Тормозные диски HPB. Конструкция, технология изготовления.
Тормозные диски HPB изготавливаются из легированного чугуна марки FC30, с добавками (Cr, Ni, Mo), по технологии предварительной термообработки заготовок, имитирующей условия предельных термонагрузок. Эта технология позволяет выявить большую часть возможных неравномерных статических напряжений в материале, проявляющихся в виде изменения заданной геометрии — коробления диска, сводя к минимуму возможность появления данного негативного процесса в готовом продукте.
Больший диаметр тормозного диска, увеличивает эффективный радиус приложения тормозного момента, позволяя поднять максимальную тормозную мощность, развиваемую системой. От эффективного радиуса, напрямую зависит площадь охвата рабочих поверхностей, являющихся одним из основных показателей возможностей диска по рассеиванию тепловой энергии.
Тормозные диски HPB имеют увеличеную толщину, это поднимает теплоёмкость и увеличивает устойчивость к нарушению геометрии (короблениям) при больших нагрузках. Улучшает охлаждение, за счёт повышения площади обдуваемой поверхности внутренних каналов вентиляции диска.
Направленные каналы вентиляции, по сравнению с традиционной прямой конструкцией, значительно повышают интенсивность прокачки воздуха по ним, улучшая теплоотдачу. Спиральная конструкция каналов более равномерно распределяет механические напряжения в диске, увеличивая ресурс и уменьшая вероятность образования трещин.
Алюминиевый центр тормозного диска, снижает вес, улучшает теплоотвод, уменьшает термические напряжения в диске. Термическое напряжение в диске вызывается разницей температур диск-центральная часть, алюминиевый центр компенсирует эту разницу коэффициентов расширения материалов.
Фиксированная конструкция диска рассчитана на температурный режим до 500°С, рекомендуется для городского использования.
В случае использования «плавающей конструкции» диска, рекомендуемой для применения в режимах предельных нагрузок (на гоночном треке), позволяет полностью снять термо-напряжения относительно центральной части и предотвратить передачу избыточного тепла на ступичный подшипник. Обеспечивая нормальную работу и увеличенный ресурс этих деталей в самых жёстких условиях.
Тормозные диски с проточками.
Проточки на рабочих поверхностях диска помогают отводить из зоны контакта колодки мелкие частицы износа и газовую фракцию (продукт разложения связующих смол, входящих в состав фрикционного материала тормозной колодки, эффект появляющийся при высоких температурах и приводящий к резкому падению коэффициента трения). Проточка, работая как газоотводный канал, предотвращает снижение эффективности торможения и расширяет границы режима работы колодок.
Кроме своих основных функций, поскольку глубина проточки составляет 1мм., она служит отличным визуальным индикатором предельного износа диска.
Перфорированные тормозные диски.
Перфорация диска, выполняя все те же функции по газоотводу, что и проточки, увеличивает площадь обдуваемой поверхности диска, улучшая охлаждение. При круглогодичной эксплуатации улучшает очистку диска от влаги и грязи.
Тормозные диски с волнистым краем.
Специалисты High Performance Brakes успешно разработали и создали тормозную систему с новым дизайном: тормозные диски в комплектах имеют волнистую кромку.
Преимущество тормозных систем с «волнистыми» дисками заключается не только в необычном дизайне и особой эстетике, но также в положительных технических характеристиках. Благодаря необычной волнистой форме, такой ротор имеет меньший вес по сравнению с классическим круглым диском, а значит, снижаются и неподрессоренные массы и общие нагрузки на подвеску автомобиля.
Таким образом, тормозные системы HP-Brakes с «волнистыми» дисками способствуют снижению нагрузок на обеих осях автомобиля, повышают общий ресурс тормозов при прежней высокой эффективности и износостойкости.
при копировании материалов сайта обязательна ссылка на источник
HPB
Способ изготовления тормозного диска и тормозной диск
Настоящее изобретение относится к способу изготовления тормозного диска для транспортного средства и к тормозному диску для транспортного средства.DE AS 1 625 680 описывает фрикционную корпусную деталь для работающих в масляной ванне сцепления и тормозов, имеющую опору, и по меньшей мере одну спеченную пористую и металлическую фрикционную накладку, приложенную к опоре. Предложение состояло в том, что фрикционная накладка должна состоять из металлических волокон, при этом, степень пористости должна была иметь значение по меньшей мере 50%.
DE 10 2010 049 797 A1 раскрывает, что тормозной диск может быть изготовлен как целая часть со ступицей колеса, намерение состоит в том, чтобы дать возможность, чтобы было уменьшено биение тормозного диска. Более того, фрикционные поверхности тормозного диска могли бы быть оснащены фрикционным покрытием, которое может состоять из твердого металла или керамики.
На транспортных средствах, особенно моторных транспортных средствах, дисковые тормоза формируют то, что вероятно является наиболее широко распространенным типом тормозных систем. Дисковые тормоза по существу состоят из тормозного диска и тормозной скобы, которая помещена вокруг кромки тормозного диска. В этой компоновке, тормозной диск присоединен ступицей колеса, установленной с возможностью вращения в поворотной цапфе, к колесу транспортного средства, которое должно тормозиться. В противоположность, тормозная скоба закреплена на поворотной цапфе. Реальное замедление достигается посредством тормозных колодок, которые могут быть размещены вплотную к тормозному диску, упомянутые колодки выполнены по обе стороны от тормозного диска между тормозным диском и тормозной скобой.
В зависимости от применения, тормозные диски могут состоять из железа, например, серого чугуна или, в качестве альтернативы, из углеродистой керамики или алюминия. Одновременно, тормозные диски должны иметь поверхность, которая демонстрирует как можно меньший износ и выпускает мало мелкой пыли. Для достижения этого, целью является поверхность, которая является как можно более твердой. Таким образом, в случае тормозных дисков, например, сделанных из алюминия, карбид кремния (SiC) добавляется надлежащим образом, будучи нанесенным в качестве износостойкого защитного покрытия на поверхности. Однако, производство тормозных дисков из не содержащих железо материалов, в некоторых случаях, является сложным и обычно дорогостоящим.
Еще одна форма воплощения такого защитного слоя может быть достигнута термическим напылением. В этом процессе, материал, который должен быть нанесен на поверхность основного корпуса тормозного диска, заблаговременно размягчается под действием тепла и ускоряется в виде отдельных частиц посредством газового потока. При ударе частиц, формируется чисто механическая связь без расплавления поверхности основного корпуса. Материалы могут быть металлами или оксидными керамическими или твердосплавными материалами. Недостатком здесь, кроме высоких затрат, в особенности является долговечность таких защитных слоев. Таким образом, как правило, возможно всего лишь умеренное придание шероховатости поверхности посредством пескоструйной обработки, и это не приводит к долговременной механической связи. Более точно, при использовании твердого чугуна для основного корпуса, например, невозможно придание шероховатости врубкой, которое полезно само по себе.
В процессе абразивного износа между тормозной накладкой и тормозным диском происходят выбросы твердых частиц, то есть, мелкой пыли. Кроме проблемы мелкой пыли, однако, зрительный эффект ржавых тормозных дисков в комбинации с дорогостоящими алюминиевыми колесными дисками играет дополнительную роль. Известно, что около 70% мелких частиц пыли возникают из материала диска из серого чугуна. Температура, на которой эти частицы, вырабатываемые износом, ударяют алюминиевый колесный диск, очень высока, имея значение вплоть до 700°C. В процессе, они могут просто въедаться в прозрачное покрытие на алюминиевой поверхности, а удаление серо-черного покрытия является весьма трудным, даже на автомойке и с высочайшим старанием. Более того, визжащие шумы или дрожание тормозов в случае накладки, которая заржавела после пребывания неподвижной в течение продолжительного периода, дополнительно рассматриваются в качестве причиняющих беспокойство.
Было бы можно улавливать формируемые мелкие частицы пыли посредством разновидности вакуумного пылесборника за тормозным диском и собирать их в фильтрующем элементе, например, в бумажном фильтре. Хотя посредством этого можно предотвращать или минимизировать загрязнение окружающей среды или образование грязных алюминиевых колесных дисков, основная проблема износа и коррозии не решается посредством этого.
Также можно предусматривать то, что указывается ссылкой как временные недорогие защитные слои, чтобы давать транспортным средствам возможность по меньшей мере добираться до торгового представителя от производителя без вынуждения совершенно нового транспортного средства показываться в выставочном зале торгового представителя с ржавыми тормозными дисками. Таковые, как правило, являются окрашенными напыленными слоями, содержащими в себе цинковые пигменты. С другой стороны, известны тормозные системы, в которых цинк втирается в поверхность серого чугуна во время процесса торможения, тем самым, вызывая катодную защиту от коррозии. С другой стороны, цинковая пленка оказывает отрицательное влияние на фрикционную функцию тормозной накладки, и коэффициенты трения снижаются.
Покрытие посредством диффузионного азотирования на основании нитрида железа также было бы возможным. Это покрытие приводит к краткосрочной защите от износа и коррозии; однако, срок службы этого покрытия ограничено. В странах с высокими предельными значениями скорости для транспортных средств, например, в Германии, это дает в результате высокие температуры торможения, по какой причине, накладки из NAO не пригодны в этих странах. Более того, процесс является очень трудоемким и весьма дорогостоящим благодаря требуемым большим печным камерам.
Многочисленные способы термического напыления (уже упомянутые выше) и способы электролитического покрытия используются подобным образом. Эти слои являются весьма дорогостоящими для производства. В случае электролитических способов, вес компонент должен быть покрыт хромом или никелем плюс частицами твердого материала. Однако, как такие электролитические покрытия, так и термически напыленные покрытия имеют тенденцию плохо работать при ускоренных испытаниях на коррозионную стойкость в солевом тумане. Таким образом, подмыв слоев термического напыления не может надежно избегаться даже с дополнительными способами пломбировки.
Ввиду указанного предшествующего уровня техники, по-прежнему есть место для улучшения простого и надежного производства тормозных дисков в качестве изделий массового производства.
При условии этой сложившейся ситуации, лежащая в основе изобретения задача состоит в том, чтобы представить способ изготовления тормозного диска для транспортного средства, какой способ предоставляет возможность недорогого и, тем не менее, надежного массового производства. Более того, намерение состоит в том, чтобы показать тормозной диск для транспортного средства, который, в дополнение к недорогому производству, в частности, имеет улучшенную устойчивость к коррозионному действию и улучшенный срок службы.
Часть задачи, относящейся к способу, достигается мероприятиями по пункту 1 формулы изобретения. Часть упомянутой задачи, относящейся к изделию, достигается тормозным диском, имеющим признаки по пункту 11 формулы изобретения. Кроме того, особенно полезные варианты осуществления изобретения раскрыты соответственными зависимыми пунктами формулы изобретения.
Должно быть отмечено, что признаки и мероприятия, представленные по отдельности, в последующем описании могут комбинироваться технически осуществимым образом и давать начало дополнительным вариантам осуществления изобретения. Описание дополнительно характеризует и детально излагает изобретение, в особенности, совместно с фигурами.
Согласно изобретению, ниже представлен способ изготовления тормозного диска для транспортного средства, в котором на основном корпусе тормозного диска по меньшей мере в некоторой области или областях расположен защитный слой. Согласно изобретению, способ содержит по меньшей мере следующие этапы:
— предварительной машинной обработки по меньшей мере некоторой области или областей основного корпуса, находящегося в виде заготовки;
— нанесения эмалевого покрытия на основной корпус по меньшей мере в некоторой области или областях, и
— последующей обработки основного корпуса, содержащего покрытие по меньшей мере в некоторой области или областях, при этом эмалевое покрытие металлургически привязано к материалу основы основного корпуса посредством фазообразования.
Эмалевое покрытие согласно этому изобретению предпочтительно является расплавленной смесью. При температуре эмалировки, стеклообразующие оксиды сплавляются для формирования стеклянного расплава. Здесь, стеклообразующими оксидами могут быть SiO2, B2O3, Na2O, K2O и Al2O3. Базовые эмали содержат приблизительно 23-34% по весу буры, 28-52% по весу полевого шпата, 5-20% по весу кварца, около 5% по весу фтористых соединений, оставшейся частью является углекислый натрий и натриевая селитра. Оксиды Ti, Zr и Mo могут использоваться в качестве замутнителей.
Чтобы гарантировать, что эмалевые покрытия жестко прилипают к металлической подложке, то есть, к материалу основы основного корпуса, например, в качестве составляющих предусмотрены оксиды кобальта, оксиды марганца или оксиды никеля. Также можно использовать керамические пигменты, такие как оксиды железа, оксиды хрома и шпинели.
В предпочтительном варианте осуществления, упомянутые вещества мелко перемолоты и расплавлены. Расплав резко охлаждается, то есть, предпочтительно добавляется в воду, при этом, гранулированная фритта стеклянного типа, сформированная таким образом, еще раз мелко перемалывается на следующем этапе. Во время процесса перемалывания, например, добавляются от 30% до 40% воды вместе с глиняной и кварцевой мукой. В зависимости от типа эмали, также добавляются упомянутые замутнители и пигментные оксиды.
Таким образом, формируется эмалевая суспензия, которая должна выстаиваться в течение определенного времени, предпочтительно несколько дней, чтобы обеспечивать лучшее смешивание перед тем, как эмалевая суспензия используется дальше. Пригодные текучие агенты используются, чтобы гарантировать, что получается равномерная толщина слоя, например, после нанесения покрытия погружением, и возможный процесс нанесения покрытия погружением будет пояснен подробнее.
Тормозной диск, то есть, его основной корпус, предпочтительно изготавливается посредством отливки в песчаную форму. В этом случае, основной корпус, то есть, заготовка, имеет окружающую наружную тормозную шайбу, которая предусмотрен для контакта с тормозной колодкой тормозной скобы, при этом, конечно, тормозные колодки или тормозные накладки контактируют по обеим сторонам тормозной шайбы, то есть, фрикционных поверхностях. В центре основного корпуса предусмотрен проем, который размещен в выступе основного корпуса. Вокруг проема, на равных интервалах, расположено предпочтительно пять сквозных отверстий через выступ. Упомянутые сквозные отверстия служат для приема колесных болтов, посредством которых тормозной диск, вместе с колесом, может быть присоединен к ступице колеса. Выступ, который также может указываться ссылкой как головка диска, может изготавливаться как целая часть, то есть, может отливаться с тормозной шайбой или может присоединяться пригодным образом к тормозной шайбе в качестве отдельного элемента. Основной корпус может быть изготовлен в виде невентилируемого или вентилируемого тормозного диска, это известно само по себе. В случае вентилируемого тормозного диска, фрикционные поверхности расположены на опорных дисках, при этом, противоположные опорные диски расположены на определенном расстоянии посредством ребер. Каждый опорный диск, конечно, также имеет только одну фрикционную поверхность, но это известно само по себе. Таким образом, воздушный зазор сформирован между опорными дисками, хотя это известно само по себе, а потому, дополнительные подробности этого приведены не будут.
Эта заготовка затем подвергается машинной обработке по меньшей мере в некоторой области или областях, при этом, в частности, подвергаются предварительной машинной обработке будущие фрикционные поверхности. Предварительная машинная обработка может выполняться посредством механических способов, при этом, предварительная машинная обработка предпочтительно выполняется посредством способов токарной обработки, предпочтительнее, посредством способов безэмульсионной токарной обработки (безэмульсионной токарной обработки). В этом случае, области, которые должны быть покрыты, то есть, например, фрикционные поверхности, предпочтительно подвергаются машинной обработке таким образом, чтобы они, например, имели шероховатость от 6 до 7 микрон. Пескоструйная обработка также возможна в целях предварительной машинной обработки, и нет намерения исключать другие пригодные способы предварительной машинной обработки.
Как только по меньшей мере фрикционные поверхности были подвергнуты предварительной машинной обработке, может наноситься эмалевое покрытие. Это может выполняться посредством напыления, хотя нанесение посредством обмазывания кистью или в ванне для обработки погружением также может быть целесообразным. Таким образом, целесообразно, если покрытие, то есть, эмалевая суспензия наносится в качестве влажного эмалевого покрытия.
В случае нанесения посредством напыления, предусмотрено, чтобы целесообразно эмалевое покрытие наносилось виде водной суспензии (эмалевой суспензии). Здесь полезно, чтобы по меньшей мере подвергнутая предварительной машинной обработке область была без труда доступна, поскольку устройство для напыления может покрывать область, которая должна быть покрыта на индивидуальной основе. Покрытие может наноситься таким образом, чтобы основной корпус предпочтительно был вращающимся. Можно заставлять тормозной диск вращаться на 80 оборотах в минуту. Эмалевое покрытие может напыляться под давлением от 2 до 4 бар, например, посредством распыления сжатым воздухом. Таким образом, эмалевое покрытие может быть нанесено требуемой толщиной материала в течение очень короткого времени, например, 20 секунд, при этом, скорости подачи эмалевой суспензии могут регулироваться в нешироких пределах согласно автоматическому контролю параметров, например, посредством управляемых компьютером роботов для напыления, для того чтобы быть способными создавать соответственное эмалевое покрытие с небольшими колебаниями толщины в каждом случае. В способе согласно изобретению, предпочтительно выбран способ одностадийного нанесения эмалевого покрытия. Это дает возможность обходиться без отдельного нанесения базовой эмали и эмали верхнего слоя, поскольку предпочтительно всего лишь одностадийное нанесение. Вращающееся устройство для напыления и неподвижный тормозной диск, который должен быть покрыт, также возможны, но не предпочтительны. Таким образом, можно снабжать эмалевым покрытием только область фрикционных поверхностей. Это может выполняться таким образом на невентилируемых тормозных дисках, но также на вентилируемых тормозных дисках. В качестве дополнительного возможного варианта осуществления, основной корпус может быть покрыт в ванне для обработки погружением, при этом, водный раствор (эмалевая суспензия) предоставляется подобным образом. В этом случае также можно покрывать только тормозную шайбу, то есть, только фрикционные поверхности. В процессе этого, основной корпус погружается в ванну для обработки погружением не полностью, а только на глубину, такую чтобы тормозная шайба окуналась на определенном участке. Посредством вращения тормозного диска, таким образом покрывается вся тормозная шайба. В частности, целесообразно снабжать вентилируемый тормозной диск эмалевым покрытием посредством ванны для обработки погружением, поскольку влажное эмалевое покрытие также может полностью проникать в промежутки между двумя опорными дисками, таким образом, предоставляя возможность, чтобы были покрыты даже внутренние поверхности по другую сторону от фрикционных поверхностей, тем временем, конечно, также могут покрываться.
Вместо частичного покрытия, при котором покрыты только тормозная шайба, то есть, фрикционные поверхности, также возможно, чтобы основной корпус был покрыт полностью. Соответственно, тормозной диск, в таком случае, полностью защищен от коррозии. Целесообразно предусматривается, чтобы основной корпус также полностью подвергался предварительной машинной обработке.
Еще раз, здесь можно предусматривать эмалевое покрытие посредством устройства для напыления или в ванне для обработки погружением. В ванне для обработки погружением, тормозной диск полностью затапливается, если тормозной диск должен быть покрыт полностью. Вращение упомянутого тормозного диска не обязательно, но может быть желательным. Если эмалевое покрытие наносится посредством устройства для напыления, можно наносить эмалевые покрытия, которые отличаются по меньшей мере цветом. Выступ, то есть, головка диска, например, также мог бы быть реализован, с тем чтобы быть светящимся в условиях тусклого освещения. Это уместно, поскольку сам выступ не подвергается воздействию никаких сил трения, подобных фрикционным поверхностям. Тем не менее, конечно, также было бы можно воплотить фрикционные поверхности с определенным цветом, если бы обеспечивалось, чтобы цвет оставался неизменным, даже после зацепления тормозных накладок, то есть, после износа соответственных фрикционных поверхностей.
Если тормозной диск покрыт по меньшей мере частично, он подвергается последующей обработке на дополнительном этапе. Для этой цели, преимущественно предусмотрено, чтобы эмалевое покрытие было прежде всего высушено после нанесения, после чего, обеспечивается обработка обжигом. Для высушивания эмалевого покрытия, тормозной диск подается в сушильное устройство, в котором покрытый эмалевым покрытием тормозной диск высушивается приблизительно при от 90 до 120°C, или приблизительно при от 80 до 100°C, в течение периода от 5 до 30 минут. В предпочтительном варианте осуществления способа, процесс высушивания может выполняться в печи с циркуляцией воздуха. Для последующей тепловой обработки, покрытый эмалевым покрытием тормозной диск обжигается в печи непрерывного действия, например, приблизительно при от 800 до 940°C. Это предоставляет эмалевому покрытию возможность металлургически привязываться к материалу основы основного корпуса посредством фазообразования. Во время этого процесса печной сушки, достигается формирование толстого непрерывного оксидного слоя, который весьма устойчив к действию коррозии от дождевой воды и также, в частности, соленой воды.
Эмалевые покрытия согласно изобретению отличаются от электролитических или напыленных покрытий по той причине, что они не могут подмываться. Если защитные слои подмываются, фаза оксида железа формируется под покрытием, которая затем приводит к большому увеличению объема, ассоциативно связанному с отслаиванием покрывающего слоя. Также благоприятно для успеха, что эмалевые покрытия согласно изобретению не могут страдать от дальнейшего повреждения, даже если слой снят до материала основы местным повреждением (ударом камня, механическим повреждением). Повреждение ржавчиной, в таком случае, происходило бы в только в области отсутствующего эмалевого покрытия, но не распространялось бы дальше. Еще одно преимущество эмалевого покрытия согласно изобретению должно рассматриваться в качестве того обстоятельства, что оно имеет очень низкий вес, это является свойственным химическому составу из оксидов алюминия, силикатов, и т. д., порам и пузырьковой структуре, типичным у эмали.
В дополнение к этой хорошей коррозионной стойкости, эмалевое покрытие согласно изобретению отличается хорошим сопротивлением износу в силу высокой твердости слоя, которая может быть в три раза большей, чем у материала основы из серого чугуна. Сопротивление износу и/или термическим трещинам дополнительно может усиливаться использованием «частично кристаллических эмалей», в которых отложения кристаллизации в стеклянной матрице повышают сопротивление износу по сравнению с традиционными эмалями. Также способствующим успеху является то обстоятельство, что характеристики износа эмали могут быть радикально улучшены посредством включения в состав наноразмерных твердых материалов. Эти карбидные жесткие материалы имеют значительно большее сопротивление износу, чем аморфная эмалевая матрица. Сопротивление износу дополнительно может быть оптимизировано посредством изменения размера карбидных частиц.
Серый чугун предпочтительно может использоваться в качестве материалы основы.
После этапа печной сушки, поверхность эмалевого покрытия по выбору может подвергаться конечной обработке, то есть, чистовой обработке. Предусмотрено, что предпочтительно осуществлять машинную обработку фрикционных поверхностей посредством токарной обработки и удалять слой окалины, сформированной вследствие процесса обжига.
Конечно, можно, чтобы тормозные диски использовались без какой бы то ни было машинной обработки в области фрикционной поверхности. Посредством использования более тонких эмалевых покрытий и использования индукционных катушек для спекания слоев в комбинации с вращательным движением, любое возможное радиальное истончение, а также неровность могут быть минимизированы. Чистовая машинная обработка дисков посредством операции чистовой шлифовки также возможна, при этом, используются алмазные или карбидные чашечные шлифовальные круги. Возможна чистовая машинная обработка посредством токарной обработки, это является осуществимым, несмотря на высокую твердость благодаря хрупкости, при этом, предпочтительны поликристаллические алмазные индексируемые режущие пластины.
Благоприятно для успеха, если нанесено эмалевое покрытие с толщиной слоя от 50 мкм до 100 мкм. В силу этого возможно изготавливать тормозные диски, которые могли бы иметь срок службы более чем 240000 км в зависимости от толщины слоя эмалевого покрытия.
Чтобы гарантировать, что сопротивление износу достаточно высоко, доказано, что полезно адаптировать состав эмалевого покрытия таким образом, чтобы, после спекания, то есть, после процесса обжига, значения твердости были > 650 HV0,1. Более того, этот состав дает в результате эмалевое покрытие стеклянного типа, которое не полностью оплавлено и имеет не гладкие поверхности, типичные для эмали, но скорее шероховатую поверхность, вызванную более высокой долей кристаллических фаз. В идеале, доля кристалла может иметь значение 20%, но также 30-50%.
В силу выдающихся коррозионной стойкости и сопротивления износу фрикционного слоя, способ эмалировки согласно изобретению особенно пригоден для изготовления тормозных дисков. Более того, способ согласно изобретению предлагает возможность настройки коэффициентов трения в широких пределах таким образом, чтобы, благодаря добавлению некоторых оксидов, могли использоваться традиционные фрикционные накладки, при этом, коррозионная стойкость и сопротивление износу были значительно улучшены относительно традиционных тормозных дисков из серого чугуна.
В дополнение, эмалевое покрытие может быть пигментировано, давая возможность выбирать разные цвета на индивидуальной основе, как уже упомянуто выше.
Посредством изобретения, можно наносить слой эмалевого покрытия по всему тормозному диску в качестве защиты от коррозии (предотвращения красной ржавчины), при этом, также возможно, чтобы эмалевое покрытие было нанесено только в области поверхности трения в качестве покрытия износа с пригодным коэффициентом трения (избежания скрежещущего шума). Эмалевое покрытие может быть нанесено в качестве декоративного легкоочищаемого покрытия в области вне поверхности контакта с фрикционной накладкой, при этом, эмалевое покрытие может быть нанесено в области контакта, для того чтобы предупреждать снятие тормозного диска (предотвращение приржавления к ступице колеса). Способ согласно изобретению может содержать этапы предварительной машинной обработки, нанесения суспензии посредством погружения/напыления, высушивания и обжига, и финишной обработки для получения требуемой шероховатости. Эмалевое покрытие, более того, может обладать теплоизоляционным эффектом, с тем результатом, что тепло, которое возникает, не рассеивается настолько быстро.
Хотя предпочтителен способ одностадийного покрытия, возможно, чтобы диск полностью погружался в недорогую эмалевую суспензию, это особенно целесообразно в случае вентилируемых дисков с большим количеством ребер между двумя опорными дисками, в каком случае, слой дорогостоящей подцвеченной эмали затем наносится при последующем нанесении напылением в области между поверхностью фрикционной накладки и контактной поверхностью чашки (головкой диска). В принципе, частицы ржавчины не могут формироваться на эмалевом покрытии, а потому, проблема со скрежещущим шумом, таким как который может возникать у традиционных тормозных дисков из серого чугуна, избегается.
Кромки основного корпуса, которые снабжены эмалевым покрытием, предпочтительно имеют радиус R, который является по меньшей мере в 3 раза большим, чем толщина слоя эмалевого покрытия в области радиуса кромок. Тем самым, гарантируется равномерная толщина слоя в области кромок. Если переходы или кромки слишком остры, эмалевый слой, который формируется на них, будет слишком тонким.
Дополнительные полезные детали и результаты изобретения подробнее пояснены ниже посредством разных иллюстративных вариантов осуществления, показанных на фигурах, из которых:
фиг. 1 показывает схематическую иллюстрацию тормозного диска согласно изобретению на виде сверху,
фиг. 2 показывает тормозной диск по фиг. 1 в разрезе,
фиг. 3 показывает детализацию фиг. 2;
фиг. 4 показывает вентилируемый тормозной диск на виде в перспективе.
На различных фигурах идентичные части всегда снабжены одинаковыми символами ссылки, а потому таковые, как правило, также описаны только один раз.
Фиг. 1 показывает схематическую иллюстрацию тормозного диска 1 согласно изобретению. Он имеет круглый основной корпус 2, в качестве примера состоящий из чугуна, то есть, например, серого чугуна. Обычно, основной корпус 2 имеет окружающую наружную тормозную шайбу 3, которая предусмотрена для контакта с тормозной накладкой (специально не показана). В центре основного корпус 2 предусмотрен проем 4, который размещен в выступе 5 основного корпуса 2. Выступ 5 также может указываться ссылкой как головка 5 диска. На равных интервалах вокруг проема 4, в данном случае, расположены пять сквозных отверстий 6 через выступ 5. Упомянутые сквозные отверстия 6 служат для приема колесных болтов (здесь специально не показаны), посредством которых тормозной диск 1, вместе с колесом (не показано), может быть присоединен к ступице колеса (также не показана).
Фиг. 2 показывает разрез по плоскости a-a тормозного диска 1 с фиг. 1. Как может быть видно, выступ 5 выступает относительно тормозной шайбы 3 основного корпуса 2. Тормозная шайба 3 содержит две поверхности торможения, то есть фрикционных поверхности 7, 8, ориентированных параллельно друг другу, то есть, первую фрикционную поверхность 7 и вторую фрикционную поверхность 8. Обозначенная линией из точек и штрихов окружность B начерчена на фиг. 2, при этом, область тормозной шайбы 3 внутри окружности B является объектом по фиг. 3.
Фиг. 3 показывает детализацию тормозной шайбы 3 по фиг. 2 в пределах окружности B. При увеличении тормозной шайбы 3 в области ее первой фрикционной поверхности 7, может быть видно, что эмалевое покрытие 10 было нанесено в этой области на поверхность 9 основного корпуса 2. Здесь, эмалевое покрытие 10 также покрывает наружную круговую поверхность. Таким образом, весь тормозной диск 1 может иметь эмалевое покрытие 10. Однако, также возможно, чтобы только фрикционные поверхности 7 и 8 имели эмалевое покрытие 10.
Кромка 14 реализована с радиусом R, чтобы гарантировать, что равномерный эмалевый слой нанесен на эту область. Здесь, радиус R имеет значение приблизительно в три толщины слоя эмалевого покрытия 10. Большие радиусы беспроблемны, но, в случае меньших радиусов, толщина слоя может быть неравномерно распределена в области кромки 14.
Эмалевое покрытие 10 также может быть нанесено на тормозной диск по меньшей мере в некоторой области или областях, при этом, только фрикционные поверхности 7 и 8 снабжены эмалевым покрытием 10. Однако, также можно, как упомянуто, снабжать тормозной диск эмалевым покрытием полностью. Эмалевое покрытие может быть нанесено посредством устройств для напыления или в ванне для обработки погружением.
Фиг. 4 показывает тормозной диск 1, который имеет опорные диски 11 и 12, между которыми выполнены ребра 13, таким образом, формируя вентилируемый тормозной диск 1. Вентилируемый тормозной диск также может иметь эмалевое покрытие 10 только на своих фрикционных поверхностях 7 и 8. Однако, полезно, если вентилируемый тормозной диск 1 полностью покрыт эмалью. Для этой цели, вентилируемый тормозной диск 1 может быть погружен в ванну для обработки погружением с тем результатом, что внутренние поверхности взаимно противоположных опорных дисков 11 и 12, а также ребра 13 также покрываются эмалью.
Также можно, чтобы тормозной диск 1 имел другие эмалевые покрытия. Таким образом, предпочтительно можно выбирать покрытие на фрикционных поверхностях 7 и 8, которое имеет требуемые коэффициенты трения, таким образом, гарантируя, что сохраняется функция тормозного диска 1. На поверхностях вне требуемых для замедления транспортного средства, тормозной диск может иметь эмалевое покрытие, которое, например, имеет сигнализирующие эффекты в форме цветов, которые светятся, даже в темноте. Также полностью совместимо с изобретением снабжать фрикционные поверхности соответствующим эмалевым покрытием, которое обладает сигнализирующим эффектом.
Во всех случаях, тормозной диск должен предварительно обрабатываться машинной обработкой по меньшей мере в некоторой области или областях перед нанесением эмалевого покрытия 10. Полезно осуществлять машинную обработку области тормозного диска 1, которая также должна быть покрыта.
После нанесения эмалевого покрытия 10, предусмотрены высушивание и обжиг. В качестве возможного варианта, также может выполняться операция механической чистовой машинной обработки.
СПИСОК СИМВОЛОВ ССЫЛКИ
1 тормозной диск
2 основной корпус
3 тормозная шайба
4 проем
5 выступ/головка диска
6 сквозное отверстие
7 первая поверхность торможения/фрикционная поверхность
8 вторая поверхность торможения/фрикционная поверхность
9 поверхность
10 эмалевое покрытие
11 опорный диск
12 опорный диск
13 ребра
14 кромка
R радиус
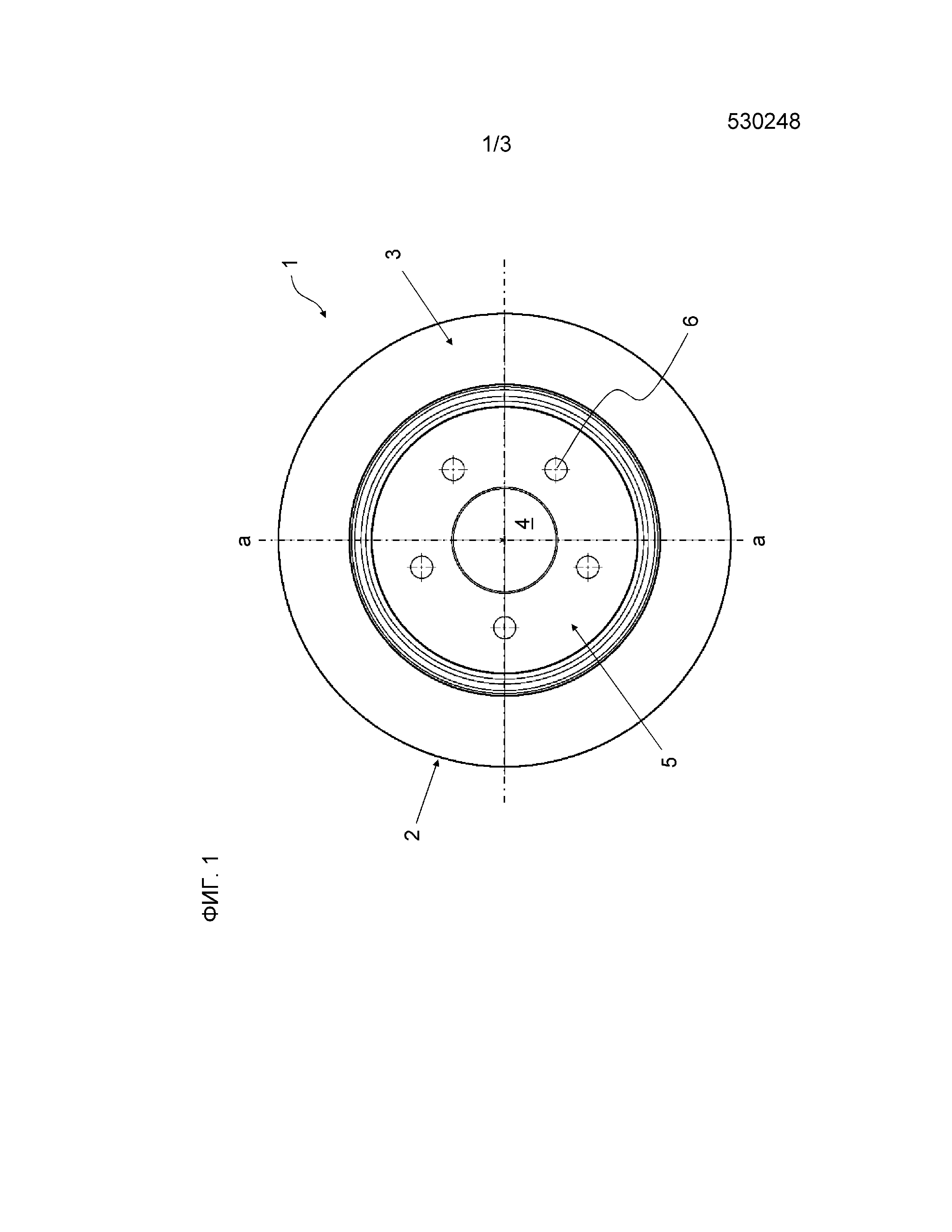
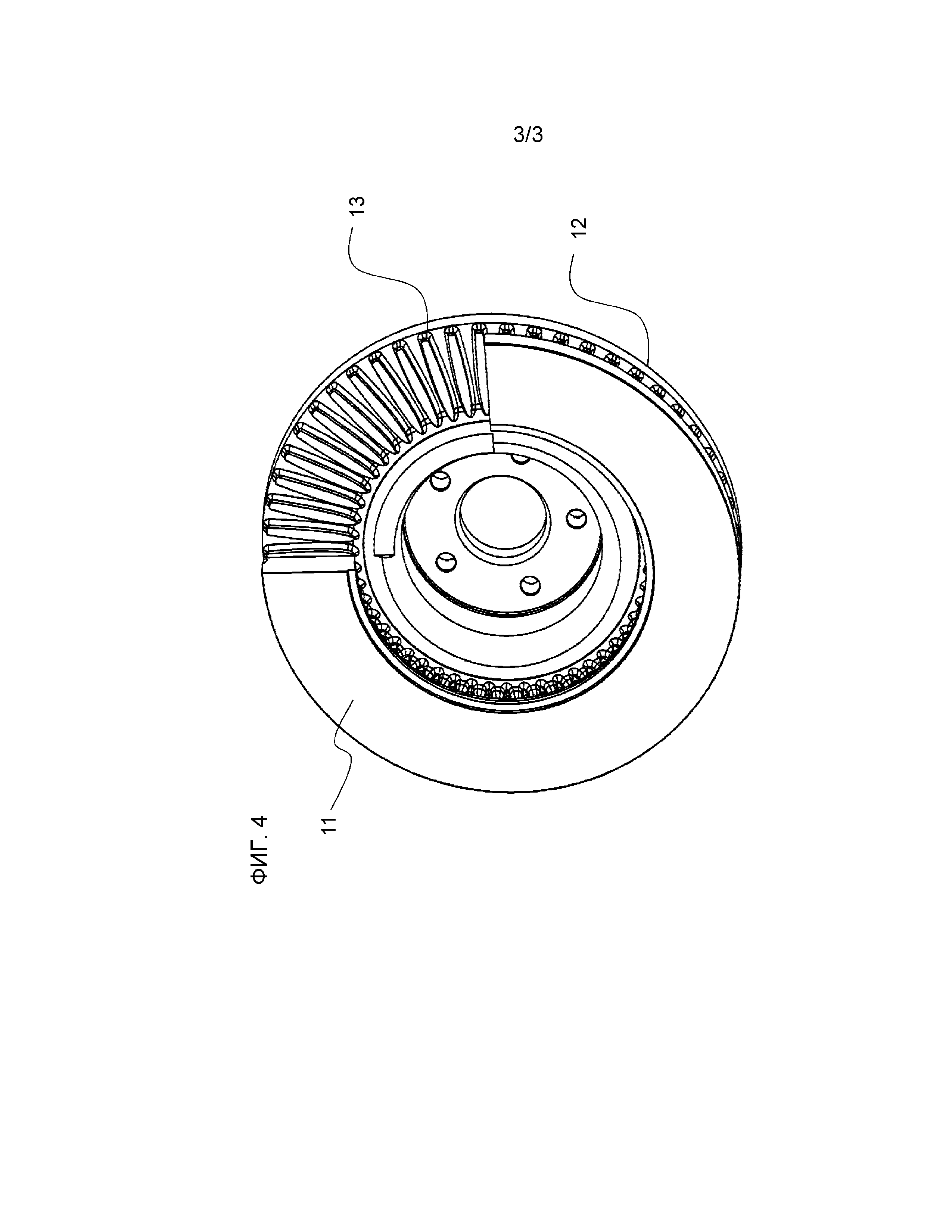
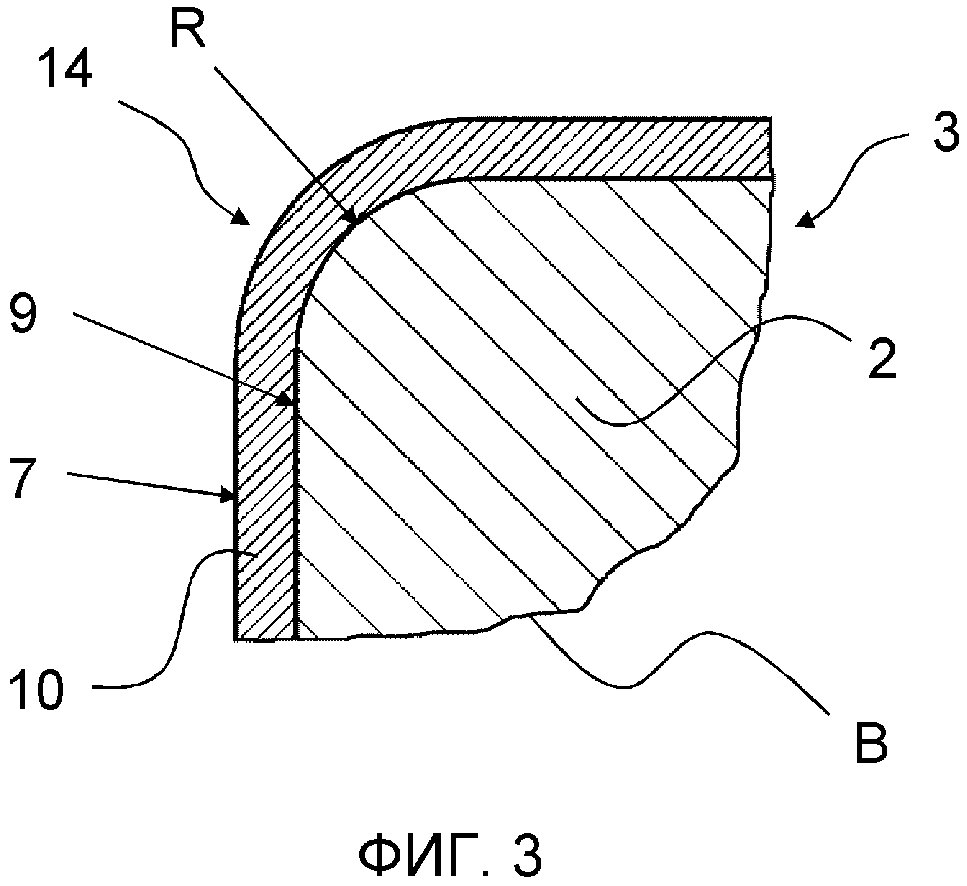
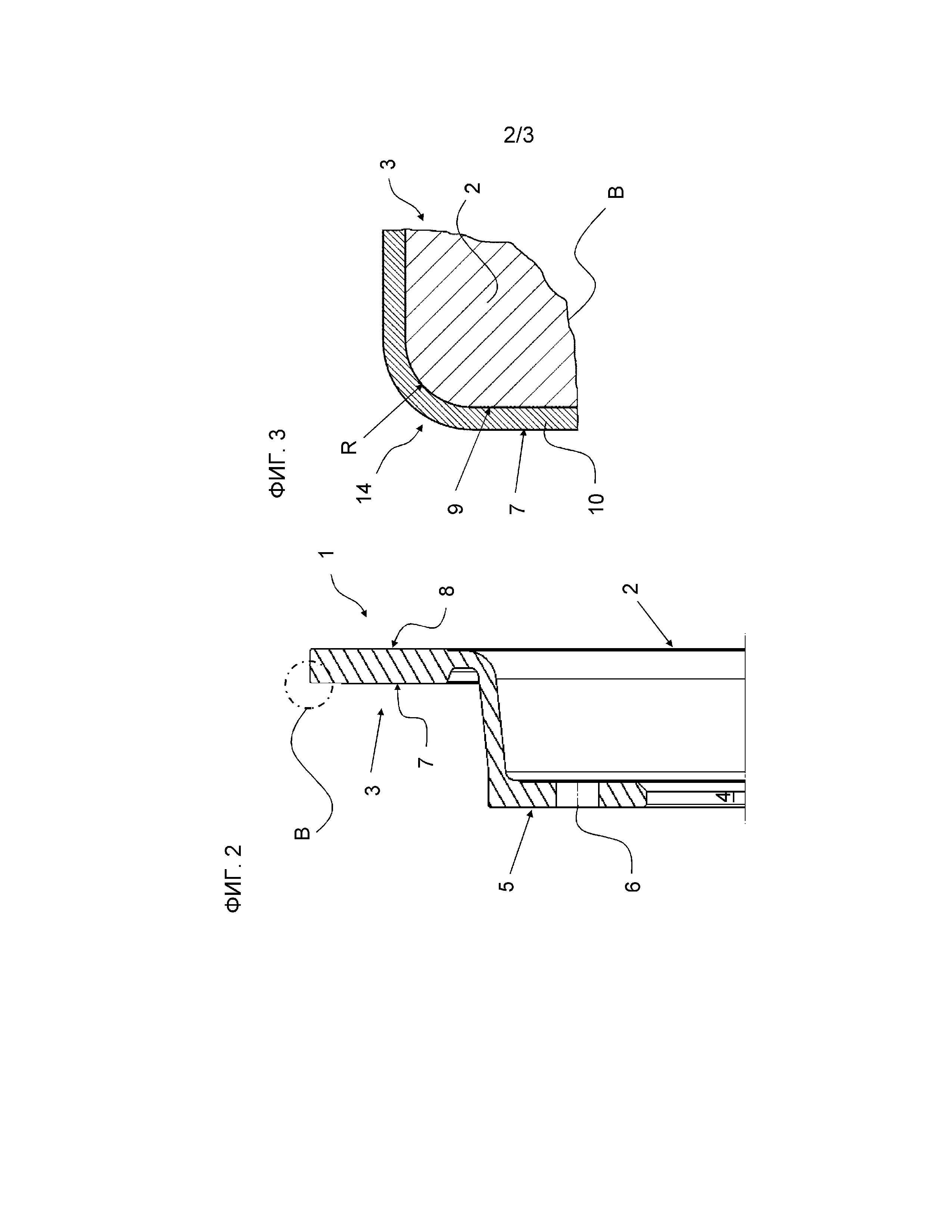
Производство тормозных дисков – есть ли предел совершенству?
На рисунке 3 показаны литники, которые лежат в основе данных таблицы 3. Прокладка литниково-питающих систем для производства при использовании как единичной, так и двойной подачи, схожи. Основные различия сосредоточены в поперечных полостях литниково-питающих систем, которые достаточно трудно распознать в визуально-графическом отображении (рисунок 3). При увеличении времени заливки посредством двойной подачи с 10,4 до 13,3 секунд появилась возможность сократить скорость заливки с 4,5 до 3,5 кг/с. Тем самым стало возможным применение литниковой чаши №4 вместо №5. Длина литниковых каналов и их поперечные размеры, а также размеры питателей тоже уменьшились. Стало возможным увеличение выхода на 3,5%. Одновременно производительность формовки увеличилась с 290 до 322 форм в час. При этом существует возможность сохранения скорости заливки 4,5 кг/с при выходе годного литья 79% — производительность формовки с двойной подачей в таком случае увеличивается до 370 форм в час.
Необходимо отметить, что если характер дефектов отливок принципиально различается в зависимости от технологии вертикальной либо горизонтальной формовки, доля брака примерно одинаковая. Если при вертикальной формовке проявляется микропористость, то при горизонтальной формовке – это усадочные раковины. Каждому опытному литейщику знакомы эти проблемы из личного опыта работы по той или иной технологии формовки, и он знает пути их устранения.
После обработки и установки тормозных дисков на автомобиль невозможно распознать различия в технологии изготовления. Один ведущий автомобильный концерн подтвердил, что на протяжении длительной эксплуатации не было выявлено качественных различий тормозных дисков, произведённых на вертикальной либо горизонтальной формовке.
Один из часто упоминаемых недостатков формовочных линий DISAMATIC — это возникающее ферростатическое давление во время заливки формы. При этом вертикальные формовочные линии с высотой кома от 700 до 800 мм. представлены на литейных производствах уже с 1977 года. В 1979 году на литейном заводе, производящем тормозные диски, была введена в эксплуатацию первая линия DISAMATIC 2070-A с размерами кома 700 x 950 мм. Опыт решения таких проблем имеется уже на протяжении 35 лет. Конструкция литниково-питающей системы позволяет сократить влияние ферростатического давления. Высота кома свыше 800 мм. не рекомендуется производителем формовочных линий для производства тормозных дисков.
Двустороннее уплотнение литейной формы над модельной плитой обеспечивает максимальную твёрдость формы на её поверхности, однако ближе к центру кома формы эта твёрдость снижается. Это естественное преимущество процесса вертикальной формовки на горизонтальной опочной формовочной линии может достигаться посредством дополнительных затрат на интегрирование вторичной наполнительной рамки на опоре модельной плиты. Вторичная наполнительная рамка используется для уплотнения формы в приграничных областях.
В опочных линиях необходимо оборудование для соединения нижней и верхней полуформ. При этом возникает опасение смещения при механических колебаниях в процессе сборки. Необходимо постоянно контролировать износ штырей и втулок во всех опоках. В вертикальной линии полученная форма напротив перемещается при помощи модельной плиты из формовочной камеры и соединяется сразу с предшествующей формой. Исключение смещения формы, ровно как и более высокие затраты на очистку в последующих процессах значительно сокращается. Для отвода газов из формы во время заливки в вертикальном процессе достаточно выпоров, смонтированных на модельной плите, которые сообщаются с верхней поверхностью формы. Повреждение формы при выполнении наколов либо сверлении выпоров также исключается.
Изготовление тормозных дисков или почему этого не стоит пробовать делать. — Ремзона — Клуб владельцев Honda Transalp — Статьи
Личный опыт производства тормозных дисков и те проблемы с которыми мне пришлось столкнуться при решение данной задачи.
Каждый, наверное, хоть раз задавался вопросом: из чего жесделаны эти волшебные тормозные диски (наверняка космические технологии и
прочее) и почему же они так дорого стоят… с виду же обычные железяки! Вот и у
меня 2014 году встал такой вопрос, когда у меня закончился задний диск на
Африке. Уверенный в своих силах (высшее техническое образование) я активно
принялся решать данную задачу веря в то, что делаю общенародное благо и
множество людей (глупцов) перестанут переплачивать за эти несчастные железяки.
Я расписал план решения проблемы, это же элементарно!)
1) Определение материала
2) Подготовка конструкторской документации (чертеж)
3) Подготовка технической документации
4) Производство
5) Естественно мировое господство и всеобщая уважуха за решение столь наболевшей проблемы)))
Хочу сказать то, что у многих людей почему-то все проблемыначинаются именно в первом пункте. Для меня это как-то вообще была, по-моему,
самая простая задача. Так, что тем, у кого возникла в нем проблема может и
вообще не стоит этим заниматься, дальше то все гораздо сложнее… Скажу забавы
ради, что множество кустарных производителей тормозных дисков в нашей
необъятной делают их из абсолютно другого
материала причем они даже не скрывают, что не знают из какого сделаны
оригиналы! И когда я их спрашивал (я нашел около 5 «кустарников») про материал
они ОЧЕНЬ сильно обижались, что я им не говорил его! При этом некоторые из них
занимаются производством более 5 лет! Так вот, вернемся к нашим проблемам.
Сказано-сделано. Через 5 дней оригинальный тормозной диск хонда (с ним она
приехала из японии) лежал на столе в материаловедческой лаборатории завода
авиационных двигателей. Ровно 5 мин (может и меньше) потребовалось эксперту
чтобы определить марку стали (Это уже подсказка))) ). Оказалось, все на
удивление просто, и никаких космических технологий, и это логично ведь они
появились в далеких 70 если не раньше.
Второй пункт был уже для меня по сложнее, так как, на заводе
нельзя было сказать: «Вась тут подрежь, там шлифани, а тут надо отпуск сделать,
да и с параллельностью не накосяч». В течении 2 месяцев мной лично делался
чертеж тормозного диска (наверное, сейчас кто-то посмеется, но я не чертил с
института…) В результате кропотливой работы дома по вечерам чертеж в формате
который можно было бы передать на производство был готов.
(за чертеж строго не судите, возможно это одна из первых версий, давно все таки дело было…)
С третьим пунктом мне помогала жена (огромное ей спасибо за
долгую, БЕСПЛАТНУЮ и кропотливую работу) имея диплом инженера технолога. По
мимо материала из лаборатории дали данные о физ свойствах стали. Мало, наверное,
кто знает (да и я сам не знал), что конкретные физ свойства можно получить
ТОЛЬКО при определенной обработке материала, причем все это есть в
справочниках. Покопашись несколько вечеров в справочниках по технологической
обработке сталей и их свойств, было определено как именно надо ее обрабатывать
на 100%. Сразу говорю, если отступить от технологии вы этих свойств не
получите!!! Это так сказать был третий этап продолжительностью еще месяца два
(а то ведь многие думают, что за один вечер все делается), но он был интересный
и мы его совместно преодолели. В результате у нас лежала технологическая
документация для серийного производства на заводе, где было прописано вплоть до
марки станка и резца, которым надо было делать и как!!
Технологию выкладывать не стану, так как она написана под определенный парк станков.
А теперь самое интересное, мы подошли к самому производству,
вот тут-то вы и поймете, почему я такой не хороший не озвучиваю Вам таким
прекрасным эту волшебную формулу счастья. Скажу сразу, на авиационном заводе,
для меня изготовили партию из 24 штук дисков на Африку, но к сожалению
(вашему), а к моей радости моя жена уже ушла в декрет (выйдет- сразу
разбогатеем) и они остались там. Но я на этом не остановился, я начал
обзванивать всякие заводы и конторы, которые занимались металлообработкой.
Какого же было моё удивление, когда при разговоре с менеджерами в 90% случаев
при произношении слова «тормозные диски» они просто сразу клали трубку, ну
иногда еще вежливо посылали… Я просто бился в негодовании, что за темные люди,
ведь я все сделал по уму! Ну да ладно, в результате упорных трудов желанный
исполнитель был найден. И тут начались переговоры…
— Вам сколько дисков надо?
— Да думаю штук 10.
-Эээ, тогда со своим материалом.
— Хорошо!
Вот тут-то и оказалось собственно говоря самая, наверное,
большая проблема. Материал из которого делаются диски имеет определённые формы
поставки (и они между прочим гостированны, то есть можно забыть о том, чтобы
прийти на завод и сказать, а дайте мне лист 5,2 мм (ведь есть либо 5 либо 6,
один велик второй мал! А шлифовка самый дорогой процесс!), да и на заказ один
делать никто не будет) и размеры (мне удалось лишь найти 6х3 метра, а как вы
повезете такой лист на завод, как погрузите?)!!! В результате пришел к тому,
что пусть листом занимается сам изготовитель, у него есть поставщики пусть и
закажет ему и привезут.
— Здравствуйте, а сколько стоит лист у вас?
— Минуточку… 83000 руб 3х6 (меньше их не бывает, и
минимальная поставка один лист, причем на базе цена такая же!) (цены 2014 года)
— Хорошо, можете мне сделать из 10 дисков, а потом еще
скажем 20?
— Нет, если мы установим лист на станок, то мы его снимать
уже не будем, надо резать до конца.
— Ммм, а можно нарезать диски разного диаметра и размеров?
— Нет, нам это не удобно, максимум два типоразмера на один
лист.
Вкратце, что бы вы поняли, изготовление одного диска
примерно 2200 руб (цены 2014) + материал. Итого партия из 100 штук (примерно,
то есть вы их до старости лет не продадите!) обойдется вам в 300 000 руб!
И да, материал из которого сделаны диски на заводах по закромам не валяется,
тем более в той форме что нам надо! Не надо быть глупцом, чтобы понять, что 300
штук я не нашел…
Пункт 5 своего плана я естественно не выполнил, и даже
наоборот в некоторых кругах меня считают плохим человеком, вот гад – знает, а
не говорит.
Как вы видите первый пункт был самый простой, при всем
уважении к читающим (может среди вас есть родственники директора
Уралвагонзавода конечно, но думаю если и есть, то им это точно не интересно)
если Вы не прошли первый пункт, то может Вам и не стоит начинать этим
заниматься, потому как дальше будет то сложнее. Просто не хочется мне брать
такую ответственность на себя, крайний то я буду (мол это он сказал! я так
сделал, а потом хана) Так что пусть данная информация просто отсутствует в
интернете, а тот, кто захочет пройти мой путь, его же все равно не
остановить))) Уверен, что входе работ он придет к тому же выводу.
Основной вывод который мне бы хотелось, чтобы вы почерпнули из вышенаписанного, это то, что тормозной диск не может априори стоить 2000 руб (если вы конечно не покупаете их с завода тысячами) но и 12 000, и то что не стоит с этим экспериментировать, так большой экономии не выйдет, а вот последствия могут быть различными.
PS
На самом деле я не остановился на этом, была найдена контора в Китае ( https://vk.com/tarazon ) которые делает диски
не хуже оригинала (естественно я тоже их носил в лабораторию) и при их цене и
качестве (а качества можно добиться только при серийном производстве) смысла
вкладываться в производство в России — нет. (См пункт 4, если вы конечно не
олигарх, тогда вы правда вряд ли читаете эту статью)
Всем удачи, надеюсь никого не обидел! Извиняюсь за много
букв! (Так на вскидку описанный процесс у меня занял около года.) Надеюсь вам это все пригодиться.
Как производят тормозные диски для премиум-брендов: изучаем завод компании Zimmermann
Германия — Мекка автомобильной индустрии. Кажется, здесь нет области или земли, где не работала бы компания, так или иначе связанная с автопроизводством. Одна из таких — немецкий производитель тормозных систем Zimmermann, который предлагает альтернативные решения для премиальных немецких производителей Mercedes, BMW, Porsche и др. Журнал «Движок» лично убедился в высоком уровне немецкого производства, приехав на завод компании в городе Зинсхайм на Skoda Kodiaq.
Напомним, что компания Zimmermann появилась в 1960‑х годах прошлого века неподалеку от Штутгарта, а потому быстро наладила сотрудничество с компанией MercedesBenz. Чуть позже, благодаря ответственному подходу и неизменному качеству продукции, сотрудничество распространилось на все немецкие автомобильные бренды. Правда, затем автогиганты начали диктовать поставщику свои условия, которые не соответствовали бизнес-стратегии Zimmermann. В итоге компания приняла решение сосредоточиться на сегменте aftermarket, где имела полную самостоятельность и свободу действий.
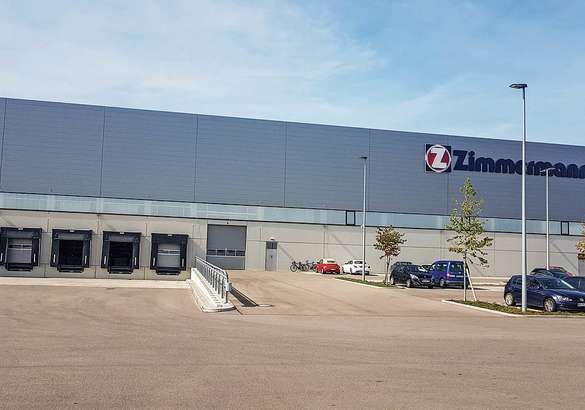
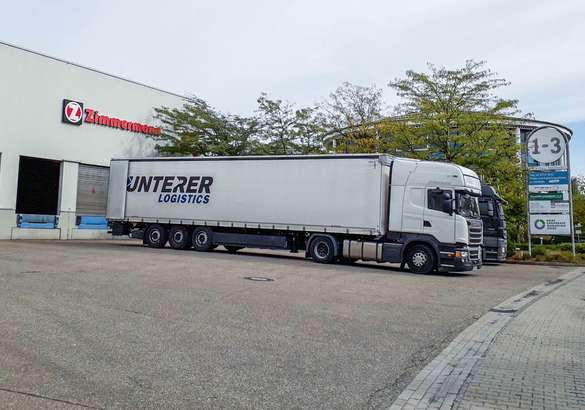
Однако годы взаимодействия с такими брендами, как Mercedes, BMW, Audi и Porsche, задали соответствующую технологическую планку. Потому на сегодняшний день производитель занят выпуском компонентов, которые как минимум не уступают заводским деталям, а в большинстве случаев превосходят их по качеству и характеристикам.

Основным видом продукции Zimmermann являются тормозные диски. Кроме того, в каталоге присутствуют тормозные барабаны, колодки и восстановленные оригинальные тормозные суппорты. Всего более 4 тыс. позиций, которые охватывают 96% европейских автопроизводителей, а также часть корейских, японских и американских автомобильных брендов. Более 65% продукции идет на экспорт.
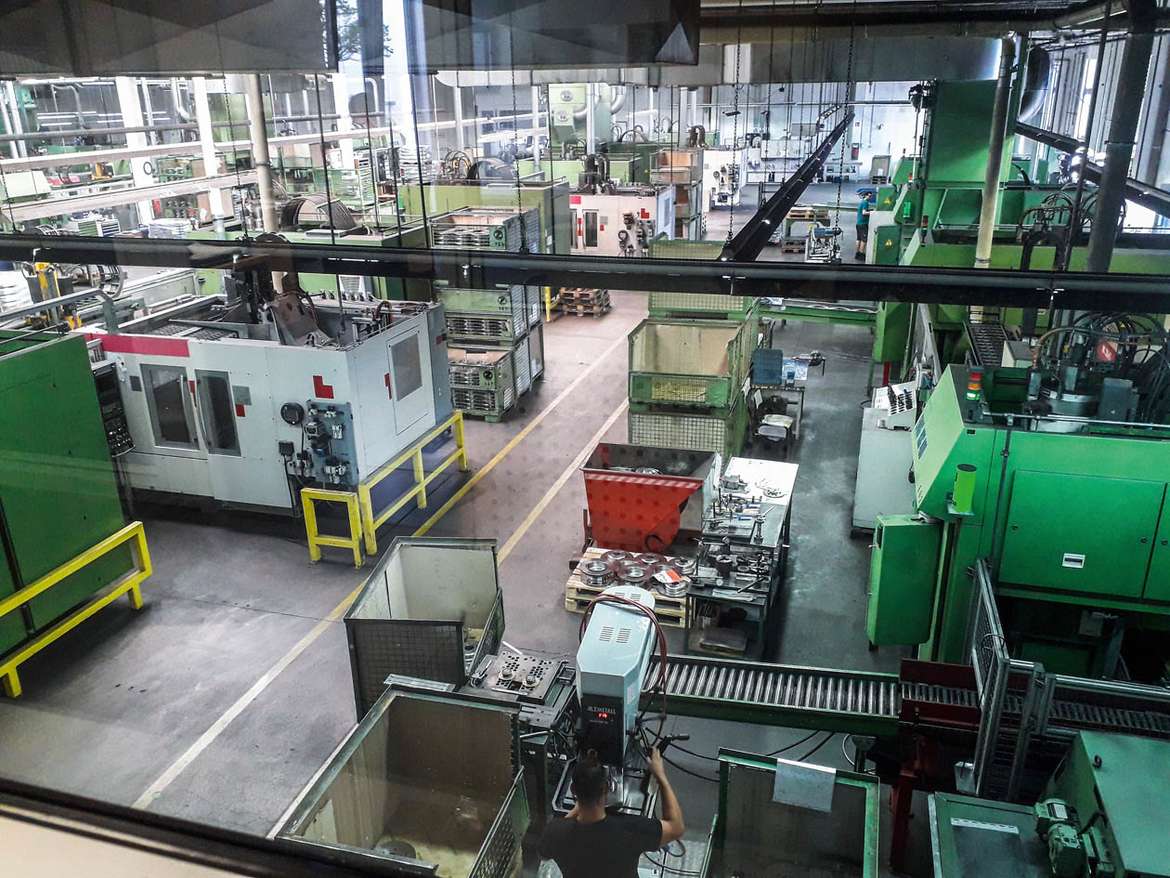
Компания Zimmermann целиком расположена в городе Зинсхайм. Здесь находятся завод, склад и логистический центр, а также штабквартира со всей администрацией. Благодаря тому, что предприятие представляет собой единый организм, компании несколько десятилетий удается держать стабильно высокий уровень качества
Процесс начинается в лаборатории компании, где инженеры на специальном оборудовании готовят технические образцы для производства. В первую очередь берется оригинальный тормозной диск, с которого до последнего микрона снимаются все мерки. После чего создается серия прототипов с разными свойствами и характеристиками, которые в лаборатории начинают проходить полный цикл испытаний согласно всем имеющимся сертификатам соответствия автопроизводителя.
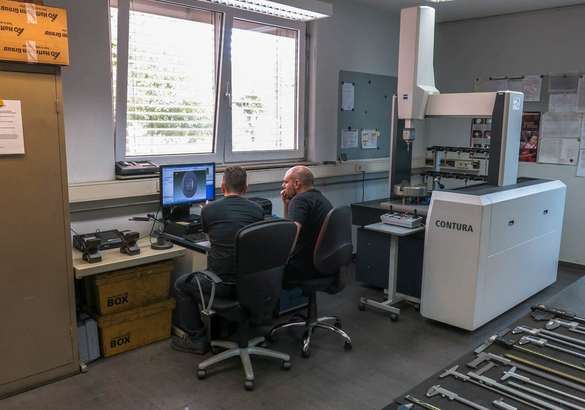
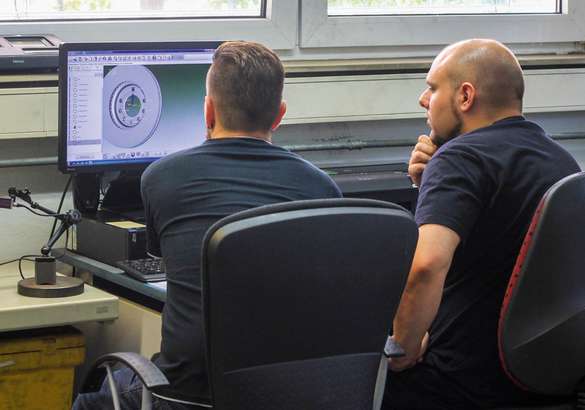
В этих спецификациях указаны всевозможные параметры, которым должен соответствовать тормозной диск, — от температуры нагрева и износа до времени окончательного разрушения. Из прототипов выбирается тот диск, который по результатам тестов имеет характеристики, превосходящие исходные параметры оригинальной продукции. После чего выпускается опытная партия, из которой случайным образом выбирается и отправляется на повторный цикл испытаний еще один тормозной диск.

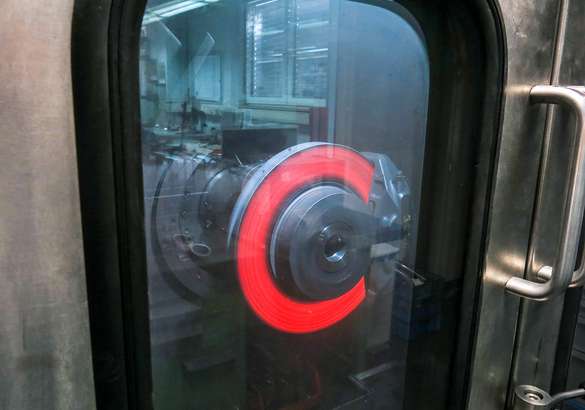
На испытательном стенде прототип диска Zimmermann совмещается с оригинальным суппортом и оригинальными колодками, после чего проходит серия циклов имитации всех возможных вариантов торможения, а также программа имитации условий частичного или полного разрушения диска
Одной из важнейших основ качества продукции Zimmermann называет уровень литья заготовок. Самостоятельно металлопрокатом компания не занимается, а заказывает основу у тех же поставщиков, которые работают с производителем оригинальной продукции. Заготовки, конечно, тоже проверяются. Существует порядка 45 качеств исходного материала, которые должны соответствовать заданным параметрам. Большая часть используемого сырья производится в самой Германии (55%) или странах Западной Европы. Малейшее несоответствие параметров — и сырье тут же бракуется.
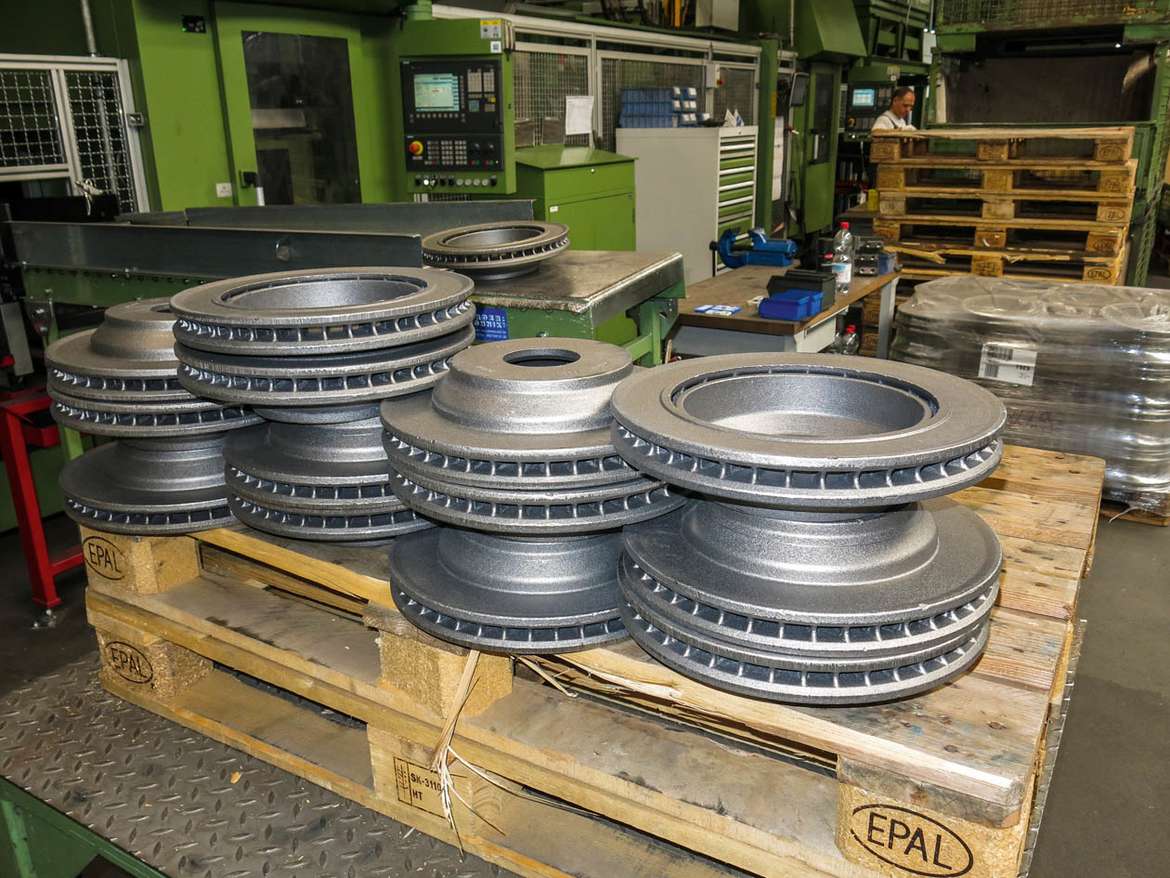
После всех проведенных испытаний заготовка попадает непосредственно в производственные цеха, которые делятся на линии по выпуску разных видов дисков: обычных, перфорированных или составных.
Обычные, перфорированные, составные
В процессе обработки заготовка тормозного диска теряет 20–25% материала, или до 10 кг веса. В зависимости от того, какой необходимо выпустить диск, используется разное оборудование. Например, для производства обычного диска требуется одна производственная машина, а для производства перфорированного уже две. То есть происходит два этапа обработки с процессом переворачивания заготовки. Собственно, именно поэтому перфорированные диски всегда дороже.
Кстати, уровень перфорации также влияет на производительность и цену. Например, тормозные диски Porsche имеют 160 отверстий, а потому их производство дольше и энергозатратнее.

Последним этапом перед упаковкой является покрытие дисков Zimmermann специальной краской с алюминием в составе, что защищает диски при транспортировке и эксплуатации. Она автоматически стирается с тормозных поверхностей при использовании и не требует предварительного удаления.
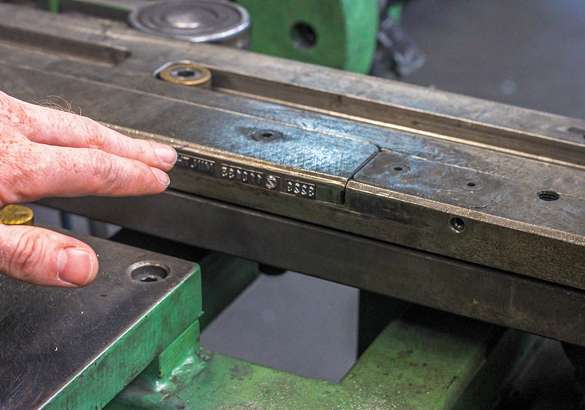
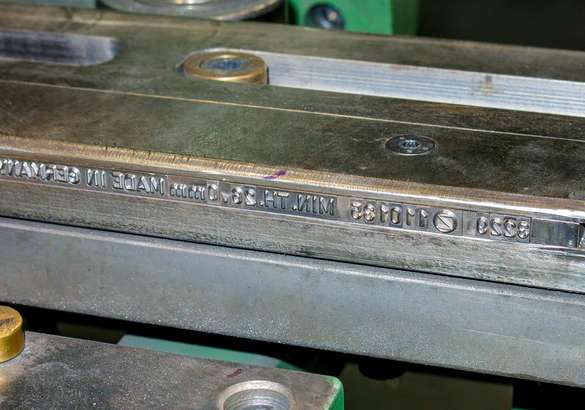
Каждый тормозной диск маркируется. Первые четыре цифры — это номер, указывающий, для какого автомобиля он выпущен, дальше — номер заводской смены, то есть кто конкретно и когда его сделал, и в конце — минимально допустимая толщина
На заводе Zimmermann высокий уровень автоматизации производства, однако процесс организован по-другому, нежели у конвейерных поставщиков, коим компания сама когда-то была. Главным отличием является то, что OEM-поставщик заточен под выпуск малого количества видов продукции, но делаются они огромными партиями. Zimmermann, наоборот, имеет возможность выпускать огромное количество вариантов и видов тормозных дисков, но не очень большими объемами, а иногда и мелкосерийными партиями вплоть до 500 штук для эксклюзивных авто. Таким образом, сделана ставка на гибкость производства, когда компания может оперативно перестроиться под любого партнера и быстро реагировать на появление на рынке новых моделей автомобилей.
У компании Zimmermann мизерный процент брака. Где-то 1,5% отсеивается на этапе заготовок, и еще 0,07% отбраковывается уже в виде готовой продукции
Отдельная линия отведена производству составных тормозных дисков. Их принципиальное отличие заключается в использовании разных материалов для разных частей диска: стальная или алюминиевая ступица специальным образом соединяется с чугунной тормозной поверхностью.
Преимуществ у таких дисков два. Во‑первых, составной диск заметно легче, что дает выигрыш как по весу авто в целом, так и отдельно по неподрессоренным массам, которые влияют и на работу подвески. Второе преимущество заключается в лучшей термоустойчивости и общем распределении тепла, благодаря чему улучшаются непосредственно тормозные свойства.
Подобные диски, например, штатно устанавливаются на Mercedes-Benz S-class и BMW поколения F. Причем в дисках для Mercedes Zimmermann использует свою запатентованную разработку, которая отличается от мерседесовской именно системой крепления ступицы к тормозному диску.
Отдельный цех на заводе отдан под производство тормозных колодок. Идея дополнить предложения этой группой товаров появилась в 2012 году. Сначала был создан исследовательский центр, а затем и небольшое производство, главным образом для BMW и Porsche.
Его цель — реализовать конструкторские разработки, понять и наладить процесс производства в принципе, а также предложить клиентам комплексный продукт, максимально подходящий его потребностям.

У компании Zimmermann несколько линеек продукции, каждая из которых отвечает своим задачам. Серия Standart максимально соответствует оригиналу. Серия Sport — для легкого тюнинга: это диски с улучшенными свойствами (перфорированные и слотированные), установка которых не требует переделки тормозной системы.
Новинка в этой группе — слотированные диски серии Black Z с черным антикоррозионным покрытием и насечками в виде буквы Z. Эти диски испытывались больше года на гоночном болиде Porsche Cayman S на треке Нюрбургринг и получили самые высокие оценки пилотов суперкара, которые неоднократно занимали там призовые места.
На вершине гаммы — двусоставные тормозные диски серий Formula Z, Formula F и Formula S, объединенные в линейку FusionZ
Каков итог?
Принципиально что-то менять в успешном бизнесе и сильных позициях на рынке Zimmermann не планирует. Согласно тенденциям компания будет внедрять экологические методы производства, а также оптимизировать бизнеспроцессы. По словам представителя руководства компании Райнера Мерца, основная задача — соответствовать тому автопарку, который сегодня представлен на рынке. Обеспечение текущих потребностей для клиентов куда важнее, чем рассуждения о будущих разработках. А клиент, как говорится, всегда прав.

Конструкция и виды тормозных дисков
Самые распространенные на сегодняшний день автомобильные тормозные системы – дисковые тормоза. Из этого следует, что главным элементом тормоза такого типа является тормозной диск, к которому прикладывается усилие исполнительного механизма. Поскольку существующие автомобильные тормоза используют трение в качестве основного принципа действия, между диском и тормозным механизмом находится колодка, покрытая слоем фрикционного материала.
Как известно, росту эффективности любых тормозов препятствует температура в паре трения. Чем интенсивнее автомобиль тормозит, тем больше выделяется тепла и тем больше нагреваются детали тормозного механизма. Для обычной тормозной колодки это приводит к потере фрикционных свойств за счет снижения коэффициента трения. Можно пойти дальше и обнаружить, что тепло от колодки передается не только воздуху, но и собственно исполнительному тормозному механизму – скобе (суппорту), нагретые поршни которой бывают способны довести тормозную жидкость до кипения. Это может привести к образованию пузырьков воздуха в жидкости и, как следствие, потере ею упругих свойств и «провалу» тормозной педали. Естественно, ни о какой эффективности не может быть и речи, остановиться бы, перевести дух и подумать, что можно сделать. Самым логичным будет повысить температуру кипения тормозной жидкости и сделать колодки, способные не снижать коэффициент трения с ростом температуры. Именно так и поступили конструкторы тормозных систем, и сейчас есть колодки, работающие в диапазоне от 200 градусов и выше. Однако тема колодок и жидкостей еще дождется своего часа, а что же происходит с дисками?
Диск также нагревается, что приводит к нарушению формы его рабочей поверхности, ее короблению, следствием чего становится осевое биение диска, передаваемое на руль и тормозную педаль. Для начала рассмотрим причину деформации диска под действием температуры. Как правило, обычный тормозной диск представляет собой обод, выполненный в одно целое со ступицей П-образного сечения. При нагреве диск, напоминающий в разрезе шляпу, условно стремится вывернуться «наизнанку» за счет разницы длин наружного и внутреннего контуров. У внутреннего она больше, следовательно, и линейное тепловое расширение также больше. Это приводит к тому, что у «шляпы» приподнимаются поля. Именно череда таких подъемов и опусканий при остывании и приводит к деформации диска. Чтобы уменьшить такой эффект, у дисков в местах соединений обода со ступицей с наружной стороны делаются галтели или проводятся другие мероприятия, увеличивающие длину наружного контура. А что, если сделать диск более массивным, тогда он уж точно не покоробится. Хорошая идея, только вообразите, какая будет неподрессоренная масса у такого автомобиля, а наличие дополнительного маховика на каждом колесе сделает торможение проблематичным, добавив еще необходимость «гасить» их инерцию. К тому же проблема рассеивания тепла осталась. Так на сцену вышел диск с внутренней вентиляцией или просто вентилируемый. Он сразу позволил повысить эффективность торможения за счет более благоприятных температурных режимов паре трения. У вентилируемого диска существенно увеличена поверхность, с которой он отдает тепло окружающей среде. А если подвести дополнительный охлаждающий воздух к тормозному диску, то о перегреве тормозов можно даже забыть. Вентилируемый тормозной диск также уменьшает температурную нагрузку на ступичный подшипник.

Увеличению поверхности рассеивания тепла способствует и перфорация дисков, при которой обод насчитывает не один десяток сквозных отверстий с зенковкой. Проделанные по всей рабочей плоскости диска сквозные отверстия снижают вес диска, способствуют более эффективному снижению его температуры при работе (что снижает риск коробления), удаляют газы, образующиеся при трении колодок о диск. Также перфорация не допускает «всплытия» тормозной колодки при попадании воды на рабочую поверхность диска в дождь или при проезде через лужи. Оказавшаяся на пути колодки вода выдавливается внутрь диска, откуда она выбрасывается наружу под действием центробежной силы. Вот здесь и кроется опасность для перфорированных дисков. Попавшая вода на раскаленный иногда тормозной диск может вызвать катастрофические последствия для его целостности, он может потрескаться и даже лопнуть. Отверстия станут дополнительными концентраторами напряжений и начальными точками этих самых трещин. Поэтому заявления о повышенной эффективности перфорированных дисков часто следует рассматривать как рекламный ход.
Однако встречаются серийные автомобили, у которых такие диски стоят и хорошо себя чувствуют за все время эксплуатации, подвергаясь замене только по причине износа. Такую картину можно наблюдать, в частности, на автомобилях Ferrari и Porsche. Все дело в том, что диаметр отверстий не велик, их расположение сочетается с конфигурацией внутренних лопаток диска, а сам диск, как правило толстостенный и большого диаметра. Это снижает риск образования трещин, однако более правильным решением являются канавки на рабочей поверхности диска. Кроме воды, канавки отводят газообразные продукты “жизнедеятельности” колодки и продукты износа. Канавки бывают направленными в зависимости от вращения диска или симметричными, что позволяет ставить диск на левую и правую стороны автомобиля. Это относится и к лопаткам внутри диска. Обычный вентилируемый диск имеет радиально расположенные лопатки, что делает левый и правый тормозные диски одинаковыми, но существуют диски с наклоненными лопатками для лучшего удаления разогретого воздуха. При этом левый диск является зеркальной копией правого и наоборот.
Указав все эти достоинства канавок, нельзя не сказать и о том, зачем они изначально были разработаны. Опять же, автоспорт с его повышенными нагрузками на тормоза потребовал эффективной очистки тормозных колодок. Дело в том, что при работе на больших нагрузках тормозные колодки очень быстро покрываются тонким слоем нагара – выгоревшего и отработанного фрикционного материала. Если его не снять принудительно, колодка превращается в скользкую лыжу. Канавки, шлицы практически срезают этот отработанный слой, обновляя колодку. Это позволяет поддерживать работоспособность колодок на протяжении всей гонки. Учитывая все вышесказанное, можно считать, что для обычных городских автомобилей тормозные диски со шлицами, конечно, являются предметом гордости владельца, но одновременно причиной более частой смены тормозных колодок.

Теперь мы добрались до высшей лиги тормозных дисков – вентилируемых сборных. Конечно, бывают и цельные диски с направленными лопатками, но их не так много. Это объясняется необходимостью иметь сложные оснастки для левого и правого диска, на что не каждый производитель может пойти. В результате диск с одной стороны выбрасывает воздух наружу, а с другой – захватывает его и пытается выдавить из центра внутрь колесной арки. Разборные диски изначально делятся на левые и правые и имеют крепежный фланец для ступицы, которая делается, как правило, из высококачественного авиационного алюминия. Такая конструкция позволяет еще больше рассеивать тепла, что благоприятно сказывается на эффективности тормозов и теплонагруженности подшипников ступицы. Понятно, что такой диск более легкий, чем его цельный аналог. Здесь тоже присутствуют подводные камни. Самый опасный – разница коэффициентов термической деформации материалов диска и ступицы. Для решения этой проблемы делают прорези на ступице, но самым эффективным способом борьбы с этим явлением можно назвать так называемые плавающие диски. Их суть – отсутствие жесткой связи между диском и ступицей, при этом диск может двигаться относительно ступицы обычно в осевом направлении в пределах нескольких десятых долей миллиметра. Плавающие диски обладают существенным недостатком – они боятся грязи, которая может лишить их подвижности, поэтому они главным образом применяются в кольцевом автоспорте.
Материал тормозных дисков
Чаще всего тормозные диски изготовляют из чугуна. Популярность этого материала объясняется хорошими фрикционными свойствами и невысокой стоимостью производства. Наряду с этими преимуществами, чугун имеет ряд существенных недостатков, которые ограничивают его использование в некоторых типах транспортных средств – спортивных машинах и мотоциклах. При регулярных интенсивных торможениях, вызывающих значительное повышение температуры (400 С и выше), возможно коробление диска, а если на его перегретую в таких режимах поверхность попадает вода, например, из лужи, чугунный диск покрывается сетью трещин и иногда даже рассыпается. Кроме того, такие диски очень тяжелые, и после длительных стоянок их рабочая поверхность покрывается коркой ржавчины. Чтобы избежать этих недостатков, диски, в большей степени мотоциклетные и значительно реже автомобильные, начали делать из «нержавейки». Более слабые фрикционные свойства этого материала компенсировали увеличением диаметра дисков и их рабочей поверхности. Для изготовления этой ответственной детали тормозной системы используют и обычную сталь, которая, как и «нержавейка», не столь чувствительна к перепадам температур и обладает несколько худшими фрикционными свойствами, чем чугун.
В 70-е годы на спортивные машины начали устанавливать тормозные диски из углепластика – карбоновые. Преодолев период роста, карбоновые тормоза оставили своих металлических коллег далеко позади. Посудите сами: вес тормозного диска из карбона на порядок меньше металлического, коэффициент трения на порядок выше, а рабочий диапазон, ограничивающийся на обычных тормозах 500-600 С, здесь простирается далеко за отметку в 1000 С. Карбоновые диски не коробятся, а снижение неподрессоренных и вращающихся масс положительно сказывается на ходовых качествах автомобиля. Тем не менее путь к обычным дорожным автомобилям таким тормозам пока заказан. Стоимость комплекта карбоновых тормозов может достигать стоимости нового автомобиля малого класса, а нормально работать они начинают только после хорошего прогрева: до этого коэффициент трения тормозов даже ниже обычных! Нельзя забывать и об удобстве управления замедлением: если с традиционными тормозами все просто и понятно, то здесь контролировать замедление сверхсложно. Фактически в обычных условиях карбоновые тормоза будут аналогом переключателя «ехать/стоять».

Более радужные перспективы в автомобилестроении имеют керамические тормоза. Они не имеют такого ошеломляющего коэффициента трения, как карбоновые, но обладают целым рядом преимуществ. У керамики гораздо больше возможностей, чем у металла или различных композитов. Этот материал отличается отличной устойчивостью к высоким температурам, высокой стойкостью к коррозии и износу, небольшой удельной массой и высокой прочностью. Но это еще не все. Керамические тормозные диски, в сравнению аналогичным деталями из серого чугуна легче на 50%. Вес, например, керамического тормозного диска PORSCHE 911 в два раза легче обычного, значит, меньше и неподрессоренные массы, а следовательно, и нагрузка на подвеску. Уменьшается и так называемый гироскопический эффект, когда вращающееся с большой скоростью тело сопротивляется смене направления вращения. Кроме того, применение керамики позволяет увеличить на 25% коэффициент трения, а заодно резко повысить эффективность торможения в горячем состоянии. Еще одно преимущество – невероятная долговечность. Керамические диски обычно не требуют замены на протяжении 300 000 км. К сожалению, есть и недостатки. Во-первых, холодные керамические диски хуже останавливают машину, чем холодные тормозные диски из металла. Во-вторых, керамика плохо работает при очень низких температурах. В третьих, такие диски при работе неприятно скрипят. И, наконец, в четвертых, цена у них ну просто непомерная.
Из какой стали делают тормозные диски
Тормозные колодки TRW
Зима предъявляет повышенные требования к тормозным свойствам автомобиля. В значительной степени тормозной путь на скользкой дороге зависит от выбора покрышек. И, разумеется, от эффективной работы тормозной системы. В последнем случае стоит уделить особое внимание такой важной части тормозной системы, как тормозные колодки. Отказ или неэффективная работа тормозов в самый неподходящий момент – это, пожалуй, самое худшее, что может произойти с водителем на дороге. В свою очередь, надежные тормозные колодки обеспечат спокойствие и надлежащую безопасность, будут служить верой и правдой до окончания установленного срока их эксплуатации. Чтобы не ошибиться в выборе этого элемента тормозной системы, необходимо побольше узнать о нем.
По большому счету, именно сопряжение тормозных дисков (барабанов) и колодок можно считать самым важным элементом тормозной системы, потому что именно эти элементы, взаимодействуя друг с другом, обеспечивают провоцируемое водителем замедление и остановку колеса. Гидравлическая часть тормозной системы только передает усилие с педали на тормозные механизмы и колодки, а ABS и другие технические достижения лишь призваны сделать процесс торможения максимально эффективным.
Здесь на первый план выходит вопрос материалов, которые используются для производства дисков и накладок. Большая часть тормозных дисков, как и барабанов, делается из чугуна. Этот сплав (железа с углеродом) используется в тормозной системе автомобиля не только потому, что имеет невысокую цену, но и потому, что он обладает лучшими фрикционными свойствами, чем, например, нержавеющая сталь, из которой делают диски для мотоциклов. При том, что масса мотоцикла меньше, чем автомобиля, а сами диски постоянно открыты для агрессивного воздействия окружающей среды, именно поэтому в производстве двухколесной техники применение материала, защищенного от коррозии, является оправданным.
Тормозные колодки TRW
В автопромышленности несколько другие условия эксплуатации и другие материалы. В частности, в автоспорте используют диски из углеволокна. Это легкий и весьма эффективный материал, имеющий как достоинства, так и недостатки. Карбоновые диски эффективно работают только при высоких температурах. Это означает, что применять их целесообразно только в случае агрессивного, спортивного вождения. В обычном городском режиме они просто не будут успевать прогреваться и, по сути, будут работать не так эффективно, как это необходимо. При этом, стоимость таких тормозных механизмов чрезвычайно высока. Диски из углеволокна – это вариант для «Формулы-1» и других элитных автогоночных чемпионатов и серий. Используются также диски из материалов на основе кремния, но они, пока что, также не получили широкого распространения, хотя, возможно, именно за ними будущее.
2011 Ferrari 458 Italia
. Фрикционные смеси можно разделить на асбестовые, безасбестовые и органические, от которых получили свои названия и соответствующие тормозные колодки. Асбест, используемый в качестве армирующего материала – это недорогой и вполне традиционный вариант, который применяют для изготовления обычных тормозных колодок. Безасбестовые тормозные колодки – это уже следующий этап развития технологий. В них в качестве армирующего материала используют стальную вату, медную или латунную стружку или полимерные материалы. Органические материалы, которые используют для изготовления тормозных колодок, показывают, на данный момент, наилучшие тормозные свойства, но их стоимость позволяет использовать такие накладки только в мире профессионального автоспорта.
И напоследок, об эксплуатации тормозов. Водитель всегда должен помнить о том, что менять тормозные колодки следует в сроки (в зависимости от пробега), указанные в руководстве на данную модель автомобиля. Обычно это происходит каждые 10-12 тыс. км пробега. Если вы сторонник агрессивной манеры езды, в этом случае проверять состояние тормозных накладок нужно регулярно. Если их толщина составляет или приближается к критической отметке (2 мм), колодки следует менять в обязательном порядке. Не дожидаясь неприятностей!
Источник 5koleso.ru
На первый взгляд тормозной диск представляет из себя подготовленный и хорошо обработанный кусок металла. Но это не так.
В действительности тормозные диски изготавливают из чугуна. А что такое чугун?
Чугун — это уже не просто металл, а определенный сплав металлов. Основа представляет собой сплав железа с углеродом, который добавляется в виде цементита и графита. Углерод необходим для придания твердости, хотя и снижает пластичность. Добавляют кремний, марганец, серу и фосфор.
Тут необходимо понимать основную задачу тормозных дисков и принцип их работы.
Тормозные колодки зажимают диск с двух сторон и тормозят движение. Визуально просто, но с точки зрения взаимодействия элементов тормозной системы дело обстоит сложнее. Принцип их действия — усилие сжатия и трение.
Там, где усиливается трение увеличивается температура, а температура увеличивается не только в паре колодка-диск, но и ситема — тормозная жидкость и далее.
Если мы посмотрим на конструкцию тормозного диска, то увидим, что он чем-то напоминает летающую тарелку. Перегрев или резкое охлаждение приводит к тому, что края этой «тарелки» то приподнимаются вверх, то опускаются вниз.
То есть рабочая поверхность деформируется и коробится.Снижается эффективность торможения и возникают различные биения, которые (в случае, если деформация все-таки происходит) мы обычно ощущаем на руле или педали тормоза.
Поэтому основная задача чугунного сплава из которого сотоит тормозной диск — это способность выдерживать высокие температуры и резкое охлаждение. Обладать твердостью и пластичностью.
Конечно, конструкция тормозного диска и всей системы в целом направлена на максимальный отвод тепла, как одной из главных проблем. Но это уже вопрос отдельного разговора и следующей статьи.
В дополнение прмерная структура тормозного диска в цифрах:
Для Чугуна с индексом G3000
Тип материала: НТ230
Усилие на разрыв: ob 230N/mm2
Твердость: HB187-241
Фосфидно евдектический сплав и цементит не более 3%
Структура: тонко слоистая со стальным отливом
С — 3.10-3.50
Si — 1.60-2.10
Mn — 0.60-1.00
P — 4 года Метки: состав тормозного диска
Источник www.drive2.ru
- Мото клуб.
- >Технический раздел
- >МотоЛикбез
- Просмотр новых публикаций
Тормозные диски мото Все о тормозных дисках мотоциклов
#1 Гость_Андрей_*
Типы тормозных дисков мотоциклов
Наиболее распространены два типа дисков. С плавающим ротором и жестко закрепленным. Большинство современных дорожных мотоциклов, оборудованы дисками с плавающим ротором. Эти диски состоят из двух частей — ротора (части непосредственно трущейся о колодку) и ступицы. Впервые диски, состоящие из двух частей, были предложены Brembo: в них ступица крепилась к ротору с помощью заклепок. Они назывались «полуплавающими» дисками, так как ротор был приклепан к коронке. В настоящее время полуплавающие тормозные диски мото ушли в прошлое, на смену им пришли плавающие диски, характерной чертой которых является ротор, свободно закрепленный со ступицей через специальные пистоны. Такой подход позволяет роторам «самопозиционироваться» и быть ещё более устойчивым к воздействию температуры.
Преимущества плавающего ротора над монолитным:
— устойчивость к температурам, связанная с низкой теплопроводностью, (тепло от ротора передается на коронку через пистоны)
— устойчивость коронки к ведению под действием температуры.
— низкая масса. Обычно, для облегчения коронку делают из более легкого материала, такого как алюминий.
Недостатки:
— высокая стоимость
— из-за передачи момента через пистоны тормоз теряет в начальной хватке
— расположенность к механическому износу пистонов
Предназначение отверстий в роторе:
— вентиляция ротора. Чем ниже температура ротора, тем меньше греется колодка, тем больше тормоз устойчив к перегреву, тем быстрее колодка восстанавливается. Эффективная вентиляция, как средство понижения температуры тормозной системы — одна из основных причин сложной геометрии отверстий в роторе.
— вентиляция суппорта и непосредственно тормозной колодки во время бездействия — отвод газов, образующихся во фрикционной пленке при экстремальном торможении. Как следствие — уменьшение эффекта увядания.
— служат абразивом для колодки. После торможения, колодка покрывается глянцевым слоем — окалиной. Этот слой должен удаляться. Отверстия в роторе выполняют роль абразива, удаляя глянец.
Чугунные диски (диски из серого чугуна)
Одни из наиболее широко распространенных роторов (90% стоковых роторов мотоциклов года выпуска ранее 2002г.) сделаны из серого чугуна различных сплавов. Трудность подбора колодки на этот ротор объясняется ещ╦ и разнообразием сплавов, используемых производителями мотоциклов. Типичные сплавы, используемые для изготовления роторов из серого чугуна, представлены в таблице:
Плотности сплавов варьируются от 7.15-7.2 гр/см 3 , температура плавления от 1150 до 1142 о С. Максимальная, безопасная рабочая температура ротора из серого чугуна: 800-900 о С (зависит от качества сплава, наличия дефектов в металле).
На практике, сплав ротора у каждого производителя — свой, кроме того, возможны вариации сплава не только от мотоцикла к мотоциклу, но и от года к году.
Роторы из серого чугуна работают на органических или полуметаллических колодках. Из-за недостатка прочности, роторы не рекомендуется использовать на жестких металлических колодках Sintered из-за чрезмерно износа.
Из сильных сторон — серый чугун обладает не только высокой теплоемкостью в сравнении с диском из нержавейки, но и втрое лучшей теплопроводностью. Эти качества обеспечивают ротору линейность и устойчивую работу на высоких температурах, благодаря быстрому равномерному разогреву ротора во всех точках. Один из ведущих производителей высококачественных чугунных роторов — Beringer.
Тормозные диски из ковкого железа
Менее распространенный тип дисков, выпускается компаниями BrakeTech, Spiegler, EBC (Pro), к сожалению, информация о точном составе железного ротора EBC Pro неизвестна, поэтому сюда он относится условно. Считается, что технологично выточенные диски из ковкого железа, прочнее литых роторов из серого чугуна, обладая схожими термическими характеристиками. На этих роторах могут использоваться как мягкие органические колодки, так и более жесткие — полуметаллические. Производители утверждают, что ковкое железо поглощает и рассеивает выделяемое тепло лучше, чем диски из нержавейки и серого чугуна, придавая тормозам линейность и устойчивость к увяданию. По словам гонщиков, использующих этот тип диска с металлизированными (Sintered) колодками — диски из ковкого железа обладают высокой устойчивостью к поводке и линейны, но колодки их быстро изнашивают. Тем ни менее, с точки зрения производительности, использование комбинации ковкое железо/ металлизированная колодка является одним из самых эффективных решений на сегодняшний день.
Тормозные диски из нержавеющей стали
Большинство дисков сделаны из аустенитовой нержавеющей стали.
Несмотря на меньшую теплоемкость стали, её плотность достигает — 7.93 гр/см 3 , а безопасная рабочая температура — 120 о С. Типичная жесткость аустенитовой нержавейки по бринеллу — 217.
Как правило, именно эти диски, рекомендуются производителями для колодок Sintered, т.к. только некоторые сплавы серого чугуна обладают той же износоустойчивостью, что и аустенитовая нержавейка.
Характерной особенностью стальных дисков является сильная начальная хватка на холодную, затем, в виду свойств материала (плохой теплопроводностью и теплоемкостью) диск сильно разогревается и наступает увядание.
Основные проблемы стального диска, напрямую, зависят от термических свойств нержавеющей стали. Высокая температура на его поверхности, ведущая к увяданию колодки и неравномерный прогрев ротора, ведущий к образованию неровностей на поверхности диска и как следствие — появление разрушающих вибрации. Из вышесказанного напрашивается жизненно важное условие для данного типа дисков — эффективное охлаждение ротора. А именно сохранение момента, свойственного первоначальной хватке на стальном роторе как можно дольше. В этом направлении и движутся производители.
Лепестковый тормозной диск мото из нержавеющей стали.
Тема вынесена в отдельный пункт, в связи с большим интересом со стороны мотолюбителей.
Диск, по большей степени, предназначен для работы со спеченной металлизированной колодкой. Необычная форма — не прихоть конструктора, а жизненная необходимость.
Основное преимущество лепестка перед обычным ротором — это лучшее охлаждение. Металлизированная колодка на стальном диске разогревается сильнее, чем серый чугун или ковкое железо.
Причина этому — низкая теплоемкость и теплопроводность. При всей прочности стального ротора — он имеет недостаток — более высокая рабочая температура на всех типах колодок, в особенности на спеченной колодке, на которой он и должен работать по замыслу. Поиски эффективного охлаждение стального ротора, напрямую ведущие к увеличению его прочности (устойчивости к ведению), эффективности торможения (сопротивление увяданию), привели к созданию лепесткового ротора. Кроме снижения рабочей температуры, лепестковый ротор ещё и легче обыкновенного, а лепестковая структура и прорези в роторе положительно сказываются на поведении колодки в момент её увядания.
Для ротора из серого чугуна — проблема с перегревом и последующим, неравномерным распределение тепла — отсутствует, поэтому мы вряд ли когда-нибудь увидим лепестковые роторы из серого чугуна.
Источник klassmoto.ru