Тормозная колодка — Википедия
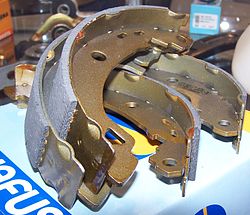
Тормозная колодка (иногда башмак) — часть тормозной системы и её основной рабочий компонент. Именно тормозная колодка создаёт тормозное ускорение, за счёт взаимодействия с поверхностью катания колеса или тормозного диска и преобразования силы нажатия в тормозной момент. Активно применяются на всех видах колесного транспорта.
Тормозной колодкой в обиходе также называют противооткатный упор, служащий для дополнительной фиксации транспортного средства при стоянке.
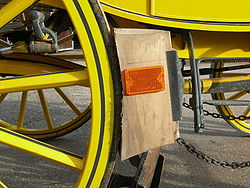
Первые тормозные колодки имели ручной привод и их применяли уже на каретах, где деревянные колодки прижимались к ободу. Впоследствии нередко ручной привод заменяли на червячную передачу.
Тормозные колодки на поездах[править | править код]
Колодочный тормоз железнодорожного состава Дисковые тормоза на некоторых локомотивах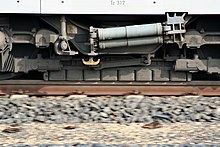
Механизм торможения карет вскоре перекочевал на только появившийся железнодорожный транспорт. На нём также тормозные колодки были поначалу деревянные, а тормозное нажатие обеспечивалось исключительно за счёт физической силы специальных работников поезда — тормозильщиков. Однако довольно скоро на смену физической силе человека пришёл сжатый воздух. Повышение нажатия на колодки привело к их повышенному износу и в этом случае дерево как материал уже не подходило. В результате стали применять тормозные колодки из чугуна, а впоследствии и из композитов.
Наиболее распространены тормоза, где колодки прижимаются к ободу колёсной пары, однако при этом, помимо износа самих колодок, происходит износ поверхности качения колёс, что ведёт к необходимости проведения дорогостоящей обточки колёс. Поэтому часто стараются применить электрическое торможение, то есть торможение тяговыми электродвигателями, при котором тормозные колодки не участвуют, что также позволяет уменьшать расход энергии за счёт рекуперации. Однако отказываться от них полностью нельзя, так как при малых скоростях электрическое торможение уже не может дать необходимого тормозного эффекта, к тому же не исключена вероятность его выхода из строя, и в этом случае ему на смену должен прийти механический тормоз с колодками. В результате иногда на железнодорожном транспорте применяют дисковые тормоза, где колодки трутся не о колёса, а о специальный тормозной диск, размещённый на оси колёсной пары. Такой тормоз применяют на высокоскоростных поездах, а также на вагонах трамвая.
Можно также отметить магниторельсовый тормоз, где тормозная колодка прижимается к рельсу, а сила нажатия образуется за счёт электромагнитного поля, создаваемого расположенными на колодке индуктивными катушками. Такой тормоз тоже распространён на высокоскоростных поездах, трамваях, а также на промышленном железнодорожном транспорте.
Тормозные колодки на автомобилях[править | править код]
Тормозные механизмы, используемые на автомобиле, делятся на два типа:
- Барабанные. В этом случае, эффект торможения происходит из-за трения элементов, являющихся неподвижными, то есть колодками с фрикционными накладками. В свою очередь, они спрятаны в тормозном барабане из чугуна и стали. Зачастую, весь этот механизм, может выполнять роль стояночного и рабочего тормоза.
- Дисковые. В этом случае, торможение происходит также за счет силы трения, но выполняется оно уже между колодками и тормозным диском, установленным между ними. Но эту систему используют только как рабочий тормоз.
Тормозные колодки на мотоциклах[править | править код]
Тормозные колодки на велосипедах[править | править код]
Велосипедные колодки сильно различаются в зависимости от конструкции тормоза.
Дисковый тормоз[править | править код]
Схож по конструкции с дисковым тормозом автомобиля или мотоцикла. Как и на мотоциклах, используются диски из чугуна или стали.
Ободной тормоз[править | править код]
Колодки прижимаются к ободу колеса. Сами колодки состоят из непосредственно прилегающей к колесу резиновой части и металлического крепления. Есть колодки со сменной резиновой вставкой. На рабочей поверхности колодки делаются насечки для отвода воды.
Барабанный тормоз[править | править код]
Тормозной механизм находится внутри втулки. При торможении цилиндрический тормозной барабан, состоящий из двух половин, раздвигается, прижимаясь к внутренней поверхности корпуса втулки.
Тормозные колодки на самолётах[править | править код]
На летательных аппаратах применяют дисковые или колодочные тормоза. На вертолётах или лёгких самолётах установлены обычные барабанные тормоза с двумя колодками, аналогично автомобильным. На более тяжёлых и скоростных самолётах используются барабанные тормоза, внутри ступицы такого колеса установлено по окружности барабана большое количество относительно небольших металлокерамических тормозных колодок, которые лежат на кольцевой герметичной резиновой тормозной камере. При поступлении в камеру воздуха или гидросмеси камера надувается, обеспечивая поджатие кольцевого набора колодок к внутренней поверхности тормозного барабана, что и вызывает торможение. В настоящее время на многих пассажирских и тяжёлых военных самолётах применяются многодисковые тормоза, выполненные по принципу мотоциклетного сцепления — внутри тормозного барабана установлен пакет чередующихся профилированных стальных или титановых дисков, с наклёпанными по окружности тормозных дисков фрикционными керамическими накладками. При сжатии пакета штоками-толкателями происходит эффективное торможение. Так как при этом выделяется большое количество тепла, то внутри тормозного барабана может устанавливается высокооборотный электромотор с крыльчаткой, нагнетающий воздух внутрь ступицы колеса.
Тормозная колодка представляет из себя металлическую пластинку, являющуюся основой, на которой закреплена фрикционная накладка. Колодка с накладкой повторяют форму поверхности, к которой они прижимаются — диска (плоскость трения прямая) или барабана (плоскость трения дугообразная). Закреплена накладка на основе заклепками или специальным клеем. Кроме того, на некоторых автомобилях предусмотрена установка в колодке датчика её износа.
В состав современной фрикционной накладки входят керамика, специальные смолы, синтетический каучук, органические и минеральные волокна, наполнители и модификаторы. Состав фрикционных материалов довольно сложен, и у каждой фирмы-изготовителя тормозных колодок он свой. Дело в том, что при торможении колодки очень сильно нагреваются, порой до тысячи градусов. При этом они должны уверенно переносить такие экстремальные температуры, не разрушаться и не терять при этом своих фрикционных свойств.
Самые главные враги тормозных колодок — перегрев, вода, масла и агрессивные жидкости (антифриз, тормозная жидкость). При недостаточной эффективности торможения или скрипе и визге тормозов, когда накладка стерта и тормозит одна металлическая основа, колодки необходимо заменить, причем меняются они только парами.
В основе работы колодочных тормозных механизмов лежит принцип преобразования энергии. В данном случае кинетическая энергия движения транспортного средства преобразуется в тепловую за счет активного трения тормозной колодки о тормозной диск, барабан или колесную пару. При торможении в тормозном приводе создается давление воздуха, тормозной жидкости или натяжение троса, которое передается на исполнительные механизмы тормозов — тормозные цилиндры или тормозной кулак. Именно эти механизмы и заставляют прижиматься тормозную колодку к диску/барабану. Чем сильнее прижим колодки, тем большая создается сила торможения. При этом, пара трения колодка-диск (или колодка-барабан) нагревается, вбирая в себя кинетическую энергию движущегося транспортного средства, и оно останавливается.
Особенности выбора тормозных колодок на автомобиль
Инфографика: замена тормозных колодок на автомобиле
Устройство тормозной системы (мотоцикл). Часть 1
Производство тормозных колодок в России
Тормозные колодки: конструкция, свойства, эксплуатация
Исправная тормозная система автомобиля — это гарантия безопасности водителя и пассажиров на дороге. С этим трудно не согласиться. Безусловно, исправность каждой детали тормозной системы имеет огромное значение. Но, пожалуй, одним из важнейших элементов тормозной системы являются тормозные колодки. Ведь именно от состояния тормозных колодок во многом зависит эффективность торможения. В процессе торможения колодки плотно прижимаются к тормозным дискам или барабанам, соединенным с колесами авто. Под воздействием силы трения скорость вращения дисков или барабанов, и соответственно колес, снижается.
Для начала, давайте разберемся, что собой представляют тормозные колодки, и какие эксплуатационные свойства колодок имеют наибольшее значение.
Тормозная колодка состоит из металлической пластины (основы) и накладки. Основу, как правило, изготавливают из стали. В качестве накладки используют фрикционный материал, то есть материал с высоким коэффициентом трения. Основные эксплуатационные характеристики тормозных колодок определяются свойствами фрикционного материала накладки. Разумеется, чем данные характеристики выше, тем качество колодки лучше.
Основой фрикционного материала является армирующий компонент, от которого зависит стабильность свойств, а также прочность тормозных колодок. Раньше в качестве армирующего компонента использовали асбест. Он способен обеспечить стабильные характеристики фрикционного материала, но представляет опасность для здоровья человека. Поэтому современные тормозные колодки не содержат асбест. А в качестве армирующего компонента фрикционных материалов используют стальные волокна, медную, латунную стружку, армирующие нити из кевлара, полимерные соединения, органические волокна и т.д. Отличными эксплуатационными свойствами обладают фрикционные материалы, в состав которых входит керамика. Тормозные колодки с накладками из таких материалов называют керамическими.
Кроме армирующего компонента, в состав фрикционного материала тормозных колодок также могут входить специальные наполнители, различные модификаторы, смолы и другие составляющие. Но чаще всего производители держат в секрете состав материала, из которого они изготавливают накладки для тормозных колодок.
Одной из главных характеристик тормозной колодки является коэффициент трения и его стабильность при различных температурных режимах. Для изготовления неоригинальных тормозных колодок, предназначенных для условий обычного дорожного движения, используют накладки из фрикционного материала с коэффициентом трения 0,25 – 0,35. Коэффициент трения оригинальных колодок находится в диапазоне от 0,35 до 0,5. Применение колодок с довольно низкими коэффициентами трения, как правило, продлевает тормозной путь, соответственно снижая уровень безопасности. При интенсивном торможении коэффициент трения колодок может снижаться вследствие повышения рабочей температуры, поэтому для восстановления нормальных показателей колодке необходимо остыть. Но не стоит думать, что слишком высокие фрикционные свойства будут гарантировать высокую эффективность торможения. В таком случае сильное давление на педаль тормоза может быстро привести к блокировке колес, и автомобиль станет неуправляемым.
При эксплуатации тормозные колодки могут нагреваться до очень высоких температур. Поэтому еще одним важным свойством колодок является термостойкость. Обычно на машины, используемые для передвижения (включая быструю езду) по городским дорогам, устанавливают тормозные колодки, способные выдержать рабочие температуры до 300 °C – 350 °C. Спортивные тормозные колодки, предназначенные для гоночных авто, способны работать при диапазоне рабочих температур до 800 °C – 900 °C. Но для ежедневной эксплуатации в городских условиях такие колодки не подходят, так как не успевают прогреться (их прогрев наступает при 100 °C – 200 °C) и торможение будет неэффективным. Именно поэтому устанавливать спортивные тормозные колодки на обычные машины не имеет смысла.
Высокие рабочие температуры тормозных колодок могут привести к нагреву других элементов тормозной системы, включая тормозную жидкость. Известно, что закипание тормозной жидкости существенно снижает эффективность работы тормозов, и даже приводит к полному их отказу. Для предотвращения такой ситуации между металлической пластиной и фрикционной накладкой в тормозной колодке часто устанавливается специальная прослойка. По сути, она играет роль некоего теплового барьера между нагретой поверхностью колодки и другими элементами тормозной системы, в частности тормозного суппорта и жидкости.
Таким образом, из всего сказанного выше можно сделать вывод, что качественные тормозные колодки должны изготавливаться из экологически чистых материалов и обладать:
- стабильным коэффициентом трения при перепадах температуры и изменении скорости вращения тормозного диска;
- стойкостью к высоким температурам;
- высокой прочностью и износостойкостью;
- способностью поглощать тепло нагретой поверхности фрикционного материала;
- отличной демпфирующей способностью и способностью предотвращать шум для обеспечения комфортного торможения.
Для тормозов дискового и барабанного типа используют соответственно дисковые и барабанные тормозные колодки. Дисковые колодки имеют более стабильные характеристики, чем колодки барабанного типа.
Со временем тормозные колодки изнашиваются и подлежат замене. Об износе тормозных колодок может свидетельствовать чрезмерный шум (скрип, писк) при торможении, слишком слабые или наоборот очень резкие тормоза, а также пыль на дисках с примесью металлической стружки. Чтобы предупредить водителя об износе колодок и необходимости их замены, на них устанавливаются специальные датчики износа. Они бывают механические и электронные. При использовании механического датчика изношенная колодка будет издавать резкий и очень неприятный скрип. Во втором случае водитель узнает об износе тормозной колодки благодаря подсвеченному индикатору на панели приборов.
Разумеется, что для каждого авто имеются свои рекомендации по срокам замены тормозных колодок. В среднем ресурс колодок составляет от 8 до 12 тыс. км пробега. Но скорость износа данного элемента тормозной системы зависит от различных факторов, например от качества колодок, стиля вождения, условий эксплуатации и т.д. Интересен тот факт, что передние тормозные колодки всегда подвержены большему износу, чем задние. Связано это с тем, что именно передние колодки испытывают основную нагрузку. Задние тормозные колодки, как правило, служат примерно в три раза дольше.
Не забывайте, что заменять тормозные колодки необходимо сразу на обоих передних или задних колесах. В противном случае, изношенная колодка с одной стороны и новая с другой будут тормозить колеса с разной эффективностью. А это неизбежно приведет к потере управляемости авто.
После замены новые тормозные колодки должны «притереться». В период притирки, примерно первых 300 км (но для каждого авто разные показатели), эффективность торможения может быть снижена, а сами колодки могут скрипеть. Поэтому водителю нужно быть предельно осторожным при торможении.
Купить тормозные колодки сегодня не составит труда. Найти их можно в любом магазине автозапчастей, включая интернет-магазины. Выбирая тормозные колодки для вашего авто, следуйте рекомендациям производителя, указанным в технической документации. Учтите, разные колодки предназначены для разных нагрузок. Поэтому перед покупкой лучше лишний раз убедиться, что колодки действительно подойдут для вашей машины. Помните, только качественные и правильно подобранные тормозные колодки обеспечат эффективное торможение и минимальный тормозной путь при любых климатических условиях. Более того, они позволят сохранить отличное состояние тормозных дисков и барабанов на протяжении длительного срока эксплуатации. Использование колодок низкого качества наоборот ускорит износ других элементов тормозной системы.
Обратите внимание, что на новых высококачественных тормозных колодках обязательно присутствует маркировка, соответствующая европейскому (ECE R90) или американскому (SAE) стандарту качества. Более того, поверхность новых колодок должна быть ровной, без повреждений и сколов. Фрикционные накладки не должны содержать глубоких трещин и отделяться от стальных пластин.
На современном рынке автозапчастей представлен широкий ассортимент тормозных колодок различных торговых марок. Купить тормозные колодки от ведущих производителей можно и в Хмельницком. В настоящее время на полках магазинов автозапчастей можно найти как оригинальные тормозные колодки, так и более дешевые аналоги. Как правило, часть колодок ОЕ качества, отвечающие всем требованиям производителей автомобилей, попадает в свободную продажу, но покупка оригиналов потребует больших финансовых затрат. Тормозные колодки, изначально предназначенные для вторичного рынка автозапчастей, стоят на 30 – 70 % дешевле оригиналов, и часто не уступают им по качеству. В продаже также можно встретить бюджетные тормозные колодки низкого качества по невысоким ценам.
Типы тормозных колодок
Администратор
2212
Данная статья является переводом статьи с ресурса http://www.auto-repair-help.com.
ТОРМОЗНЫЕ КОЛОДКИ
Автор: Джим Миллер
Тормозные колодки используются для контакта и давления на тормозной ротор (диск), чтобы создать трение, необходимое для остановки движущегося транспортного средства. Тормозные колодки состоят из металлической основы (подошвы) с фрикционным материалом, скрепленным или склепанным к металлической основе. Для барабанных тормозов используется гораздо более плотный фрикционный материал, чем Материал основы. Это обеспечивает тормозную колодку большей влагостойкостью. Тормозные колодки могут быть оборудованы индикатором износа. Это, как правило, металлическая вставка, которая будет контактировать с поверхностью тормозного диска, когда тормозная накладка изношена до минимальной толщины. Когда индикатор износа контактирует с тормозным диском, он издает громкий шум (визг, писк), который, обычно уменьшается, когда вы отпускаете педаль тормоза. Этот шум может быть более заметен в поворотах, т.к. тормозной диск оказывает воздействие на индикатор износа, ввиду действия различных сил, возникающих при повороте. Если это происходит, немедленно проверьте тормозные накладки на износ (или обратитесь к местному механику), так как это может помочь предотвратить дорогостоящее повреждение тормозных компонентов от износа тормозных накладок.
Большинство коммерческих тормозных колодок, установленных в авторемонтных цехах, изготавливаются с учетом нормальных, «рутинных» характеристик вождения (т.е. обычная езда по городу). Поэтому такие «ежедневные» тормозные колодки обычно жертвуют более высокими конечными показателями, чтобы обеспечить более длительный срок службы. Хотя такие тормозные колодки, как правило, приемлемы для повседневного автомобилиста, они могут иметь опасные последствия при использовании на транспортных средствах высокой мощности (или тяжелые), которые выдерживают тяжелые условия эксплуатации. Я полагаю, что любой водитель, который ищет тормозные площадки высокой эффективности (продемонстрировать свой высокоэффективный стиль вождения), рассматривает некоторые из следующих типов/брендов тормозных колодок. Большинство из них могут быть установлены в специализированных авторемонтных мастерских (тюнинг ателье).
КЕРАМИЧЕСКИЕ ТОРМОЗНЫЕ КОЛОДКИ
По сравнению с органическими (из углеродных материалов) тормозными колодками, керамические тормозные колодки, как правило, тише и испускают меньше пыли. Большинство керамических составов имеют очень низкие характеристики пылеобразования, таким образом предотвращая от аккумулирования пыли на ваших колесах. С тех пор, как они были впервые использованы в 1985 году, материалы, содержащие керамические составы были широко признаны за их превосходную комбинацию черт. Вместо полуметаллических стальных волокон, керамические тормозные колодки используют керамические соединения и медные волокна. Это позволяет керамическим тормозным колодкам переносить высокие температуры остановки с минимальным тепловыделением, обеспечить быстрое восстановление после остановки, и генерировать гораздо меньше пыли и износа на тормозных колодках и дисках. Также соединения в керамических тормозные колодках сделали торможение намного тише. Это происходит потому, что керамические соединения помогают ослабить шум, генерируя частоту, которая выходит за пределы диапазона человеческого слуха. Керамические тормозные колодки соотвествуют или превосходят OEM стандарты срока эксплуатации, дистанции остановки (тормозного расстояния, пути) и шума. По данным большинства испытаний на долговечность керамические соединения увеличивают срок службы тормозов по сравнению с большинством других типов составов, металлических и органических материалов и служат дольше других высококачественных материалов со значительным запасом, без жертв в виде шума, срока службы самих колодок и тормозных характеристик.
КЕВЛАРОВЫЕ ТОРМОЗНЫЕ КОЛОДКИ ROTEX
Лучшие кевлар-металлические колодки это тормозные колодки Ротекс, о чем будут свидетельствовать многие автомобильные механики. Rotex колодки предлагают превосходную способность останавливать. Фрикционное вещество в колодках Rotex имеет кевлар и металлическую стальную проволоку (+ губка железа для максимальной теплопередачи), а также серебряный графит для тихой работы. 60% содержание металлической смеси уменьшает вибрацию, которая вызывает визг. Тормозные колодоки Ротекс идеально подходят для перфарированных дисков. Эти тормозные колодки тоже, вероятно, с самым низкой пылеобразованием на рынке. Это связано с кевларовым склеивающим материалом, используемым при их производстве. Rotex колодки, в среднем, служат на 30% дольше, чем органические тормозные колодки. Металлическое наполнение в Rotex гарантирует, что автомобиль остановится быстро, несмотря на то, что сделаны для города, чтобы не быть абразивом для дисков. Rotex были впервые сделан для автомобилей, таких как Mercedes-Benz и BMW, чтобы обеспечить тормозную колодку с превосходной тормозной силой, но без всей пыли, что испускают органические колодки.
ТОРМОЗНЫЕ КОЛОДКИ ИЗ УГЛЕРОДИСТОГО ЖЕЛЕЗА HAWK
Тормозные колодки Hawk славятся отличной тормозной способностью. Тормозные колодки Хоук сделаны из мягкого материала Ferro Carbon (углеродистое железо) и обеспечивают высокий коэффициент трения. Хоук делают смеси которые превосходны для агрессивных водителей или водителей у которых есть тяжелый грузовик или SUV. Состав HPS Hawk популярен во многом из-за его противоизносной формулы, в сочетании с низким уровнем пыления смеси. Тормозные колодки Hawk Performance HPS Road предназначены для купе, спортивных автомобилей, седанов, Грузовиков и внедорожников, использующихся для высокоскоростного вождения. Производительность колодок Хоук HPS железо-углеродного соединения будет обеспечивать дополнительные характеристики торможения для повышения вашего опыта вождения. Этот уникальный продукт сочетает в себе безопасность и качество аэрокосмической техники с тормозными технологиями автоспорта. Тормозные колодки HPS производства HAWK предлагают по крайней мере 20% больше тормозного усилия в купе с более высоким сопротивлением к износу, чем многие OEM (неоригинальные) тормозные колодки или стандартные заводские заменители.
Перевод подготовлен командой мастерской Works Garage специально для ресурса beworks.ru.

передние и задние, из чего делают, состав и виды колодок
3611 ПросмотровКаждый современный автомобиль имеет тормозную систему. Такая система нужна для того, чтобы дать возможность водителю остановить машину в нужный момент. Эта система состоит из нескольких агрегатов, которые по-своему очень важны и выполняют определенную функцию.
В эту систему входят передние и задние тормозные диски, суппорты, остановочные цилиндры и колодки. Именно об устройстве тормозных колодок речь и пойдет. Дело в том, что остановочные башмаки считаются наиболее частым заменяемым устройством в системе. Происходит это по причине того, что при соприкосновении с тормозным диском из-за силы трения тормозные колодки нагреваются и быстро изнашиваются.

История
Первые тормозные колодки были из дерева и соприкасались с тормозными дисками посредством специальных рычагов. Такие тормозные колодки устанавливались еще на конные повозки. Следует учесть тот факт, что в какое-то время такие тормозные системы не пользовались большим спросом, а происходило это в то время, когда производители автомобилей ставили на свои автомобили двигатели, не обладающие большой мощностью. Поэтому машины имели небольшой вес и не требовали хороших тормозов.
Конечно же, прогресс не стоит на месте, и с каждым днем производятся все более мощные двигатели, поэтому и модернизации подвергаются тормозные системы, и остановочные башмаки. В то время, когда дисковые тормоза были непопулярны, автомобили останавливались с помощью барабанных тормозов.
Функции
Передние и задние тормозные колодки состоят из двух основных частей, это основная и фрикционная часть. Фрикционная часть соприкасается с поверхностью тормозного диска, поэтому и быстро изнашивается. В последнее время производители часто разрабатывают что-то новое для того, чтобы увеличить срок эксплуатации тормозных колодок.
Основной функцией, которую обязаны выполнять тормозные колодки, является замедление или остановка тормозного диска. Для того, чтобы справляться с этой задачей, в состав, из которого делаются передние тормозные колодки, входит много компонентов. Каждый производитель имеет свой определенный состав. Раньше производители в состав добавляли асбест. В состав он входил до тех пор, пока не выявили вредные свойства этого вещества.
Сегодня производители для того, чтобы скрепить фрикционные частицы, используют специальные составы, в основу которых входят органические вещества. Стоит учесть тот факт, что некоторые производители до сих пор в состав добавляют асбест, потому что он дешевле, чем органические вещества.
Для того, чтобы признать асбест вредным веществом, врачи производили специальные экспертизы, в ходе которых было выявлено что это вещество сильно влияет на здоровье водителя, пассажиров и пешеходов, которые движутся вдоль дороги или по пешеходному переходу. Вредны именно пары, которые выделяются из-за нагревания.
Разновидности
Сегодня существует два вида передних и задних тормозных колодок, отличаются они лишь тем, из чего их делают. Есть асбестовые тормозные колодки и без асбеста. Различие их лишь в том, чтобы скрепить фрикционные элементы, в состав добавляется либо асбест, либо органические вещества.
Первый вид колодок рекомендуется заменять только в респираторе и очках для того, чтобы сохранить зрение. Не смотря на то, что это вещество такое вредное производители все равно делают изделия из него. Ведь асбест намного дешевле, чем органические вещества, в конце это отражается и на цене. Более того эти изделия покупают водители, даже не задумываясь о последствиях.
Второй вид подразумевает, что для того, чтобы закрепить все фрикционные элементы, используется металлическая стружка из мягких металлов. Они значительно дороже, чем первый тип. Обуславливается это тем, что они более термостойкие и меньше подвергаются износу. Также во время использования металлов в составе снижается шум при торможении, что является неоспоримым преимуществом.
Во время покупки колодок в магазине на коробке будет специальная маркировка, прочитав которую можно определить, из чего изготовлено изделие, и на какие условия оно рассчитано. Устройство любых тормозных колодок схоже по своей конструкции и составу.
Из маркировки можно узнать примерные сроки замены и правильные размеры тормозных колодок, при которых они могут эксплуатироваться.

Замена
Несмотря на то, что они бывают с большим сроком годности, он все равно подходит к концу, и требуется замена колодок. Чаще всего в негодность приходят передние остановочные башмаки. Происходит это потому, что при нажатии на простой тормоз именно передние тормозные колодки останавливают автомобиль.
Для того, чтобы определить, когда колодки пришли в негодность, не требуется быть механиком со стажем. Для этого следует всего лишь следить за поведением автомобиля во время торможения. Если в момент нажатия педали тормоза сначала ничего не происходит, лишь спустя время машина начинает тормозить, то это признак того, что колодки стерлись, и для того, чтобы соприкоснуться с диском, им нужно больше времени.
Помимо этого, можно узнать сроки замены, исходя из информации маркировки, которую можно найти на корпусе. Чтобы выбрать правильные колодки, нужно знать вес и устройство своего автомобиля. Это нужно, чтобы выбрать нужную температуру, при которой они могут оставаться работоспособными. Дело в том, что из-за веса машины напрямую зависит время соприкосновения.
После того, как была произведена замена, следует смазать все необходимые агрегаты устройства специальной смазкой, чтобы не было постороннего скрипа из подвески.
- Во-первых, нужно смазать направляющие колодок.
- Во-вторых, нужно смазать направляющие суппортов. Смазку для направляющих следует выбирать исходя из материалов, из которых изготовлены направляющие.
Чаще всего на корпусе направляющей есть маркировка, на которой можно посмотреть какая смазка потребуется для смазки именно этого устройства.
После того как будут правильно смазаны все направляющие устройства, скрипов в области подвески не должно быть.

Резюме
Сегодня автомобиль есть практически у каждого жителя. Около половины водителей знает устройство своего автомобиля и сможет починить его в случае поломки. Помимо этого, многие знают вес своей машины, исходя из которого, они могут подбирать запчасти, рассчитанные на определенный вес.
В устройстве машины существует много элементов, которые нужно устанавливать, именно исходя из веса машины. К таким устройствам относятся амортизаторы, пружины и другие элементы подвески.
Также вес нужно учитывать, когда выбираете задние или передние тормозные колодки. Выбрав задние или передние тормозные колодки, их нужно правильно установить на автомобиль для правильной работы.
Полезные и спорные: тормозные колодки из асбеста
И все благодаря асбесту – минералу, который используется более чем в трех тысячах различных изделий, охватывающих множество сфер деятельности человека – от строительных материалов до специальных систем защиты от напалма.
Тормозной путь
Использовать асбестовое волокно в качестве основы для производства тормозных накладок начали в первой половине XX века – на заре массового автомобилестроения. В самом деле, асбест идеально подходит для этих целей: слабо подвержен механическому воздействию, не плавится и не источает вредных паров, а его прочность при растяжении вдоль волокон — до 30000 кгс/кв.см, что превышает показатели стали. Более того, асбестовые тормозные колодки не теряют эффективности и при жаре, и в лютый холод, и в любую влажность. В СССР, а затем и в России тормозные колодки из асбеста используются в железнодорожных составах, грузовых автомобилях, вездеходах и многих других видах специализированной техники. Казалось бы, такой уникальный минерал, у которого нет аналогов в природе, должен применяться повсеместно, но вот уже несколько десятилетий вопрос о его применении остается спорным.
Наука за хризотил-асбест
Можно ли безопасно использовать асбест? Изучением этого вопроса в течение десятилетий занимаются исследовательские группы со всего мира. Согласно результатам большинства из них – можно при соблюдении нескольких параметров. Во-первых, важна форма добываемого минерала. Сегодня весь добываемый в гражданских целях асбест относится к хризотиловой группе, другие формы запрещены. В частности, в исследовании Давида М. Бернштейна, Рика Роджерса и Пола Смита «Биоперсистенция волокон хризотила» указано, что из-за своей малой длинны (5 мкм), волокна хризотил-асбеста даже в случае попадания в организм человека выводятся за 15 дней, не успевая нанести ему вреда.
Вторая составляющая безопасного производства и использования хризотил-асбеста – контролируемое применение. Этот термин означает, что добыча и использование минерала должны проводиться в соответствии с разработанными нормами, регламентирующими требования к оборудованию, системам очистки воздуха, плановым осмотрам сотрудников и т.д. Профессор-токсиколог Дэннис Паустенбах в своем исследовании состояния здоровья рабочих, занятых в ремонтных мастерских и постоянно контактирующих с хризотиловыми накладками на тормозные колодки, отмечает что «выбросы продуктов изнашивания тормозов (пыли или обломков) не загрязняют окружающий воздух волокнами асбеста длиной более 5 мкм». Если взять статью «Токсикология асбестосодержащих тормозных накладок: роль в развитии мезотелиомы», то там сказано следующее: «эпидемиологические и мета-аналитические исследования с точки зрения взвешенности доказательств не показывают существенного риска развития ЗМ (злокачественной мезотелиомы – прим.ред.) у механиков, выполняющих работы с такими фрикционными изделиями, содержащими хризотил».
Борьба за рынки
В отношении к асбесту мир разделился на два лагеря. Несмотря на то, что разницу между амфиболом и хризотилом признает даже Всемирная организация здравоохранения (ВОЗ), которая решением Генассамблеи декларировала дифференцированный подход к использованию разных видов минерала, страсти в отношении асбеста не утихают. Еще бы – на кону огромный автомобильный рынок, емкость которого оценивается в сотни миллиардов долларов.
Благодаря уникальным свойствам, колодки из асбеста доступнее и эффективнее других. С одной стороны, это сильное преимущество – что еще нужно потребителю? С другой стороны – это сильный вызов. Хризотил-асбест – слишком неудобный конкурент для производителей синтетических волокон и схожей продукции. В борьбе с неугодным минералом в ход идут любые средства от лоббизма до проведения проплаченных информационных кампаний, направленных на формирование негативного общественного мнения по отношению к асбесту.
Итогом этой диверсионной деятельности становятся громкие, но ничем не подкрепленные публикации в СМИ, голословные высказывания активистов и другие скандалы. Под давлением общественности производители автомобильных компонентов в ряде стран, например в США, вынуждены отказываться от использования асбеста несмотря на то, что никаких норм, законодательно ограничивающих использование минерала нет. К примеру, в 2017 году компания Yamaha отозвала с российского рынка 128 квадроциклов модели YFM-90R, проданных с 2015 по 2017 год. Причиной для странного демарша стало подозрение на возможность наличия хризотил-асбеста в накладках на тормозные колодки. Потребители, что характерно, были вполне довольны продуктом компании и очень удивились такому решению.
Что самое интересное, претензии антиасбестового лобби часто выходят за грани разумного. Используя любые общественные площадки, активисты декларируют, что асбестовые колодки выделяют в атмосферу волокна минерала, загрязняющие воздух. Только вот наука говорит о том, что при торможении, из-за воздействия высоких температур, возникающих при трении, из колодок выделяется вовсе не асбест, а форстерит, который не является канцерогеном и не опасен ни для среды, ни для человека.
В конце-концов, результат битвы за тормоза пока завис на стадии равенства сил. С одной стороны полноценно реабилитировать хризотиловые тормозные колодки пока не получается, но и у производителей синтетических аналогов запретить их насовсем тоже не выходит. Хотя, при учете общих тенденций в развитии как международных отношений, так и науки, у хризотила есть вполне веские основания не сомневаться в своем будущем.
На что обратить внимание при выборе тормозных колодок — журнал За рулем
Выбирая подходящие тормозные колодки для автомобиля, мы решаем более приземленную задачу, чем разработка системы мгновенной остановки поездов. Однако и с колодками все не так просто. С чего начать поиски нужных колодок, куда смотреть, чему верить? Попробуем разобраться.
Какие имена на «тормозном рынке» России можно считать самыми надежными?
Поскольку высшая честь для производителя — поставлять комплектацию на конвейеры автозаводов, то можно назвать три имени: Federal-Mogul, TMD Friction и Galfer. Эти компании лидируют в первичной поставке тормозных колодок для европейского рынка по легковой тематике. Крупнейший поставщик — Federal-Mogul.
Это еще не все. Автозаводу отдельно взятые колодки не нужны: его интересуют тормозные системы «под ключ». В частности, колодки должны быть совместимы различными электронными устройствами тормозной системы (ABS, EBD, EDS, ASR и т.п). Вот почему на конвейер колодки поставляются через производителей тормозных систем, крупнейшими из которых для европейских автопроизводителей легковых автомобилей являются TRW, Brembo, Continental (ATE), Akebono, CBI.
На оригинальной колодке крупно нанесен логотип автопроизводителя и логотип производителя тормозной системы. Поэтому конечные потребители иногда ошибочно полагают, что бренд, относящийся к логотипу производителя тормозной системы, и есть бренд реального производителя тормозной колодки.
А на какие бренды в первую очередь смотреть в магазине?
Например, вот на эти: Ferodo,Wagner, Textar, Mintex, Pagid, Galfer, Brembo, ATE, TRW, Bosch, Icer, Remsa, LPR и др.
С чего начать выбор нужной мне колодки?
С номера оригинальной детали. Его найти несложно — в дилерском центре всегда подскажут. Деталь с таким номером могут производить несколько фирм. Но следует помнить, что оригинальная колодка будет по определению и самой дорогой. Если вопрос об экономии не стоит, то это — лучший выбор. Продукция, идущая на конвейер, распространяется в основном через авторизованные дилерские центры, но иногда поступает и в обычные автоцентры. Но уж если решили не экономить, то лучше платить у официалов. Это будет стопроцентное попадание «в оригинал».
А если хочется сэкономить? Тогда нас ждет продукция для вторичного рынка.
Чем вторичный рынок хуже первичного?
Ничем! Так обычно говорят производители. Мол, тот же конвейер, та же технология. Но не всегда это именно так. К примеру, если конвейерная колодка испытывается по десятку с лишним параметров, то ее вторичная подруга — преимущественно по трем. Это плотность крепления материала к несущей пластине, тест на сжимаемость фрикционного материала и динамометрические испытания по замеру трения. Это обязательные тесты для вторичного рынка Европы. На такую продукцию ставят клеймо R90 на соответствие одноименным правилам. Без этого клейма колодка не может быть продана на вторичном рынке в странах Евросоюза.
Так чем же хуже вторичные колодки?
У них может быть несколько иной состав фрикционной смеси. Они могут чуть хуже тормозить, иметь меньший ресурс. Однако разница с оригиналом исчисляется несколькими процентами — не более.
Проблема совсем в другом. Соответствие правилам R90 не обсуждается — наличие клейма обязательно. Но номер такой колодки будет отличаться от оригинального, а потому для покупателя возможны приключения.
Какие — понятно, в общем-то… Предстоит обнаружить кросс-ссылку, которая выведет вас с номера оригинальной колодки на неоригинальную. Тут может помочь продавец — в профильных торговых точках всегда есть база данных: например, база TecDoc. В нее загружают информацию большинство серьезных поставщиков, в том числе и упомянутые выше.
Перед покупкой желательно сопоставить свою старую колодку с новой: компьютеры тоже умеют подвирать. Но и тут возможны «приключения»: следует помнить, что различия по внешнему виду вполне допустимы! Колодки могут отличаться, допустим, покрытием, которое снижает вибрации и шум. Колодка премиум-класса имеет, как правило, металлическую антишумовую пластину. А вот колодки эконом-класса и среднего сегмента — резиновое, типа мастики, как правило, с неровной поверхностью. По своим характеристикам эти типы покрытий могут быть идентичными, но металлическая антишумовая пластина выглядит намного эстетичнее и меньше подвержена повреждениям в сравнении с покрытием типа мастики.
Можно ли ставить такие колодки на дорогую машину? Тут опять некоторое лукавство — многое зависит от владельца. Один даже «старушку» будет гонять к официалам, другой сразу же после окончания гарантии уйдет «налево». И в этом случае он будет искать только бюджетный вариант.
Где купить вторичную колодку?
Лучше всего — у тех же официалов: они, как правило, предлагают как оригинальные запчасти, так и более доступные по цене — для послегарантийных машин. Опять-таки, речь идет о надежности продавца.
Понятно, что к автодилерам поедут далеко не все, потому что изначальная цель поиска вторичных колодок была простая: сэкономить. Есть и более дешевые места — сетевые розничные магазины вроде «Авто-49», и интернет-магазины типа Exist. Но с этого момента опять начинается лотерея, потому что, не будучи специалистом, отличить колодки премиум-качества от собратьев более низкого ранга уже почти невозможно. Некоторые произво
Фрикционная смесь и ее влияние на характеристики колодок
В составе фрикционной смеси тормозной колодки содержится в среднем от 20 до 30 различных составляющих, включая органические и неорганические волокна, абразивы, минеральные, синтетические и органические смазочные материалы, металлическую стружку и др. наполнители.
Сочетание этих компонентов в той или иной пропорции обеспечивает адресный подбор фрикционной смеси под тот или иной тип применения. К примеру, большее содержание абразивов увеличивает эффективность торможения, которая характеризуется безразмерной величиной, называемой коэффициентом трения. Чем выше коэффициент трения, тем меньше тормозной путь автомобиля.
Большое содержание абразивов в составе фрикционной смеси приводит к чрезмерному износу колодки, диска и повышенной шумности при торможении.
Однако слишком большое содержание абразивов в составе фрикционной смеси приводит к чрезмерному износу колодки, диска и повышенной шумности при торможении. Графит, сульфиды металлов в составе смеси выполняют роль смазки. Они снижают степень износа колодки и диска, уменьшают шум при торможении, но приводят к уменьшению коэффициента трения и повышению вибрации при торможении. Чрезмерное содержание стальной стружки и органических соединений в составе смеси увеличивает долю углеродистых отложений в продуктах износа колодки.
До середины 90-х годов XX века в составе фрикционных смесей активно использовался асбест, обеспечивающий высокий коэффициент трения и высокую температурную стабильность. Общее количество компонентов в составе фрикционной смеси асбестосодержащей колодки по сравнению с современной колодкой было значительно меньше (6–10 компонентов). Компания Ferodo первой на рынке еще за 16 лет до официального запрета асбеста наладила выпуск безасбестовых фрикционных смесей. Заменить асбест одним компонентом невозможно, поэтому общее количество составляющих в смеси увеличилось.
Медь до недавнего времени являлась одним из основных компонентов фрикционной смеси тормозной колодки с удельным весом до 20%. Медь выполняла следующие важные функции: обеспечение эффективности торможения, снижение шума при торможении, снижение пыльности при износе, обеспечение эффективного отвода тепла, обеспечение целостности и прочности фрикционной смеси. Однако медь – тяжелый металл, и в окружающей среде она окисляется, образуя вредные соединения. Мельчайшие частицы меди с продуктами износа фрикционного материала попадают на дорожное полотно и смываются дождями в водоемы, где медь оказывает негативное влияние на экосистему водной среды. Постепенное ограничение на использование меди во фрикционных смесях уже принято в ряде штатов США – к 2021 году ее содержание в тормозных колодках должно быть менее 5%, а к 2025 году – менее 0,5%, что принято считать нулевым содержанием. Похожие инициативы вводятся и в странах Европы. Предполагается, что к 2025 году содержание меди в составе фрикционной смеси тормозных колодок будет законодательно регламентировано или полностью запрещено во всем мире. И уже сегодня крупнейшие европейские автопроизводители требуют установки на свои автомобили тормозных механизмов с колодками с пониженным и нулевым содержанием меди.
Крупнейшие европейские автопроизводители требуют установки на свои автомобили тормозных механизмов с колодками с пониженным и нулевым содержанием меди.
При проектировании тормозной колодки должны учитываться основные тенденции в современном автомобилестроении. Увеличение доли автомобилей с электрическими и гибридными силовыми установками (требуются смеси с пониженной шумностью при торможении), использование электромеханического стояночного тормоза (требуются смеси с большим коэффициентом статического трения), применение производителями тормозных систем суппортов меньшего размера и веса для снижения неподрессоренных масс в подвеске автомобиля (уменьшение размера тормозной колодки – использование фрикционной смеси с обеспечением большей эффективности торможения), использование тормозных колодок с меньшим содержанием во фрикционной смеси стальной стружки и с меньшим или нулевым содержанием меди (существующие и грядущие законодательные ограничения) – все эти тенденции были учтены в недавно внедренной Federal-Mogul новой технологии тормозных колодок Ferodo Eco-Friction с низким или нулевым содержанием меди.
Основой для Ferodo Eco-Friction стала комбинация из 25 компонентов, в том числе сульфидов металлов, минералов, абразивов, волокон, керамических частиц и различных видов графита. Этот состав обеспечивает эффективность торможения, не уступающую медьсодержащим фрикционным материалам. Результаты независимого тестирования колодок по технологии Eco-Friction для популярных европейских автомобилей подтвердили их превосходство по эффективности торможения в сравнении со стандартными медьсодержащими колодками Ferodo Premier и с продукцией конкурентов (меньший тормозной путь и меньшая степень износа в паре трения колодка/диск). Благодаря успешным исследованиям Federal-Mogul стала мировым лидером в области создания фрикционных материалов с низким или нулевым содержанием меди.
Более 85% ассортимента колодок Ferodo для вторичного рынка выполнены по технологии Eco-Friction.
Серийный выпуск колодок Eco-Friction начался в 2014 году, когда компания Daimler выбрала продукцию Ferodo в качестве оригинальных комплектующих для нового Mercedes-Benz C-Class, а с сентября 2015 года колодки Eco-Friction устанавливаются и на Audi A4. Также эти колодки были рекомендованы для вторичного рынка автокомплектующих. Свыше 85% ассортимента колодок Ferodo для вторичного рынка выполнены по этой современной технологии.
До середины XX века фрикционная накладка дисковой тормозной колодки прикреплялась к несущей стальной пластине потайными заклепками во многих точках, но в середине XX века для соединения композитов с металлом были разработаны достаточно термостойкие и прочные клеи на основе термореактивных смол. В технологии производства дисковых тормозных колодок как для легковых, так и для грузовых автомобилей в настоящее время используется два основных способа формования фрикционного материала на стальной несущей пластине: прессование (только давление) и термопрессование (давление плюс нагрев). При производстве фрикционных накладок для грузовой техники используется метод термопрессования фрикционного материала. Для барабанных тормозов легковых и легких коммерческих автомобилей фрикционная накладка приклеивается к поверхности стального башмака. Фрикционные накладки барабанных тормозных механизмов для грузовых автомобилей закрепляются на тормозном башмаке с помощью заклепок. Это обуславливается большими габаритами тормозного механизма, более высокими нагрузками на фрикционную накладку при торможении, а также удобством и оптимизацией затрат при замене фрикционных накладок при регламентном обслуживании тормозной системы (без необходимости замены тормозных башмаков).
Большое содержание абразивов в составе фрикционной смеси приводит к чрезмерному износу колодки, диска и повышенной шумности при торможении.