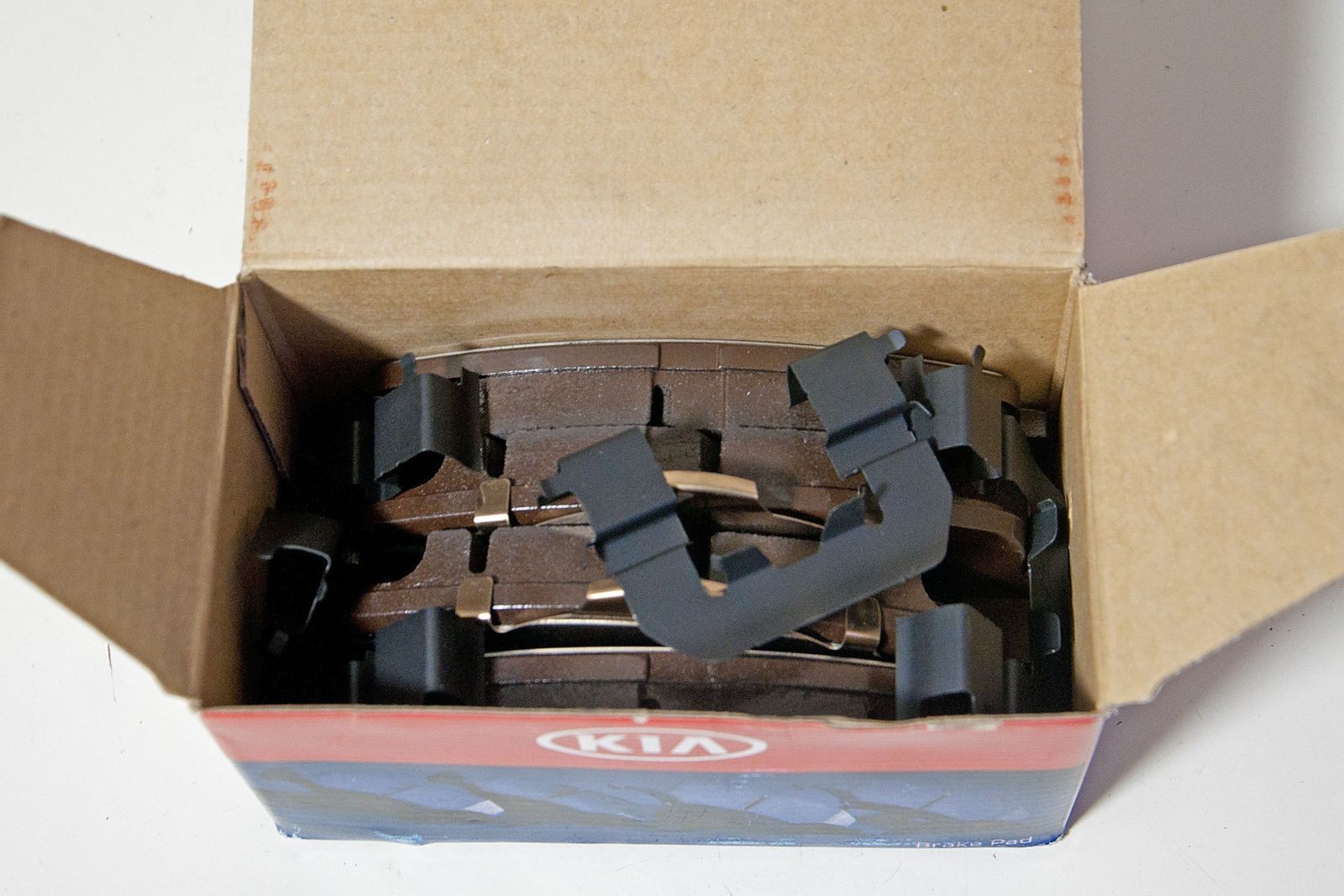
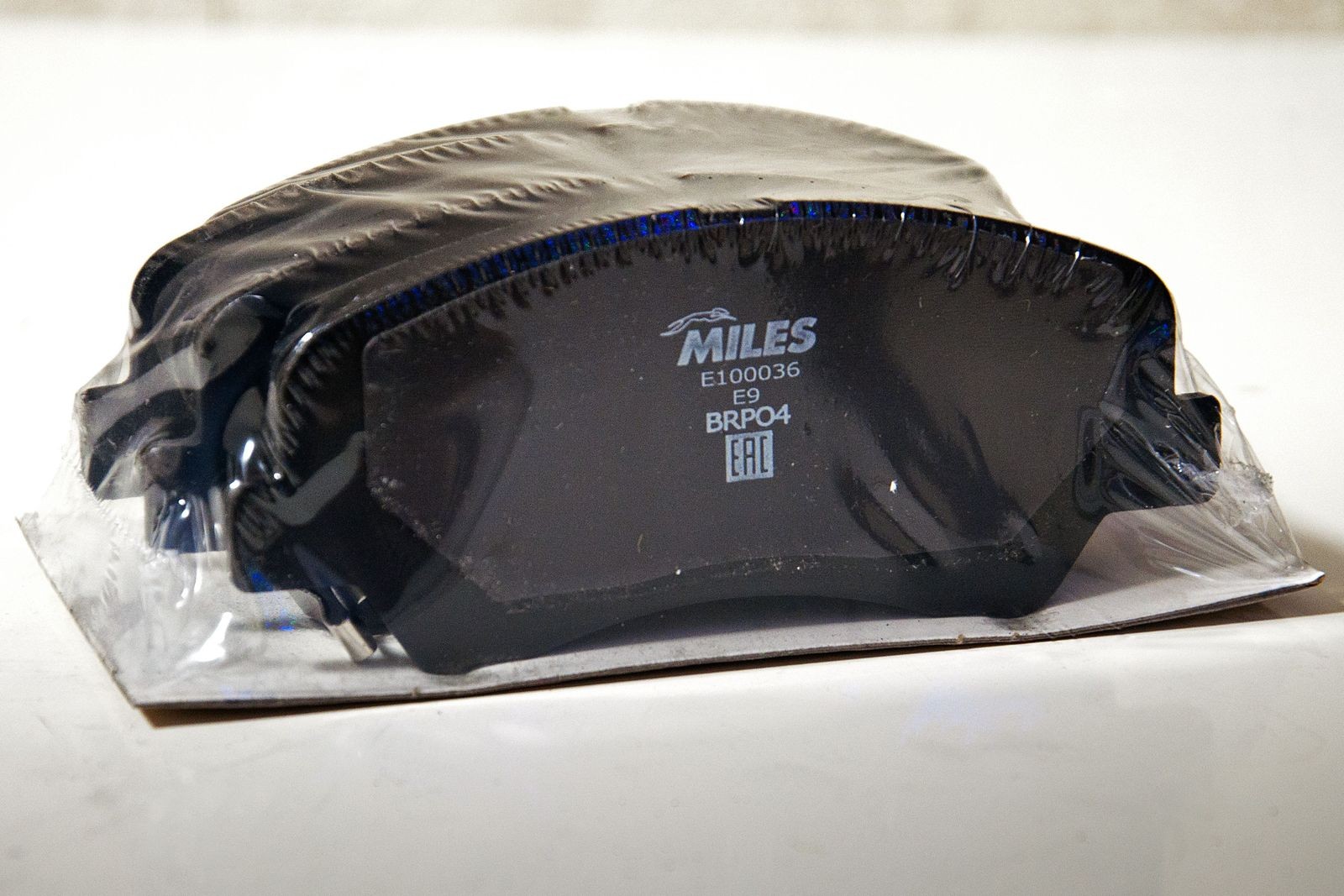
И, конечно же, аналог опять отличился небольшим разбросом в толщине колодок. Цифры получились такими. Толщина оригинала – везде 16,9 мм, накладки – 11,0 мм. Толщина аналога гуляет от 16,4 мм до 16,7 мм, зато накладка здесь «щедрая» – 11,5-11,9 мм. Правда, тоже неровная. Ну а самое интересное – это одна прорезь на накладке вместо двух, как у оригинала.

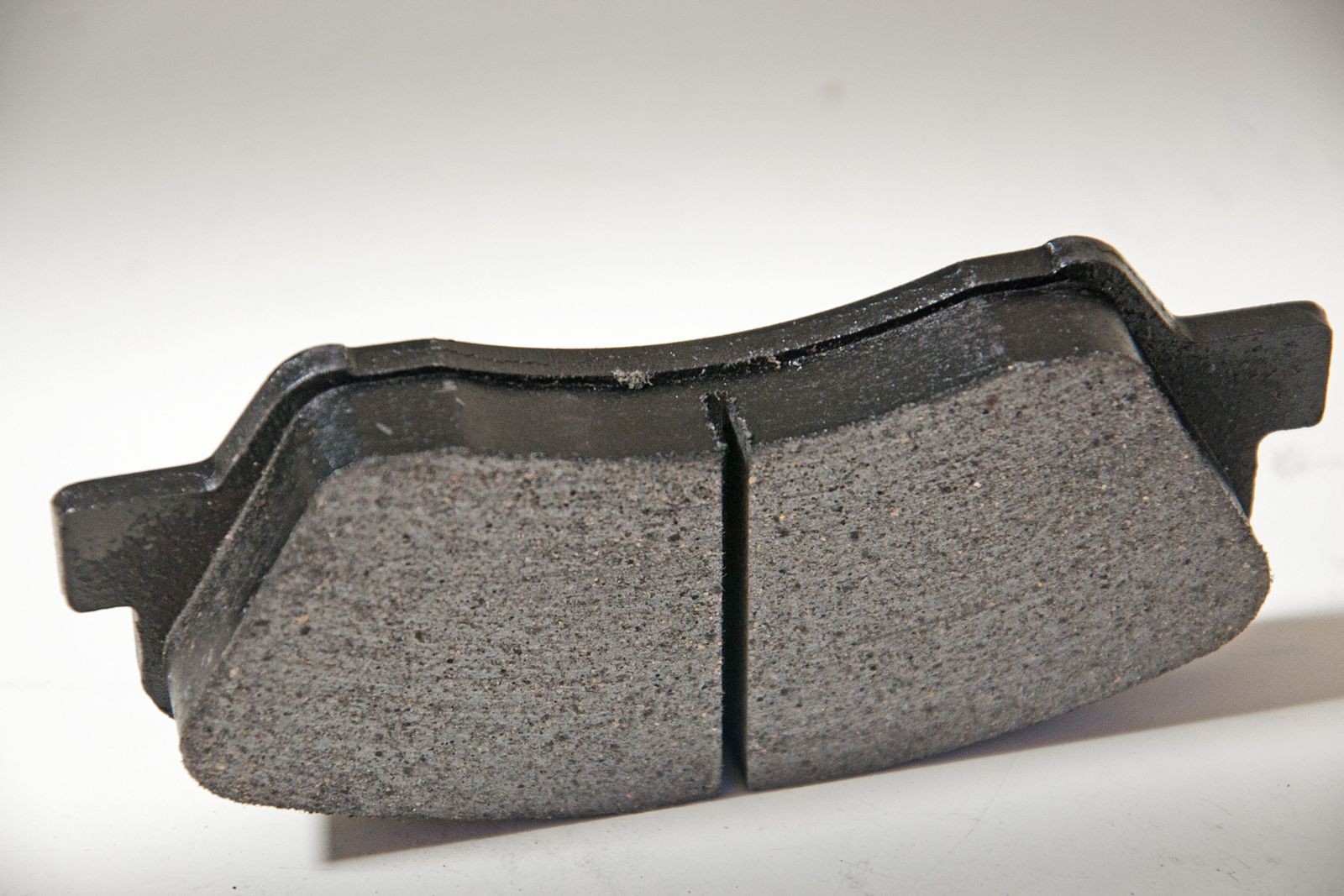
Зачем вообще нужны эти пропилы? Они выполняют две функции. Первая – это отводить от рабочих поверхностей дисков и колодок образующуюся при торможении пыль из продуктов износа. Вторая – не дать треснуть накладке при перегреве. Когда греется колодка с большой сплошной поверхностью, она нередко ломается, после чего на ней видна трещина. Пропил эту проблему решает. Почему Miles на нём решил сэкономить, непонятно. Да и тот, что всё-таки сделан, не слишком радует. Достаточно сравнить, как ровно он выглядит на оригинале, и какая бахрома видна на аналоге. Видимо, фрикционный материал аналога тут тоже не из самых качественных.
Теперь перейдём к дискам
Их у нас только два: оригинальный Hyundai-Kia с номером 517120U000 и диск Miles с номером К001254. Такие диски стоят на Hyundai Solaris и Kia Rio.
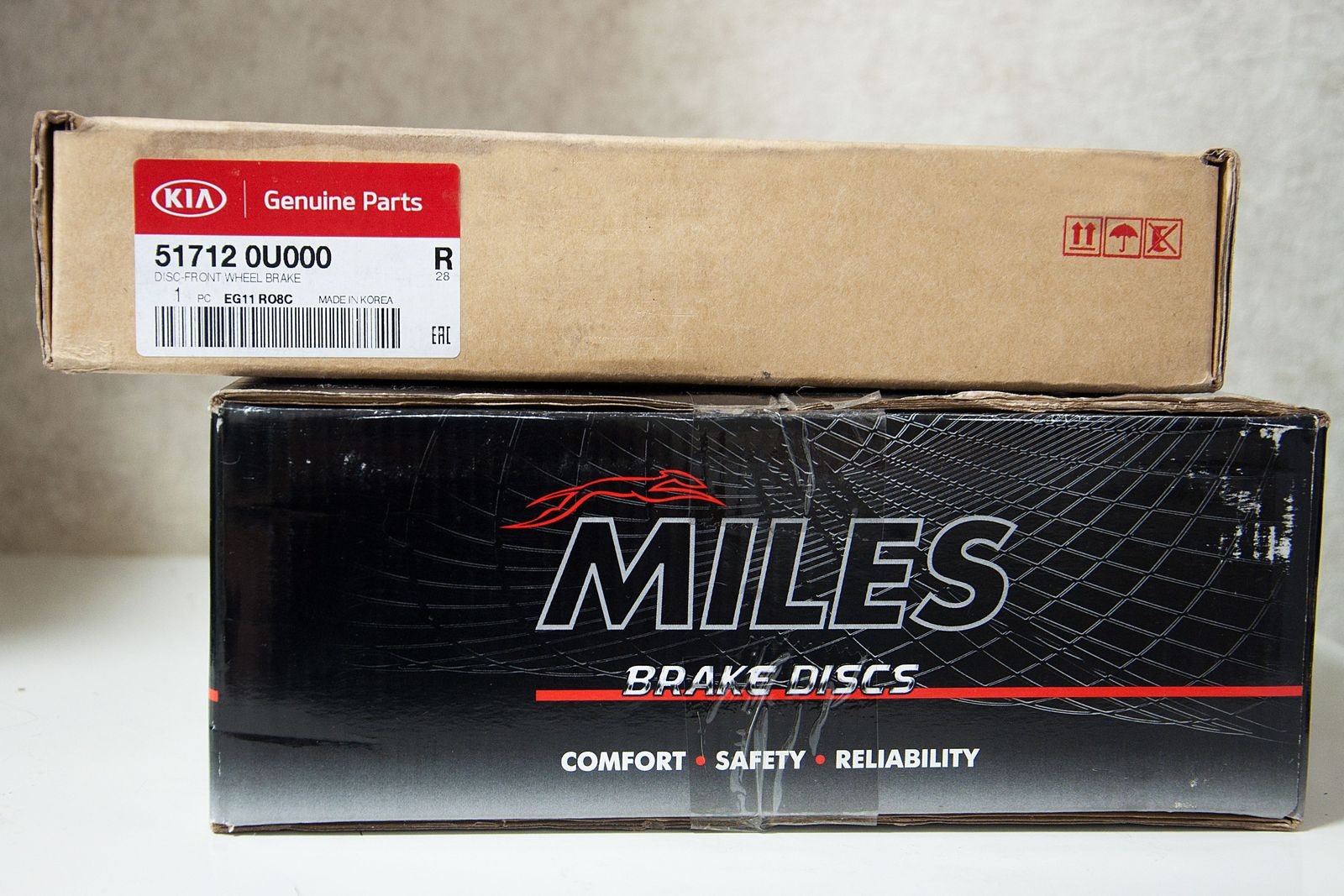
Об упаковке Miles ничего нового сказать нельзя: всё более-менее прилично и аккуратно. С Киа ситуация иная. С коробкой всё отлично: много картона, хорошо закрыто, внутри диск не болтается, все уложено компактно. Но полиграфии нет вообще никакой, есть только этикетка.

Внутри ситуация похожая: у Miles есть инструкция, у Kia её нет. Оба производителя упаковывают диски в полиэтилен и обрабатывают смазкой. Но у Miles её слишком много, поэтому пакет испачкан в масле даже снаружи. У Kia смазки в меру, а вот жёлтый полиэтилен оригинальной запчасти намного плотнее и снаружи чистый.
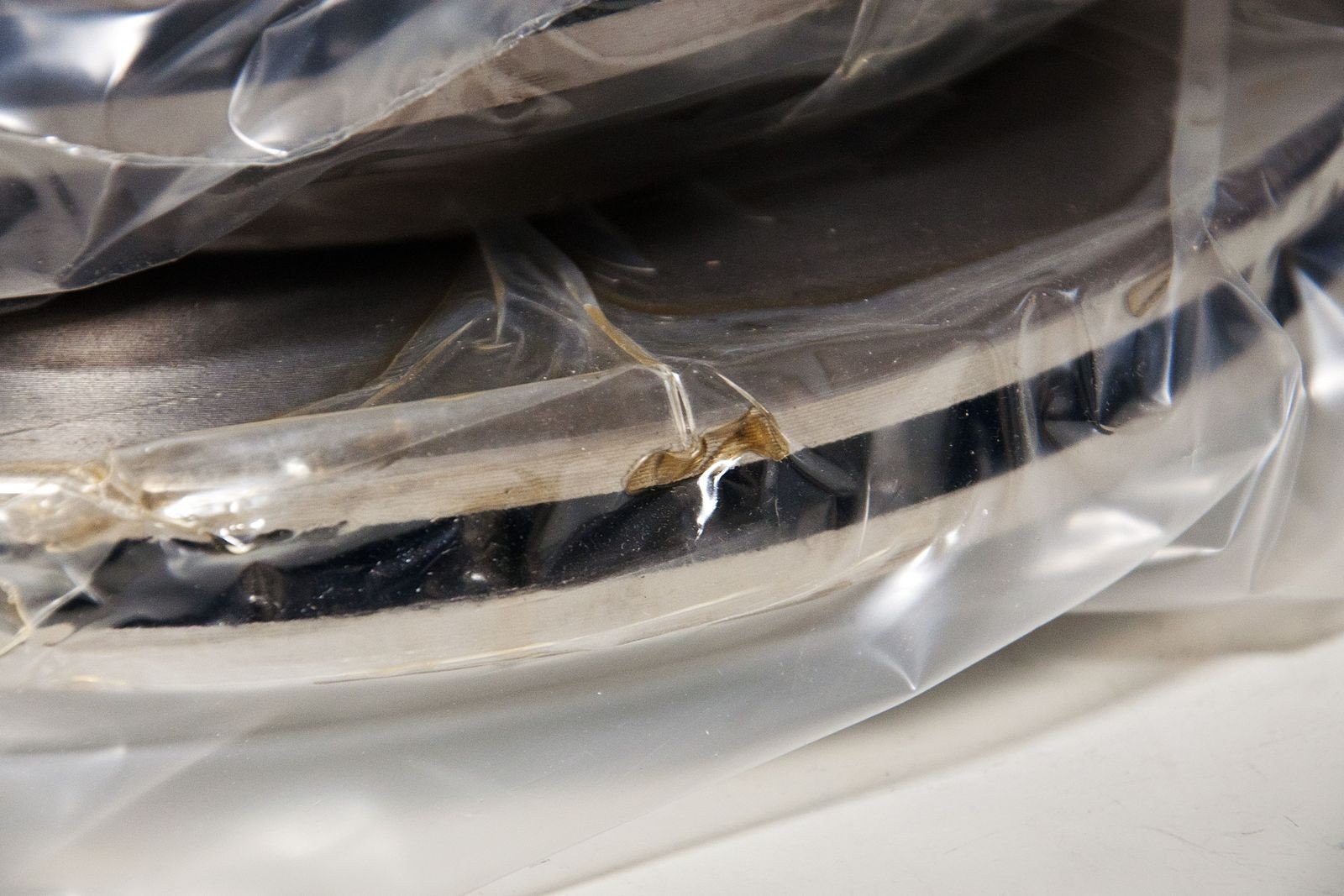
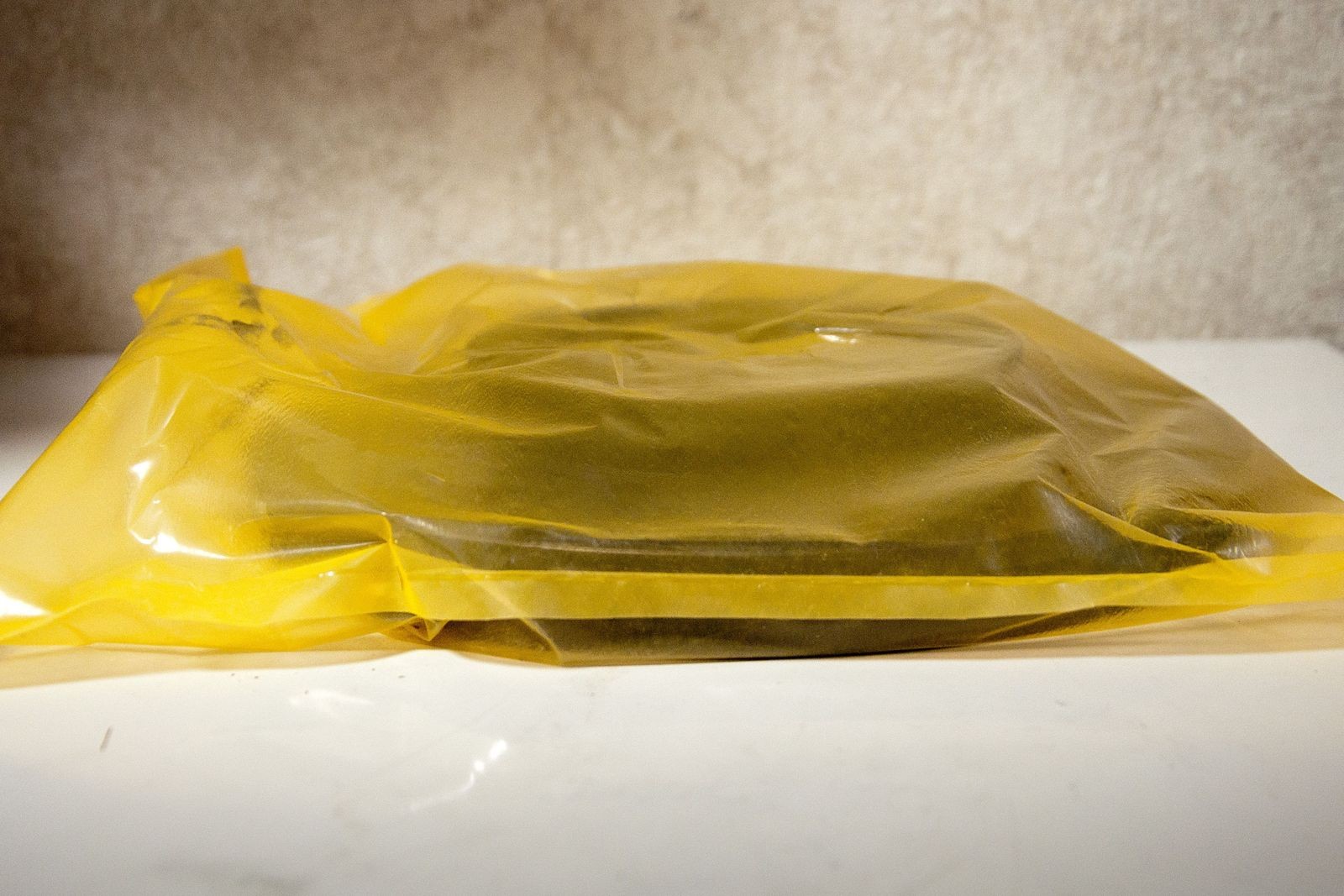
Как вы понимаете, упаковка – это далеко не так важно, как то, что лежит внутри. А вот тут как раз и начинаются сюрпризы.
Сравните, как выглядит оригинальный и неоригинальный тормозной вентилируемый диск с торца. Светлый диск – Miles, тёмный – Kia.
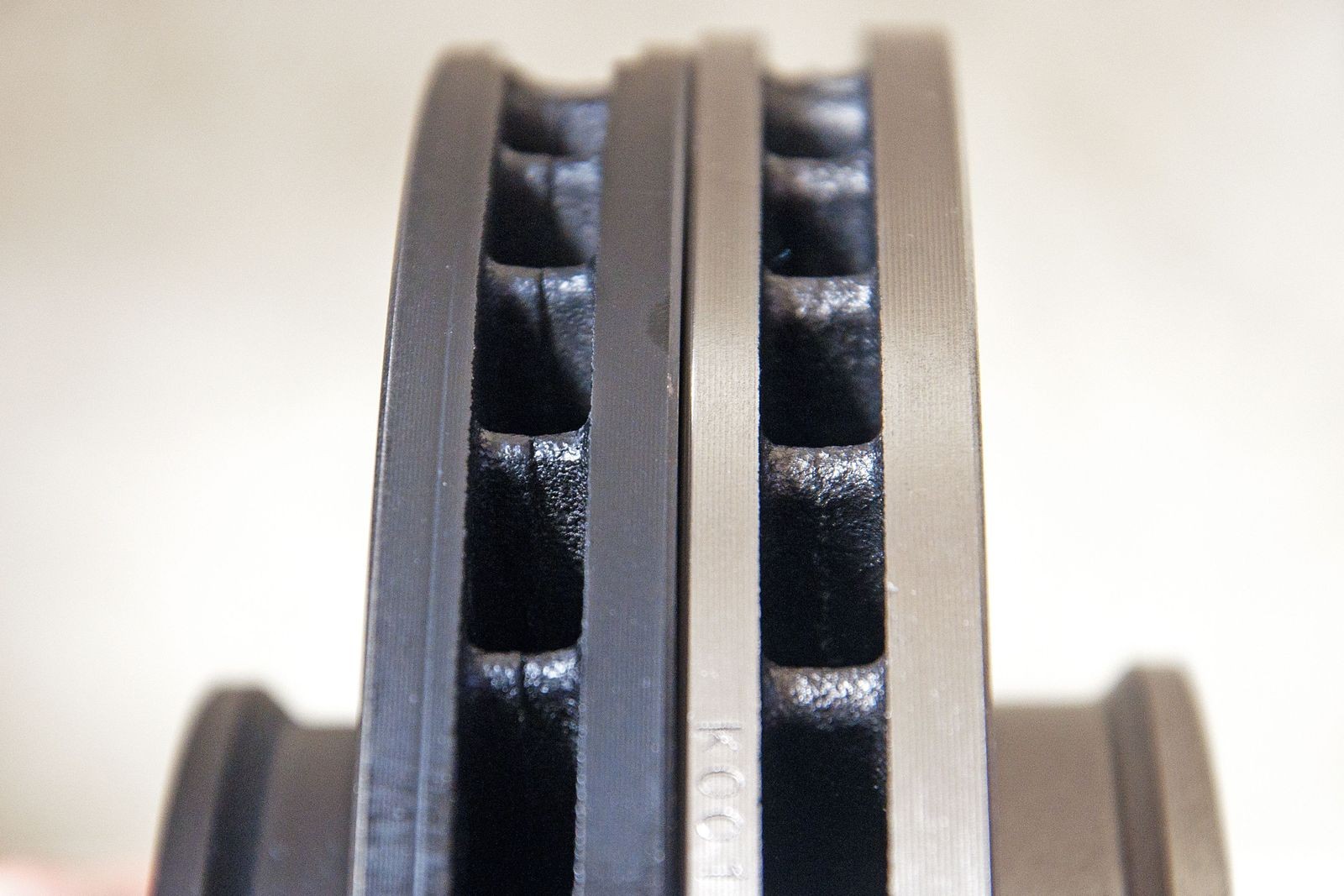
У обоих дисков часть со стороны ступицы немного толще. Но у аналога она толще заметно. Думаю, ничего плохого в этом нет, но замер штангенциркулем выявил очень интересную особенность: у аналога толщина диска в разных точках замера разная. То есть, тут в наличии та самая «особенность», что приводит к биению диска. Если толщина одной стороны оригинала составляет 6,5 мм, другой – 6,7 мм, а всего диска – 22,0 мм по всей длине окружности, то у аналога ситуация другая. Толщина одной стороны колеблется от 6,9 до 7,3 мм, толщина другой – везде 5,9 мм (как-то вообще не похоже на оригинал, да?). А толщина всего диска раскидана от 22,1 до 22,4 мм. Разброс толщины 0,3 мм – это очень много. С такими дисками можно смело ехать на проточку, и лишним это не будет. На балансировке колеса эта разница заметна почти не будет, а вот на торможении – вполне вероятно. А ещё это отразится на ресурсе колодок, а в экстренной ситуации – и на адекватности работы ABS.
Второй недостаток аналога – некачественная обработка посадочного отверстия. Оно на ощупь неровное и непохоже на отверстие диска Киа.

Если на оригинальном диске Киа фаска снята исключительно ровно, и поверхность после этого обработана, то на Miles её, похоже, выгрызали зубами.
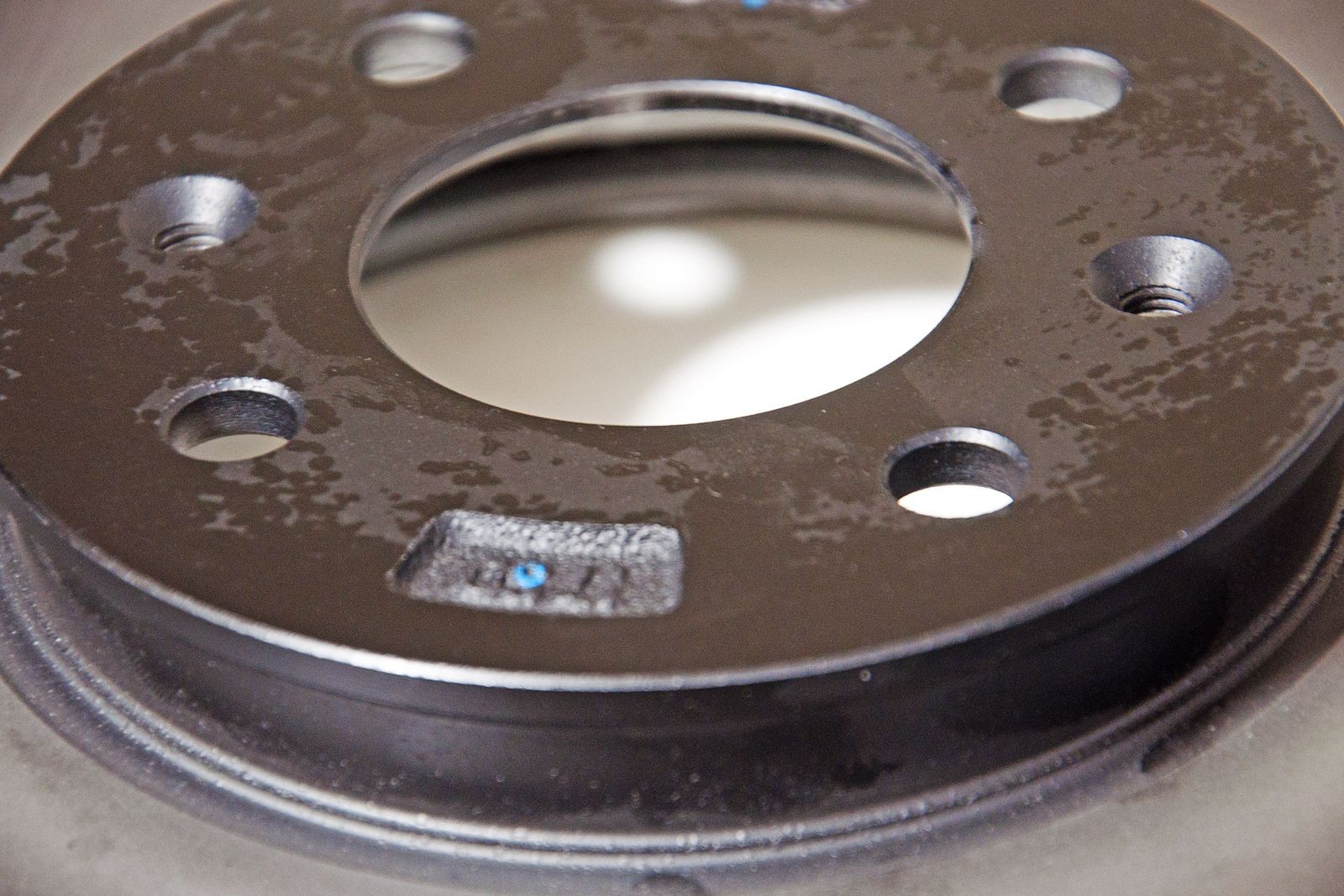
Такая небрежность в изготовлении, думаю, не помешает установке диска. Но заметное упрощение технологии на пользу диску не идёт однозначно.
* * *
Тормоза – не та система, на которой можно экономить. Тем более в случае с «корейцами», которые не были уличены в низком ресурсе тормозных механизмов. Незначительный выигрыш в стоимости этих деталей скажется на ресурсе других механизмов (например, суппортов, а в случае с кривым диском – ещё и на ресурсе ступичных подшипников). Так что не надо забывать, что скупой платит дважды, и вся эта экономия на тормозах в рассрочку когда-то потребует свои проценты. Хорошо, если деньгами.